機械加工の基本
发布时间2025-02-27 分类広報 浏览量1999
加工
近代的な製造業のコア技術として、機械加工は、旋盤、フライス盤、研削盤や金属、プラスチック、切削、研削、穴あけ、その他のプロセスのための他の専門的な機器、部品の幾何学的形状、構造寸法と表面仕上げの精密制御を介して、自動車エンジン部品から製造ニーズの全分野の航空宇宙精密部品であることを確認します。CNC技術と自動化された生産ラインの深い統合により、加工プロセスは、効果的に生産コストを制御しながら、加工効率を向上させるインテリジェントなプログラミング制御への伝統的な手動操作からの変換とアップグレードを実現しました。国際規格に厳格に準拠した品質管理システムは、工具の摩耗状態をリアルタイムで監視し、加工パラメータを最適化することで、大量生産における工程の安定性を保証します。インダストリー4.0の潮流のもと、機械加工はフレキシブルな生産とデジタル管理の方向へと進化し、複雑な部品のカスタマイズに信頼性の高いソリューションを提供しています。
数値制御加工
CNCマシニングは、工作機械の軌道を正確に制御するコンピュータ・プログラミングに依存しており、旋盤加工、フライス加工、中ぐり加工、その他の精密加工プロセスの自動実行により、金属、エンジニアリング・プラスチック、その他の原材料が、設計仕様を満たす複雑な部品に効率的に変換される。その核となる利点は、デジタルコマンド駆動の高繰り返し精度と多軸リンク機能にあり、医療機器の微細部品からエネルギー機器の大型構造部品まで、本格的な製造ニーズに適応することができる。現代のスマート工場は、CAMプログラミングシステムとオンライン検査装置を統合することで、加工パラメータの動的最適化と工具寿命のインテリジェントな予測を実現し、航空宇宙や自動車金型などのハイエンド分野での加工効率を向上させながら、大量生産における寸法の一貫性を確保する。IoT技術とデジタルツインモデルの深い応用により、CNC加工はクラウドベースの共同製造と適応プロセス調整の進化を加速し、インテリジェント製造エコロジーに重要な技術サポートを提供しています。
機械加工の分類
回転
工作物は旋盤主軸によって回転され、工具のラジアル/軸方向送り運動と組み合わされる。シャフト、ディスク、ブッシュなどの回転部品の内外円形加工を得意とし、自動車ドライブシャフト、油圧シリンダーバレルなどの大量生産で高効率切削の利点を発揮する、 アルミニウム CNC旋盤は、高温合金から幅広い材料で、ねじ切りや偏心構造の精密加工ができる。
ミーリング
垂直/水平フライス盤多刃工具回転切削の使用は、複雑な空洞、3次元曲面成形加工が可能で、パーティング面の金型インサートから関節のロボットジョイントに典型的なアプリケーションのシナリオであり、5軸リンクCNCフライス技術は、空間角の限界を打破するために、インペラ、プロペラ、および処理の分野で他の形状の部品はかけがえのないものです。
研磨
砥石粒子によるミクロン単位の材料除去は、焼入れ鋼、セラミックス、その他の超硬材料で鏡面精度を得るための究極のプロセスです。 精密スピンドル製造のベアリングレースや医療機器の人工関節の表面処理は、オンライン測定システムと恒温作業場の環境制御によってサブミクロンの寸法安定性を保証するこの技術に依存しています。
ドリル、リーマ、タッピング、その他の加工
基本的な貫通穴加工から精密ねじ成形まで、完全な穴加工ソリューションをカバーする深穴加工技術は、ガンドリル、石油・ガスパイプライン、その他の特殊なL/D比のニーズに対応し、複合工具の適用により、ドリル加工、リーマ加工、タップ加工を1回のクランプで完了できるため、エンジンブロック、油圧バルブブロック、その他の多穴部品の加工効率が大幅に向上します。また、次のような分野でもよく使用されている。 ダイカスト金型 製造。
加工設備
旋盤
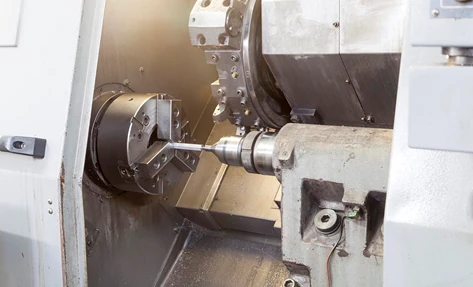
旋盤は回転体加工の核心設備として、主軸を駆動して棒状または円板状の工作物を高速回転させ、刃物台のラジアル・軸複合送り運動に合わせて、円筒旋削、面削り、ねじ切り加工を正確に完成させる。近代的なCNC旋盤は動力工具とY軸機能を統合し、ステンレス鋼、チタン合金などの難削材のフライス-旋盤複合加工を行うことができ、自動車カムシャフト、油圧バルブコアなどの精密部品の大量生産に広く使用されており、そのデュアルスピンドル設計は、自動化された連続加工を実現することができます。
マシニングセンター
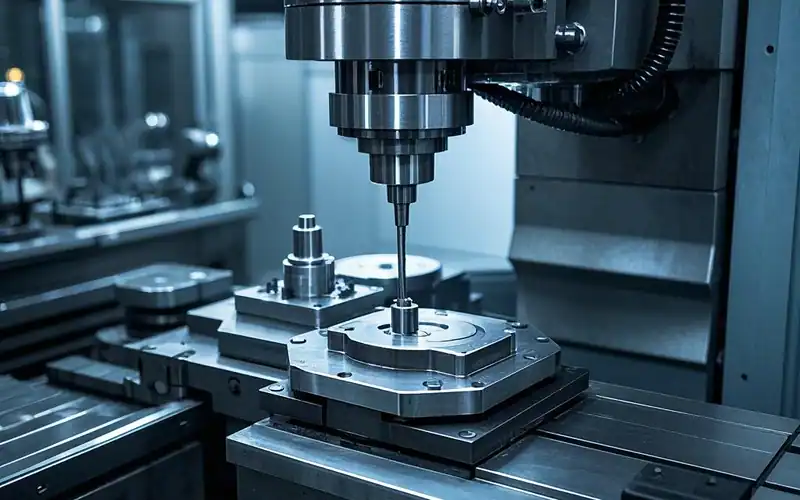
多軸リンクの空間加工能力により、フライス盤は垂直/水平スピンドルの助けを借りて、フェースフライスカッタ、ボールエンドカッタなどの工具を駆動し、複雑な形状の成形を実現し、5軸CNCフライス盤はテーブルのスイングにより空間角の制限を突破し、航空エンジンのブレードやプラスチック射出成形金型のインサートの三次元曲面加工で代替不可能性を発揮する。自動工具交換システムを備えたマシニングセンターは、粗加工から仕上げフライス加工まで、アルミ合金フレーム部品の全工程を一度に完了することができます。
ドリリングマシン
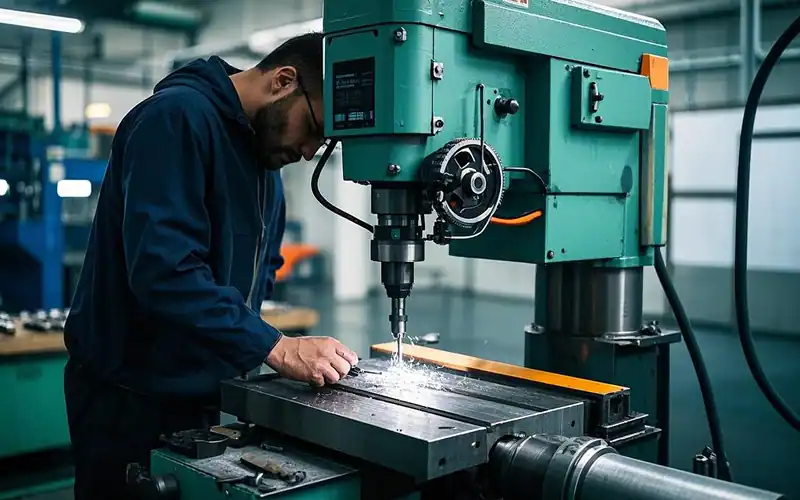
深穴加工分野のプロフェッショナル・ソリューション・プロバイダーとして、ボール盤はツイストドリル、深穴ドリルなどの工具を高速スピンドルで駆動し、正確な穴加工を実現します。高圧冷却システムを備えたガンドリル技術により、長さ対直径比30:1以上の深穴加工が可能です。インテリジェント・ドリリングセンターは、リーマ加工とボーリング加工のモジュールを統合し、エネルギー機器のチューブプレートや自動車のトランスミッションシェルなど、複数仕様の穴の効率的な加工要求に応え、ドリル摩耗のリアルタイム補正を実現するレーザー工具計測器を装備している。
グラインダー
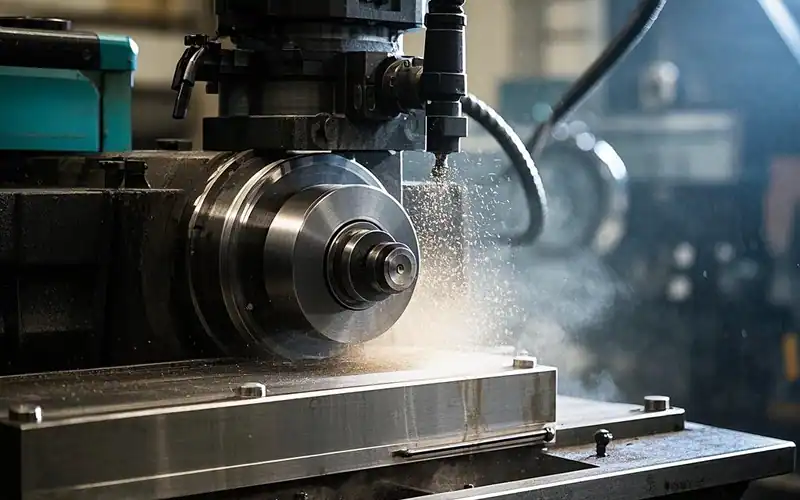
CNCプロファイル研削盤は、クローズドループフィードバックシステムにより、ベアリング軌道面やネジ山のミクロンレベルの輪郭精度を安定的に維持することができます。オンライン測定システムを備えたセンタレス研削盤は、光学機器のガイドピラーや油圧バルブのスプールなど、大容量の高精度部品の全自動研削ソリューションを提供します。
その他の機械加工設備
CNC工作機械
インテリジェント・マニュファクチャリングのコア・キャリアであるCNC工作機械は、多軸リンクを通じてCAMプログラミング・システムとシームレスに接続し、複雑な部品の3Dモデリング・データを精密加工コマンドに直接変換する。適応制御システムを搭載したインテリジェント工作機械は、切削力の変動や工具の摩耗状態をリアルタイムで検知し、産業用モノのインターネットプラットフォームと組み合わせることで、加工パラメーターのクラウドベースの最適化反復を実現し、自動車用金型、光学機器、その他の精密製造分野に柔軟な生産ソリューションを提供する。
レーザー切断機
高出力ファイバーレーザーとガルバノメーター位置決め技術により、非接触加工でステンレス、アルミ合金などの金属板をミクロンレベルの精密切断を実現し、インテリジェントモニタリングシステムにより、炭素鋼の酸化層を自動的に識別し、焦点位置を調整できるため、新エネルギー自動車バッテリートレイや電子部品ヒートシンクの加工効率が大幅に向上する。万ワットレーザー切断設備は、厚板切断のボトルネックを突破し、自動搬出入ロボットアームにより、建設機械と造船業に全天候型連続運転能力を提供し、熱影響部制御技術により、その後の精密部品の溶接品質を効果的に保証する。
ウォータージェット切断機
超高圧ウォータージェットとガーネット砂を混合したコールドカットプロセスを採用した水切断機は、熱変形がないという独自の利点により、炭素繊維複合材料や大理石形状の装飾部品の加工において、材料本来の特性を維持します。5軸ダイナミックカッティングヘッドは、空間角度補正技術により、タービンブレードや食品用プラスチック容器に施されたセラミックコーティングの3次元輪郭の正確な分離を実現します。 環境に優しい機能により、従来の切削加工で発生する粉塵公害を完全に排除し、医療消耗品や建築カーテンウォール業界における高水準の加工シーンに適したプロセスとなっています。
加工工程
切断原理
切断原理切削運動とは、主運動と送り運動を含む、工具と被加工物との間の相対運動である。
切断速度切削速度:切削速度とは、加工される被加工物の表面に対する、工具の刃先上の選択された点の主運動方向に対する瞬間的な速度のことである。
切り込み切込み深さとは、加工する面と加工される面との間の垂直距離のことである。
切削工具
切削工具材料: : 一般的に使用される工具材料には、高速度鋼、超硬合金、セラミックス、超硬材料などがあります。
工具形状先行角、後行角、主たわみ、キャンバーなどの工具の幾何学的パラメータは、切削力、切削熱、耐久性、被削材の表面品質などに影響を与える。
工具の研磨工具の研ぎには、砥石の選択、研ぎ工程、研ぎ品質の検査が含まれる。
切削油剤
切削油剤の役割切削油剤の役割には、冷却、潤滑、洗浄、防錆などがあります。
切削油剤の種類切削油の種類には、エマルジョン、合成油、切削油などがあります。
切削油剤の選択切削油剤の選定は、加工条件、ワークの材質、工具の材質などに基づいて行う。
加工工程
総体的な準備
部品の機械的特性に基づいて、ニアネットシェイプのブランクは、鋳造、鍛造または3D印刷によって準備され、熱間静水圧プレスプロセスは、チタン合金の航空宇宙構造部品の内部欠陥を除去するために使用され、アルミニウム合金のダイカストブランクは、ポロシティ率が<0.2%であることを保証するためにX線検出する必要があります。 インテリジェント製造ワークショップは、MESシステムを通じてブランクのバッチと加工順序を自動的に一致させ、原材料から粗加工までの全工程の追跡を実現します。インテリジェント製造ワークショップ
ワークの位置決め
6点位置決め原理を用いたモジュール式治具システムの設計により、油圧式拡張マンドレルは薄肉円筒部品の半径方向振れ精度0.005mmを確保し、五面体真空吸引カップは成形複合材料の非破壊クランプソリューションを提供します。新エネルギー自動車のモーターハウジングの加工には、レーザースキャンと適応型クランプ力制御技術が採用され、ブランクサイズの変動が位置決め基準に与える影響を補正します。
工具の準備
工具寿命を予測する切削シミュレーションデータに基づき、PVDコーティング超硬工具は高温合金の断続切削に対応し、ダイヤモンドコーティングドリルは炭素繊維複合材料のバリレス加工を実現します。インテリジェントツールマガジンは、RFIDチップを通して工具パラメータを自動的に識別し、マシニングセンターでの工具交換時に工具補正値を同期校正することで、自動車金型キャビティ加工の寸法一貫性を確保する。
加工
多軸CNC工作機械は、フルシーケンシャル加工戦略を導入し、複合旋盤センターは、航空機エンジンマガジンの内側と外側のプロファイル加工をワンクランプで完成させ、マイクロ潤滑技術は、インコネル718材の切削効率を40%向上させる。5軸マシニングセンターは、揺動フライス加工により深溝加工の工具寿命を3倍に延ばし、オンライン測定システムと連動して工具経路の偏差をリアルタイムで修正する。
ワーク検査
三次元座標測定機(CMM)は、デジタル検査閉ループを構築するために、ブルーライトスキャナは、タービンブレードブレードのプロファイルの偏差をキャプチャするために、工業用CTは、アルミニウム合金鋳物の内部収縮の非破壊検査。 CPK値の主要寸法のSPCシステム統計分析、99.7%の表面欠陥の識別精度のAI目視検査、検査データは自動的に電子品質ファイルを生成するためにQMSシステムにアップロードされます。
加工品質管理
加工誤差解析
オリジナルエラー: 工作機械、治具、工具、ワークピースそのものに関連するもので、製造誤差や組立誤差など。
処理エラー加工プロセスにおける様々な要因、例えば切削力、切削熱、工具摩耗などによる誤差。
検出エラー測定機器、測定方法、測定環境など、測定過程における要因に起因する誤差。
品質管理方法
予防的コントロール設計と工程管理を通じてエラーを減らし、製品品質を向上させる。
プロセス制御:: リアルタイムで処理を監視・調整することで、一貫した製品品質を確保する。
完成品検査完成品が指定された要件を満たしていることを確認するための検査と試験。
加工面の品質
表面粗さ: : 表面の微細な凹凸の高さで、部品の耐摩耗性や疲労強度に影響する。
表面リップル度: : 表面の波形の形と大きさで、部品の疲労強度と密閉性に影響する。
表面仕上げの質感表面加工には、部品の外観やはめあい精度に影響する跡やテクスチャーが残ります。
加工寸法精度管理
寸法精度機械加工された部品の実際の寸法が、指定された寸法に適合している度合い。
位置精度加工中の工作機械に対するワークピースの位置決め精度は、部品の組み立て精度に影響します。
リピートポジショニング精度工作機械の安定性と信頼性を反映する。
カスタム加工部品の開始
寧波Hersinは複雑な部品のためのワンストップCNC加工ソリューションを提供し、ラピッドプロトタイピングから大量生産までのフルサイクル精密加工サービスを提供しています。 5軸連動マシニングセンター、複合旋盤設備クラスターとスイスBaume超精密工作機械を頼りに、Hersinは自動車部品やその他の製品の生産に特化しています。図面を弊社のインテリジェント見積もりシステムにアップロードして、DFM最適化と工具摩耗分析を含む数理レポートを入手してください。お問い合わせ
加工設備安全規則
設備の立ち上げ前点検
油圧システムの圧力安定性(20~25MPa)と空気圧配管の密閉性を確認し、赤外線サーモグラフィでスピンドルモーターの巻線温度異常を検出し、CNCシステムのソフトリミットとハードリミットの二重保護設定をチェックする。5軸マシニングセンタの場合、回転テーブルのロック機構を追加検証し、レーザー干渉計でガイドウェイの位置決め精度の誤差≤0.02mmを検出し、炭素鋼の工作物をクランプするとき、磁気吸引カップの残留磁気強度が≤5ガウスでなければならない。
機器操作手順
SOPパラメータ設定仕様を厳守する:鋳鉄の荒フライス切削速度は150-220m/分に制限され、超硬工具の送り速度はap=2mm×ae=35mmの勾配に従って調整される。チタン合金を加工する場合、微量潤滑(MQL)システムを作動させ、切削エリアの煙の濃度を監視し、オペレーターは耐衝撃マスクと難燃性の衣服を着用し、スピンドルの過負荷アラームが発生した場合、直ちに非常ブレーキボタンを作動させなければならない。
シャットダウン後の機器のメンテナンス
切削液タンク内の金属屑をクローズドループで洗浄し、pH値(8.5-9.2)を検査し、超音波洗浄機を使用して、工具シャンクのテーパ面のミクロンサイズの油膜残留物を除去する。毎月ボールねじのバックラッシュ補正を行い(C3級精密ねじ補正≤0.015mm)、振動スペクトル分析を通じてスピンドルベアリングの寿命を予測し、グリース充填量は±0.5mlの精度である。
加工事故のケーススタディ
事故事例 I
ある自動車部品工場CNC旋盤主軸過熱火災:オペレーターがステンレス鋼連続旋削のクーラント停止に違反し、切削温度が900℃を超え、燃料ミストが発生した。事故後、赤外線画像監視システムを設置し、PLCに切削熱力学モデルを組み込んで温度-速度連動制御を実現することが必須となった。
事故事例 II
ガントリーフライス盤保護ドアインターロック故障の原因障害:機器の改修遮蔽安全格子信号、5ミリメートルアクリルバッフルを介して鉄粉スプラッシュ。整流プログラムは、圧力感知フロアマットと二重回路のグレーチングの保護レベルIP67にアップグレードされ、トリガ応答時間≤0.3秒。
機械加工の開発動向と課題
加工技術の開発動向
- デジタルツインドライブ:工作機械の状態をクラウドにリアルタイムマッピング、加工誤差予測精度99.2%
- 複合加工革命:旋盤、フライス、中ぐり、研削の各装置を統合することで、クランプ回数を減らし、インペラ加工のサイクルタイムを60%短縮
- グリーン・マニュファクチャリング:水素切断技術がエマルションに取って代わり、カーボンフットプリントを45%削減
機械加工業界が直面する課題
- 高スキル人材の障害:37%の5軸プログラミング技術者不足、ギャップを埋めるためにARリモートガイドシステムの必要性
- 超硬素材加工のボトルネック:炭化ケイ素ミラー加工の工具寿命はわずか15分、プラズマアシスト切断技術のブレークスルーが急務
- データ・セキュリティのリスク:CNCシステムの脆弱性によるGコードの改ざん、ブロックチェーンによる暗号化通信が必要
機械加工技術発展の展望
量子計測技術は寸法検査精度をナノメートルレベルまで向上させ、AIの自己進化型アルゴリズムは切削パラメータの動的最適化の効率を300%向上させる。2030年までに、ブレイン・コンピュータ・インターフェイスをベースとした工作機械のジェスチャー制御とゼロエミッションのドライマシニングセンターがハイエンド製造の標準となり、マイクロファクトリーモデルは航空宇宙のサプライチェーンを再構築する。