ラピッド・ツーリング:製品開発と製造を加速する革新的ソリューション
发布时间2025-02-14 分类広報 浏览量1738
急速な技術革新の時代にあって、製造業は「規模第一主義」から「機敏で効率的」へと大きく変貌を遂げようとしている。ラピッド・ツーリング(Rapid 序文:中国の金型製造のジレンマとブレークスルー
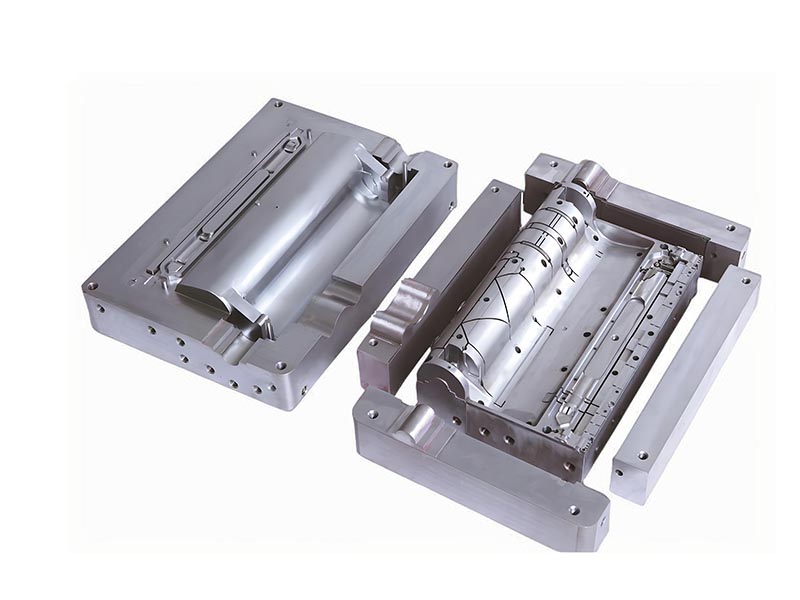
私(何欣)は23年間鋳造業に深く携わってきたエンジニアとして、中国が金型の輸入大国から自主革新国家へと変貌していくのを目の当たりにしてきました。金型産業が集まる寧波で、私たちは伝統的な鋼鉄金型の開発サイクルが長く、試行錯誤のコストが高いという苦痛を経験し、同時に、急速な金型技術がもたらした革命的なブレークスルーも経験した。本稿では、高圧鋳造を組み合わせる、 低圧鋳造 におけるラピッドツーリングの役割を明らかにした。 アルミニウム 部品製造における重要な技術的論理。
1.高速金型の本質:妥協ではなく、正確なマッチング
1.1 伝統的な金型の3大苦悩点
- 時間コスト高圧鋳造の鋳型は、開発に8~12週間かかることがあります。
- 金融圧力自動車エンジンケーシングの金型費用200万ドル超
- 試行錯誤のリスク:: 重力鋳造 金型の構造変更にはさらに15万ドルかかる
1.2 ラピッドツーリングの技術的方向性
材料科学、加工技術、シミュレーション技術の3つの革新によって達成された:
- サイクル・コンプレッション 70%設計から試作まで最短7営業日
- コスト削減 50%-80%アルミニウム金型のコストは8万ドルから15万ドルに抑えることができる。
- 試作量の正確なマッチング500個から30,000個までのパイロットプラントをサポート。
2、4つの主要な鋳造工程のための高速金型ソリューション
2.1 高圧鋳造(HPDC)のシナリオ
高圧鋳造は、680~720℃の溶融アルミニウム合金スープを、1600~2000Tのクランプ力の下、10~50m/sの速度で金型キャビティに押し込むプロセスであり、金型が極度の熱機械的負荷に耐えることが核心的な課題です。このシナリオにおけるラピッドツーリングの革新は、材料と構造の二重の最適化に反映されています。従来のH13鋼の代わりにQRO90熱間加工鋼が使用され、そのモリブデン-バナジウム合金組成により、熱疲労耐性が40%向上し、表面の窒化処理(層深さ0.2-0.3mm)と合わせて、金型寿命を3万サイクル以上に延ばすことができます。モジュール式インサートシステムの構造設計は、脆弱な部分(ゲート、エジェクタピンの位置など)の局所的な補強のために、寧波の会社、新エネルギーモーターエンドカバーの生産は、インサートの迅速な交換を介して、金型のメンテナンス時間を8時間から1.5時間に短縮する。経済面では、1個あたりのコストは従来の金型の18.6円から7.3円に削減され、開発サイクルは12日に圧縮され、特に年間生産量が5万個以下の自動車構造部品プロジェクトに適している。
技術的な問題::
- 金型は1600Tのクランプ力に耐える必要がある。
- アルミニウム合金は最高700℃の温度で溶融する。
- モジュール寿命要件 >50,000 サイクル
ラピッドツーリングソリューション::
- 素材のアップグレード従来のH13鋼からQRO90熱間加工鋼への置き換え
- 構造の最適化インサートは、重要な部分を局所的に補強するためにコアに使用される。
- リアルタイムデータ中国・寧波で金型寿命32,000回の5G基地局用ヒートシンク筐体。
2.2 低圧鋳造(LPDC)のシナリオ
低圧鋳造は0.5-0.8MPaの空気圧でアルミ液をスムーズに金型キャビティに注入し、特に高密度を必要とする薄肉部品の生産に適している。トポロジー最適化技術によって設計された注湯システムは、充填時間を9.2秒から6.8秒に短縮し、金属の利用率を12%向上させた。高速ツーリングソリューションは、プリハードン鋼P20+ローカル銅合金インサートを採用し、ツーリングコストを従来のソリューションの45%に削減します。 航空宇宙用油圧ハウジングのような複雑な構造部品のパイロットテストに特に適しており、一般的なプロジェクトのリードタイムは15~20日で、3,000~8,000個の小ロット生産に対応しています。
技術的ブレークスルー::
- 特殊金型温度制御システムの開発(精度±2)
- 勾配冷却チャンネル設計
- 判例新エネルギー自動車モーターハウジングプロジェクトで、製品収量が78%から93%に増加した。
2.3 重力キャスティング・シナリオ
重力鋳造は金属液の自重充填に頼っており、大型で複雑な部品の生産によく使われている。第一に、3D印刷砂型と金型の複合技術、SLSプロセスで砂型コア(精度CT8レベル)を鋼鉄外型と組み合わせて生産することで、エンジンシリンダーブロックの試作サイクルを45日から12日に短縮しました;第二に、ヒートバランス制御システム、金型の主要部分に銅合金インサート(熱伝導率380W/m・K)を埋め込み、舶用ディーゼルエンジンのシリンダーヘッドの温度勾配を40%に低減しました;第三に、インテリジェント排気設計、多孔質金属を使用することで、シリンダーヘッドの温度勾配を40%に低減しました。温度勾配は40%減少した。第三に、インテリジェントな排気設計で、従来の排気溝の代わりに多孔質金属ベントプラグを使用し、鋳造ポロシティ欠陥率を15%から3%未満に減少させた。経済データによると、迅速鋳型プログラムの試用鋳型の数が平均2.3倍削減され、1つの試用鋳型のコストが1.2~1.8万元節減され、特に1つの鋳型の重量が50kg以上の大型建設機械部品の開発に適している。
革新的な実践::
- 3Dプリント砂型と金属型の組み合わせ技術
- 熱バランスを改善するために銅合金を局所的にはめ込む
- 経済効果注湯システムの最適化により、鋳型試行回数を40%、サイクルタイムを65%短縮。
3、急速金型の5つのコア技術
3.1 素材選択マトリックス
アプリケーションシナリオ | 推薦資料 | 硬度(HRC) | 熱伝導率 (W/m-K) | コスト指数 |
---|---|---|---|---|
高圧鋳造 | H11+表面窒化 | 48-52 | 24.3 | ★★★★ |
少量のアルミニウム合金 | 7075航空宇宙用アルミニウム | 35-40 | 130 | ★★★ |
高精度構造部品 | S7工具鋼 | 54-56 | 29.4 | ★★★★☆ |
3.2 表面処理プロセスの比較
- マイクロアーク酸化10~30μmのセラミック層形成、耐熱温度800℃以上
- DLCコーティング摩擦係数を0.1に低減し、工具寿命を3倍に延長。
- 実例ターボチャージャーのシェル金型に複合コーティングを施し、金型寿命は8万回を超えた。
3.3 寿命予測モデル
Moldflowのシミュレーションデータとフィールドモニタリングに基づく:
L=K× (σaピープルiedσUTS)m×Nthいいえマl
そのうちのひとつだ:
- K材料定数(アルミニウム合金は0.8~1.2)
- m疲労指数(スチール金型は6.5、アルミ金型は4.2)
- 応用例予測誤差±8%以内
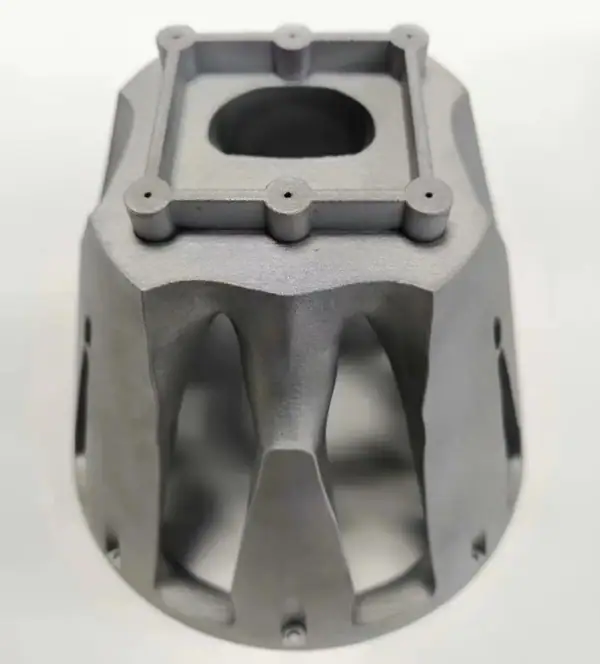
3Dプリンティング・ラピッドプロトタイピング
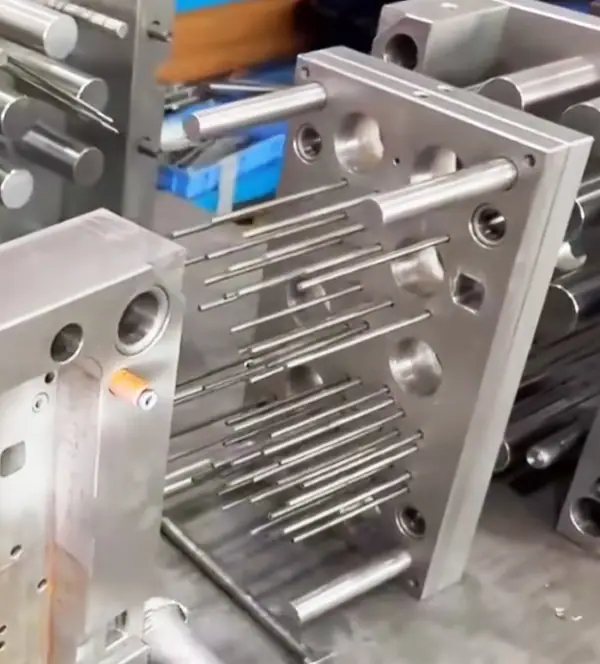
ラピッド・ツーリング
4、3Dプリンターと迅速な金型イノベーションの統合
勾配材料印刷技術は、コア表面のHRC55高硬度とコア内部のHRC35高靭性の組み合わせを実現することができる。勾配材料印刷技術は、コア表面のHRC55の高硬度とコア内部のHRC35の高靭性の組み合わせを実現することができ、ドローンブラケット金型はこの技術で処理され、耐衝撃性が60%向上した。経済分析によると、5以上の形状の水路を持つ複雑な金型では、3D印刷ソリューションの総コストは、CNCに比べて42%削減することができ、これは特に医療用マイクロ流体チップ金型のような精密なシナリオに適している。現在の技術的な限界は、最大造型サイズ(ほとんどのデバイスは500mm以下)と後処理要件(主要な嵌合面は依然としてCNC仕上げが必要)にあるが、マルチレーザー技術の発展により、2025年にはメートルスケールの金型の全体的なプリントを実現できると予想される。
4.1 技術的ブレークスルーのポイント
- コンフォーマル・クーリング・チャンネル射出サイクルタイムを23%短縮し、変形を40%低減。
- グラデーション印刷コア表面硬度HRC55、内部靭性HRC35
- ケースデータLEDランプシェード金型冷却効率37%向上
4.2 経済分析
規範 | 従来のCNC金型 | 3Dプリント金型 |
---|---|---|
開発サイクル | 18日 | 6日 |
複雑な構造コスト | 100% | 65% |
修正費用 | 30% | 8% |
5.製造企業への3つの実践的提言
- 金型グレーディング・システムの確立::
- クラスA金型(10万個以上):従来のスチール金型
- クラスB金型(10,000~50,000個):高速スチール金型
- クラスC金型(10,000個未満):3Dプリンティング/アルミ金型
- デジタル・ツインの導入::
- 金型設計段階でのMAGMAシミュレーションシステムの導入
- 生産段階での応力分布を監視するためのIoTセンサーの設置
- 迅速な対応メカニズムの構築::
- 標準化されたモールディングの予備ライブラリ(80%共通仕様をカバー)
- 地域協力ネットワークの構築(寧波は2時間のサプライチェーンサークルを形成している)
結論:金型産業の次の10年
私たちは寧波金型クラウドプラットフォームプロジェクトを実施し、高速金型はインテリジェント化し、サービス化する:
- インテリジェント見積システムパラメータを入力して金型ソリューションを生成するのに5分かかります。
- ブロックチェーントレーサビリティライフサイクル品質トレーサビリティ
- 共有金型ライブラリー中小企業30%在庫コストの削減
ラピッド・ツーリングよくある質問(FAQ)
Q1:ラピッド・ツーリングは大量生産に使えますか?
A: シナリオに基づいた評価が必要です:
- アルミ合金金型:小ロット<5000個>に最適
- プリハードン鋼金型:30,000~50,000個対応可能
- カビの状態をリアルタイムで評価するため、デジタル監視システムを組み込むことを推奨する。
Q2:ラピッドツーリングの寸法精度を管理する方法は?
A: 推奨プログラムです:
- 加工段階:5軸工作機械を使用+インライン測定(精度±0.02mm)
- 金型試作段階:三次元測定機(CMM)による重要寸法の全数検査
- 量産段階:500型ごとにサンプリングとテスト
Q3:ラピッドツーリングの表面処理における革新的な技術とは?
A:3つの最先端技術:
- レーザークラッディング:40%のコスト削減で摩耗箇所を補修
- ナノコンポジット・コーティング:摩擦係数を0.08に低減
- プラズマ窒化:表面硬度HV1200まで
Q4: 3Dプリント金型の限界は何ですか?
A: 現在の主な制限:
後処理要件:重要な合わせ面のCNC仕上げが必要になることが多い。
最大サイズ:ほとんどのデバイスは500×500×500mmに制限されています。
材料の選択:現在、金型鋼、アルミニウム合金が主な支持材料となっている。