アルミダイカスト金型設計:プロセスから最適化までの実践ガイド
发布时间2025-02-15 分类広報 浏览量2748
寧波禾欣のシニア・エンジニアとして、20年以上鋳造業界に深く携わってきた私は、アルミニウムの製造工程を熟知している。 ダイカスト金型 製造業におけるコアポジション。自動車部品であれ、3C電子製品であれ、航空宇宙部品であれ、アルミダイカストの高効率と高精度のプロセスは、金型設計の微妙なサポートと切り離せません。本稿では、アルミダイカストの金型設計のポイント、技術動向、最適化戦略について、実務経験と体系的な分析を組み合わせ、業界関係者に実践的なガイドを提供します。
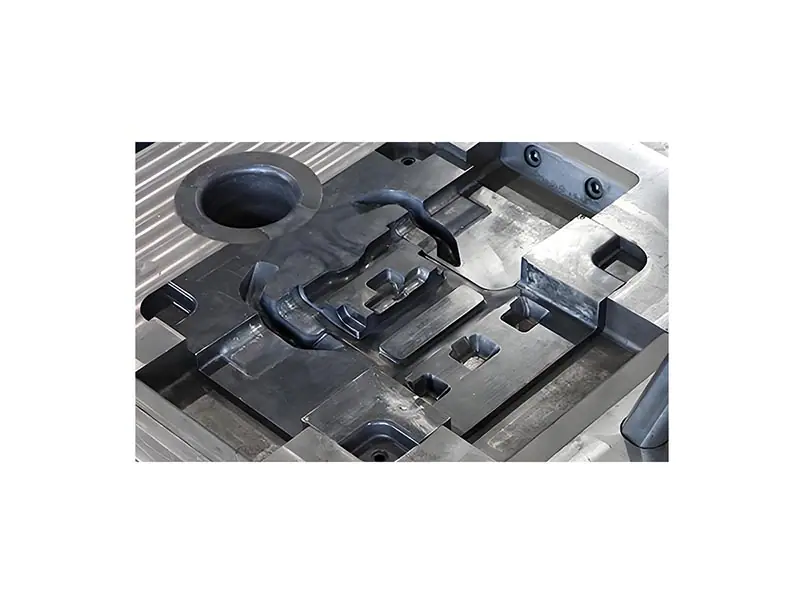
アルミダイカスト金型のコアバリュー:それがプロセスの成否を分ける理由
ダイカスト金型は金属成形の "型 "であるだけでなく、生産効率や製品の品質にも影響する。決め手このプログラムの重要性は3つある。その重要性は3つの分野に反映されている:
- 正確な精度
金型のキャビティ設計は、鋳物の寸法公差(通常±0.1mm)と表面仕上げ(Ra 1.6~3.2μm)を直接決定する。例えば、自動車エンジンブロックダイカストでは、金型冷却システムの設計が不合理であれば、局部収縮が不均一になり、気孔や変形を誘発します。 - 高い生産効率
一組の最適化された多数個取り金型は生産効率を300%以上高めることができる。ある新エネルギー車のモーターシェルプロジェクトを例として、4個取り金型を採用した後、1時間当たりの生産量は15個から60個に跳ね上がり、歩留まりは98%以上に安定した。 - コストメリット
金型の寿命は部品単価に直接影響します。金型にH13熱間加工鋼を使用することで、表面TD処理(熱分散法)により、金型の寿命を10万から50万まで延ばすことができ、共有コストを大幅に削減することができます。
アルミダイカスト金型の5大タイプと選択戦略
金型タイプ | 適用シナリオ | コストサイクル | 技術的特徴 |
---|---|---|---|
試作金型 | 小ロット検証(500個未満) | 低コスト/2~3週間 | 3Dプリンティング加工複合プロセス |
ラピッド・ツーリング | パイロット生産(500~5000個) | 中コスト/4~6週間 | レーザークラッディング積層造形 |
ユニット金型 | 多品種少量生産 | モジュール設計 | キャビティ・インサートの迅速な交換 |
生産金型 | 大量生産(10万個以上) | 高額/8~12週間 | マルチスライダー構造+ポイント冷却システム |
トリミング金型 | バリ取りとランナ分離 | に必要である。 | 油圧サーボドライブ+精密ガイダンス |
推薦セレクション::
- 高圧ダイカスト(HPDC)エアホールを減らすため、真空システムを備えた生産金型を優先する;
- 薄肉複雑部品(携帯電話のセンターフレームなど) 迅速な金型製作と、現地でのスクイーズ鋳造技術の併用を推奨する;
- 多品種フレキシブル生産ユニット金型を使用すれば、切り替え時間を30分未満に短縮できる。
アルミダイカスト金型設計の6つの黄金律
- フラクタル・ラインの最適化
パーティングラインは、重要な機能面を避けるべきである。例えば、5G基地局のラジエーターは曲面パーティングを使用し、非接触面にバリを発生させ、後加工コストを削減している。 - 流路システムの流体力学的設計
採用テーパークロス・スプルー(入口8mm→出口4mm)、30°の内側ゲート角度と共に、アルミ液のスムーズな充填を達成し、乱流による酸化スラグを避けることができます。 - 冷却システムのヒートバランス制御
コア部にはベリリウム銅インサート(熱伝導率210W/mK)を埋め込み、モールドサーモスタットで勾配温度制御(ゲート部250℃→端部180℃)を行うことで、冷却時間を20%短縮した。 - 脱型傾斜の科学的計算
合金の収縮率(ADC12では約0.6%)と表面の要求に応じて、外壁の勾配は1°~1.5°とされ、深いキャビティ部品では2°~3°に増加する。例えば、UAVシェルの深いキャビティ構造では3°の勾配が使用され、射出抵抗は40%減少します。 - 排気タンクとオーバーフロータンクの正確なレイアウト
最終充填エリアには段付きオーバーフロータンク(深さ0.3mm→0.8mm)が設置され、真空バルブ(真空度≦50mbar)により空隙率を0.5%以下に制御することができる。 - 金型材料の高度な選択
- レギュラーパーツ:H13スチール(硬度48~52HRC)
- 高耐摩耗性要件:ダイバール鋼(コバルトおよびモリブデン添加)
- 耐食シーン:STAVAX ESR(鏡面研磨 Ra 0.05μm)
業界の最先端技術:デジタル化とインテリジェンスが金型のアップグレードを後押し
- AIシミュレーション主導の設計反復
AnyCasting/MAGMAソフトウェアを使用することで、充填-凝固-応力シミュレーションの全プロセスを48時間以内に完了することができ、収縮のリスクを事前に予測することができます。ギアボックスのシェルプロジェクトでは、シミュレーションによってゲート位置を最適化し、金型の試行回数を3回削減しました。 - 3Dプリンターによるコンフォーマル冷却水路
成形水路の製造にSLM(Selected Zone Laser Melting)技術を使用することで、金型の温度差を±5℃以内に制御することが可能になり、サーマルノットが大幅に減少した。LEDランプシェード金型の適用後、サイクルタイムは18%短縮された。 - モノのインターネット(IoT)金型監視システム
温度/圧力センサーが金型の要所に埋め込まれ、キャビティ表面の状態をリアルタイムで監視します。型締力の異常な変動(>5%)が検出されると、バッチ不良を回避するための早期警告が自動的に発せられます。
ケーススタディ:新エネルギー車用バッテリートレイ金型の最適化
挑戦::
- 製品サイズ1200×800mm、平均壁厚2.5mm、気密性≤0.5Pa・m³/sが必要
- 初期歩留まりはわずか65%で、主な欠陥は冷間偏析と変形である。
処方::
- ダブルゲートのタンジェンシャル供給によるバランスの取れた充填経路
- ダイナミックな温度制御のために12セットのパルス冷却管を埋め込んだ金型コア
- バランスの取れたリリース力のための窒素ガススプリングを備えたエジェクターシステム
成果主義::
- 収量は92%に向上
- プロダクション・ビートが180秒台から140秒台に短縮
- 金型寿命は30万回を超える
よくある質問(FAQ)
Q1:金型サプライヤーの技術力はどのように評価するのか?
- 主な指標:過去の症例のCpk値(1.33以上)、CAE解析能力、試験金型報告書の完全性。
Q2:金型の表面コーティングはどのように選べばいいですか?
- 従来:CrNコーティング(硬度2200HV)
- 高耐摩耗性:AlCrN(耐熱温度900)
- リリース向上:DLCダイヤモンド・ライク・コーティング
Q3: 金型メンテナンスのベストプラクティスは?
- 毎日:シンブルの潤滑をチェック(高温用グリースNLGIグレード2を使用)
- 金型5000個ごと:EDMで軽度のひび割れを修復
- 金型サイクル50,000回ごと:一体型焼戻し処理(550℃×2時間)
結語
アルミダイカスト金型の設計は科学と芸術の結合であり、厳密な工学計算を必要とし、豊富な実務経験に頼っている。デジタル技術が深く浸透するにつれて、金型業界は「知能設計-精密製造-予知保全」という新しいパラダイムの到来を迎えている。実務者として、コスト、効率、品質のトライアングルゲームをリードする唯一の方法は、イノベーションを受け入れ続けることである。
カスタマイズされた金型ソリューションや技術的なアドバイス コンタクト歓迎 寧波Hersin鋳造チーム - 20年の経験で、我々は究極の精度とパフォーマンスであなたの製品を強化します。