ダイカスト技術:ビジョンを現実にするための重要な製造工程
发布时间2024-12-24 分类広報 浏览量2343
現代の製造業において、ダイカストプロセスは精密金属部品を製造する重要な手段とみなされている。ダイカストは、溶融金属を高圧で精密金型に注入することにより、複雑な形状の金属部品を製造することができ、自動車、エレクトロニクスなどの分野で広く使用され、いくつかの主要産業の技術発展を支えている。本稿では、ダイカスト・プロセスのコア・プロセス、材料選択、アプリケーションを詳細に分析し、このプロセスがいかにして製造における革新と卓越性を達成しているかを紹介する。
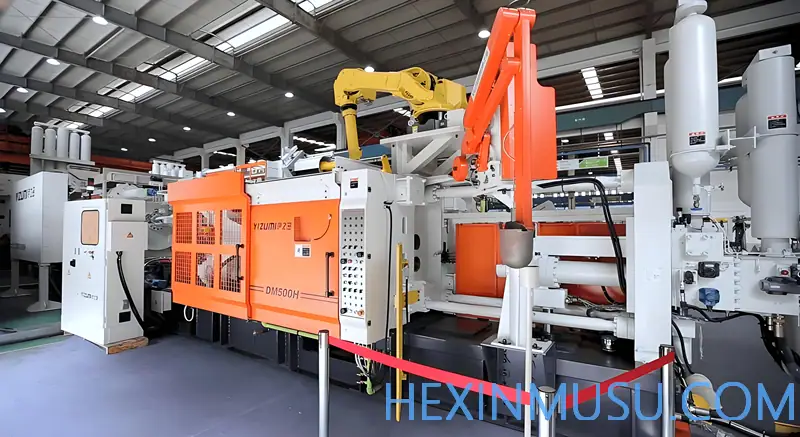
ダイカストとは何か?
ダイカストは、再利用可能な金型を使用して複雑な形状の金属部品を製造する、効率的で正確な金属鋳造方法です。従来の鋳造プロセスとは異なり、ダイカストは溶融金属を高圧で金型に注入するため、特に大量生産に適しており、高い精度、再現性、優れた表面仕上げが得られます。
ダイカスト・プロセスは当初、印刷産業で使用されていたが、その普及の可能性はすぐに自動車、航空宇宙、エレクトロニクス産業など多くの分野に拡大した。今日、ダイカストは主にアルミニウム、亜鉛、マグネシウムなどの軽金属を使用し、小型の複雑な部品から重要な自動車部品まで、幅広い製品の製造ニーズに対応している。ダイカストの核となる利点は、非常に厳しい公差で部品を作ることができることと、その後の機械加工の必要性を減らすことができることであり、現代の製造業に欠かせない技術となっている。
ダイカストプロセス
ダイカストの製造工程は、いくつかの重要なステップに分けることができる:
- 金型の準備
金型はダイカストプロセスの基礎であり、一般的な金型の種類には、単一キャビティ金型、マルチキャビティ金型、コンビネーション金型などがあります。金型設計は部品の複雑さと生産規模を考慮する必要があり、金型は亀裂や熱欠陥を避けるため、使用前に洗浄と予熱を行う必要があります。 - 射出工程
射出工程では、溶融金属は異なるシステムで溶解され、鋳型に注入される。ホットチャンバー方式の場合、溶融は鋳造機内で行われ、コールドチャンバー方式は溶融金属をコールドチャンバーに注ぎ、そこで圧力をかけて鋳型に注入します。 - 冷却と凝固
溶融金属は金型内で冷却・凝固され、最終的な部品が形成される。冷却工程では、収縮による部品の欠陥を防ぐため、圧力を制御する必要がある。 - せりだす
金属が完全に凝固すると、金型が開かれ、機械のエジェクターが部品を押し出す。 - トリミングと後処理
部品の品質を確保するためには、余分な材料やバリを取り除く必要がある。必要であれば、研削などの後処理によって、部品の精度をさらに向上させることができます。
ダイカストの種類
ダイカスト鋳造工程は、溶解と射出工程によって、ホットチャンバーダイカストとコールドチャンバーダイカストの2種類に大別される:
- ホットセルダイカスト
亜鉛や特定の金属のような低融点金属に適している。アルミニウム.このプロセスでは、ダイカストマシンに接続された溶融金属リザーバーを通して金型に金属を注入するために空気圧プランジャーを使用する。効率的で速く、小型部品の大量生産に適しており、家電製品の生産によく使われる。 - コールドルームダイカスト
アルミニウムや銅合金などの高融点金属に使用される。コールド・チャンバー・ダイカストでは、まず溶融金属をコールド・チャンバーに注入し、次にプランジャーを通して金型に注入する。このプロセスは、高い強度と耐熱性を必要とする部品に適しており、自動車や航空宇宙用途で広く使用されている。
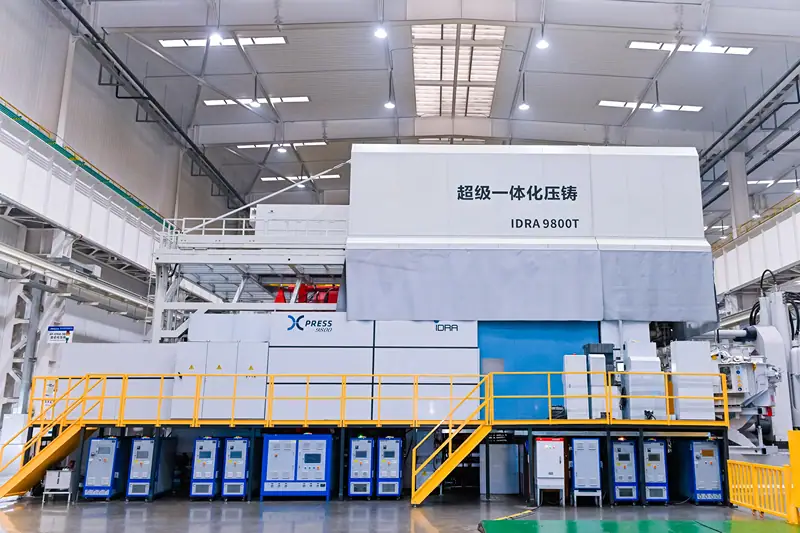
ダイカストのバリエーションと革新
技術が進化し続けるにつれ、ダイカスト鋳造プロセスは、さまざまな産業ニーズに対応するため、さまざまなバリエーションや技術革新を遂げてきました。例えば
- 重力ダイカスト溶融金属は重力を利用して鋳型に注入されるため、精密鋳造品の大量生産に適している。
- 圧力ダイカスト低圧または高圧による金属の充填。自動車部品や航空宇宙部品など、高精度が要求される部品の製造に適しています。
- 真空ダイカスト空気の滞留を少なくし、高級品に適した真空環境を作ることで、表面品質と寸法精度を向上させます。
- 押出ダイカスト部品の機械的特性と精度を向上させることができ、自動車部品によく使用される。
- セミ・ソリッド・ダイカスト特殊な鋳造温度により、複雑な形状の部品をより高い精度と強度で製造。
ダイカストのメリットとデメリットの比較
工業生産で広く使われている製造工程である金属ダイカストの利点は、大量生産において重要なものとなっている。しかし、ダイカストには、特定の応用場面での使用に影響を及ぼす可能性のあるいくつかの限界もあります。ダイカストの主な長所と短所、およびその原因を以下に分析する:
ダイカストの利点
- 優れた寸法精度
金属ダイカストは寸法精度の高い部品を製造することができ、特に厳しい公差が要求される用途に適しています。精度は金型の設計と製造工程に依存し、特に5軸CNCマシンなどの高精度CNCマシンを使用して金型を製造する場合、より高い寸法精度を達成することができます。さらに、低圧ダイカスト(LPDC)や重力ダイカストなどのプロセスバリエーションを使用することで、金型を正確に充填することができ、部品の精度が向上します。 - 複雑な幾何学
ダイカスト鋳造は、鋳物や薄肉などの複雑な形状の部品を製造することができる。この特徴により、ダイカスト鋳造は、航空宇宙、自動車、家電製品などの分野で、複雑な構造と幅広い機能を持つ部品を製造することができるようになりました。このようにして、設計者はより多くの機能を一つの部品に統合することができ、その後の組み立ての必要性を減らすことができる。 - 大量生産による短納期
ダイカストは、大量の部品を製造するのに適した大量生産プロセスである。高圧鋳造では、使用する圧力が高いため生産速度が速く、部品1個あたりの生産コストを削減できます。特に組み合わせ金型の場合、複数の部品を同時に製造できるため、部品あたりの生産性と費用対効果が向上します。 - 滑らかな表面仕上げ
ダイカスト工程で金属に高圧が注入されるため、鋳造された金属部品は通常、滑らかな表面仕上げになります。低圧鋳造,重力鋳造などの工程で使用される。この高品質な表面処理は、部品の外観を向上させるだけでなく、その後の表面処理に要する労力を軽減する。 - 長い金型寿命
ダイカスト金型これらは通常、高温・高圧に優れた耐性を持つ高品質の鋼鉄で作られている。このような強靭な鋼材により、金型は長時間の使用に耐え、耐用年数が長いため、金型の交換頻度を減らし、長期生産のためのメンテナンスコストを削減することができます。
ダイカストの欠点
- 非鉄金属のみ
ダイカスト鋳造法は、主にアルミニウム、亜鉛、マグネシウムなどの非鉄金属に適用される。これらの金属は融点が中程度であり、高圧下で金型に注入することが容易である。しかし、鋼や鉄のような融点の高い鉄系金属には、ダイカストは適していません。鋼や鉄のような金属を鋳造するには、特殊な設備とより複雑な工程が必要となるため、ダイカストの用途はやや限定される。 - 高い金型コスト
ダイカスト鋳造用金型は、製造コストが高い。数値制御加工金型を作るとなると、その工程は複雑でコストもかかる。特に複雑な部品を製造する場合、高品質の鋼鉄製の金型を使用すると、さらにコストが上がります。ダイカスト・プロセスは大量生産に適していますが、小ロットや複雑な部品の場合、金型のコストが制限要因となることがあります。 - 欠陥への敏感さ
生産工程におけるダイカスト鋳造部品は、気孔、収縮、気孔およびその他の欠陥が現れることがあり、特に高圧鋳造では、これらの欠陥がより一般的である。例えば、鋳造工程中の空気の滞留により、部品表面に気孔が生じ、この気孔が熱処理中に気泡を形成し、部品の品質に影響を及ぼすことがある。このような欠陥に対処するために追加の表面仕上げ工程が必要となり、製造コストが増加する可能性がある。 - 小規模生産には不向き
ダイカストは大規模生産に適しているが、初期投資、特に金型製造や設備立ち上げなどの固定費が高い。そのため、ダイカストプロセスは通常、小規模生産や1回限りの部品生産には適していない。小規模生産の場合は、他のプロセス(射出成形やCNC機械加工など)の方が適している場合があり、コストと生産リードタイムを削減できる。
ダイカストにおけるハーシーの金属材料
ダイカストプロセスで使用される金属材料は、通常アルミニウム、マグネシウム、亜鉛などの非鉄合金です。これらの合金は異なる性能特性を持っており、異なるアプリケーション要件に適しています。次の表は、一般的なダイカスト合金の詳細な比較で、主な組成、融点、特性、典型的な用途を列挙しています。
合金 | 一般的なサブタイプ | ベース | 融点 (°C) | 主な特徴 | 典型的なアプリケーション |
---|---|---|---|---|---|
アルミニウム | A380、A360、A390、A413、ADC12 | アルミニウム(Al)、銅(Cu)、ケイ素(Si)、マグネシウム(Mg) | 577 - 660 | 軽量、耐腐食性、高強度、良好な加工性、費用対効果。 | 自動車(エンジン部品、ホイール、シャシー)、航空宇宙(構造部品、ハウジング)、エレクトロニクス(ハウジング、ボディ) |
マグネシウム合金 | AZ91D、AM60B、AS41B | マグネシウム(Mg)、アルミニウム(Al)、亜鉛(Zn) | 632 - 650 | 極めて軽量で、重量に敏感な用途に適した優れたキャスタビリティー。 | 航空宇宙(車体構造、内装部品)、自動車(軽量部品)、エレクトロニクス(携帯機器、携帯電話筐体) |
亜鉛合金 | 亜鉛合金 #2、#3、#5、#7、ZA8、ZA27 | 亜鉛(Zn)、アルミニウム(Al)、銅(Cu)、マグネシウム(Mg) | 381 - 419 | 鋳造性に優れ、融点が低く、複雑な設計に適しており、コスト効率が高い。 | エレクトロニクス(コネクター、ハウジング)、金物(錠、ボタン)、玩具、自動車部品(装飾部品、ギア) |
銅合金 | 黄銅(C85700など)、青銅(C93200など) | 銅(Cu)、亜鉛(Zn)(黄銅);銅(Cu)、錫(Sn)(青銅) | 900 - 1083 | 高強度、優れた導電性と耐食性、耐久性。 | パイプ(耐食水道管、ガス管)、電気コネクタ(端子、電気接点)、船舶用部品(耐食部品)、ベアリング |
錫合金 | - | 錫(Sn)(90%)、銅(Cu)(2.5%)、鉛(Pb)(7.5%)、アンチモン(Sb) | 170 - 230 | 低融点、良好な流動性、耐食性、容易な鋳造。 | 装飾品(宝飾品、手工芸品)、置物、土産物 |
鉛合金 | - | 鉛(Pb)、錫(Sn) | 183 - 327 | 低融点で柔らかく、耐食性に優れ、放射線遮蔽に適している。 | 放射線遮蔽(医療機器、原子力施設)、バッテリー(順次交換中) |
錫基合金 | - | 錫(Sn)、銅(Cu)、アンチモン(Sb) | 232 | 低融点、良好な鋳造特性、良好な耐食性。 | 電子部品(はんだ材料、電子部品)、宝飾品、特殊用途(小型部品、高級宝飾品) |
ダイカストと他の製造工程との比較
ダイカストは、他の製造工程(射出成形、鍛造、スタンピングなど)と混同されがちです。その類似性にもかかわらず、各工程には独自の利点と応用分野があります。以下では、ダイカストと射出成形や鍛造などの一般的な工程を比較し、その違いと適用シナリオについて説明します:
ダイカストと射出成形の違い
ダイカストと射出成形は、よく使われる2つの成形プロセスで、どちらも射出原理を使用し、複雑なディテールと優れた表面仕上げを持つ部品の製造に適しています。しかし、適用できる材料や工程は異なります。両者の主な違いは以下の通りです:
不一致 | ダイカスト | 射出成形 |
---|---|---|
ワークフロー | あらかじめ設計された鋼鉄製の金型に溶融金属を加圧射出する。 | あらかじめ設計されたスチール製またはアルミ製の金型に、圧力をかけて溶融プラスチックを射出する。 |
メイク | 非鉄金属合金(アルミニウム、亜鉛、マグネシウムなど) | 熱可塑性プラスチックまたは熱硬化性プラスチック |
金型材料 | 鋼鉄 | スチールまたはアルミニウム |
クールダウン | クールダウン時間が長い | より短いクールダウン時間 |
生産速度 | 比較的遅い | 割とすぐ |
加工費 | 金型コストの上昇(スチール金型を使用) | 金型コストの低減(アルミ金型を使用) |
部品コスト | 高い(生産時間が長いため) | より低い(より速い生産時間) |
ダイカストと鍛造の違い
鍛造とダイカストの主な違いは、成形方法である。鍛造では、圧縮力を加えることで金属を固体の状態に成形するのに対し、ダイカストでは、あらかじめ設計された金型に溶融金属を注入します。また、この2つのプロセスは、適用できる材料、生産速度、部品の性能の点でも異なります:
不一致 | 鍛金 | ダイカスト |
---|---|---|
ワークフロー | 加熱した金属に圧縮力を加えて成形する。 | 溶融金属を加圧下で金型に射出する。 |
メイク | 鉄やアルミニウムなどの鉄および非鉄金属用 | アルミニウム、亜鉛、マグネシウムなどの非鉄金属用 |
成形材料 | 金型は不要だが、形状を最適化するために金型を使用する。 | 金型を使用しなければならない |
生産速度 | 低調 | 割とすぐ |
トレランスコントロール | ミディアム・トレランス | 高精度公差制御 |
最終部品の特性 | 機械的特性の向上 | 機械的特性は鋳造材料に依存する |
ダイカストとスタンピングの違い
スタンピングはプレスによって金属板を成形するプロセスで、薄肉部品の大量生産に適しています。ダイカストと比較すると、スタンピングは成形材料と工程が異なり、特に適用部品の複雑さと生産性の点で異なります:
不一致 | ダイカスト | パンチ |
---|---|---|
ワークフロー | 成形用金型への溶融金属の注入 | 金型を使って金属板をプレスして部品を成形すること。 |
メイク | 主に非鉄金属合金(アルミニウム、亜鉛など) | あらゆる種類の金属板(スチール、アルミニウムなど)に適しています。 |
金型材料 | 鋼鉄 | 鋼鉄 |
部品形状 | 複雑な形状の部品 | 薄肉部品や単純な形状の場合 |
生産速度 | 低調 | 割とすぐ |
正確 | 高精度 | より低い精度 |
ダイカストと3Dプリンティングの違い
3Dプリンティングは、積層造形ベースのプロセスであり、材料を1層ずつ積み重ねてパーツを作成する。3Dプリンティングは、ダイカストよりも柔軟性が高く、より迅速なプロトタイピングが可能ですが、生産速度と部品の性能には違いがあります:
不一致 | ダイカスト | 3Dプリンティング |
---|---|---|
ワークフロー | 成形用金型への溶融金属の注入 | デジタルモデルに基づく材料のレイヤー・バイ・レイヤー印刷 |
メイク | 非鉄金属合金(アルミニウム、亜鉛など) | 熱可塑性プラスチック、金属粉末など |
金型材料 | 鋼鉄 | 金型不要 |
生産速度 | 低調 | 割とすぐ |
正確 | 高精度 | 中程度の精度 |
アプライアンス | 複雑な部品の大量生産 | ラピッドプロトタイピング、少量生産 |
一般的なダイカスト材料とその選択
アルミニウム、亜鉛、マグネシウム、その他の合金は一般的なダイカスト材料ですが、それぞれ異なる用途に適したユニークな特性を持っています。以下は、いくつかの一般的な合金の特性です:
- アルミニウム軽量で耐食性に優れ、加工しやすく、自動車、航空宇宙、エレクトロニクス分野で広く使用されている。
- マグネシウム合金航空宇宙や家電製品など、重量が重要視される用途向け。
- 亜鉛合金融点が低く、鋳造性に優れ、電子製品、金物、玩具部品によく使用される。
- 銅合金電気コネクターや船舶用部品の高強度、高導電性。
設計と製造の最適化
ダイカスト鋳造の設計は、材料の選択だけでなく、部品の形状、抜き勾配、フィレット半径などの要素も考慮し、部品の性能、製造性、費用対効果を向上させる必要があります。例えば、適切な抜き勾配は、部品が金型に固着するのを効果的に防止し、破損のリスクを低減することができます。適度なフィレット半径は、応力を均等に分散し、応力集中を避けるのに役立ちます。
評決を下す
ダイカストは、その高精度と大量生産能力により、現代の製造業に欠かせない技術となっています。自動車部品、電子機器筐体、航空宇宙部品など、ダイカスト技術は技術革新と卓越した設計のための強固な基盤を提供します。材料とプロセスが進歩し続けるにつれて、ダイカストは今後もさまざまな業界に、より効率的で高品質なソリューションをもたらし続けるでしょう。
ダイカストでよくある問題と対処法
なぜダイカストには気孔が生じやすいのですか?
ポケットは通常、射出工程で金属が完全にガス抜きされないか、金型設計の欠陥(例:貧弱なガス抜きシステム)によって発生します。対策としては、金型ベント設計の最適化、射出速度と圧力の調整、より効率的なベントシステムの使用などがあります。
ダイカストの表面に欠陥が生じやすいのはなぜですか?
気泡、しわ、傷などの表面欠陥は、金型表面の凹凸やメタルフローの不均一が主な原因です。このような問題を避けるためには、金型の表面仕上げを定期的にチェックし、射出温度と流量が安定していることを確認する必要があります。
ダイカストの引け巣の問題は何ですか?
収縮穴は鋳造冷却金属の収縮が原因で、フィラーを補充することができず、しばしばダイカストの大きいまたは複雑な形状に現れます。鋳型の設計を最適化し、注湯システムの効率を高め、冷却速度を調整することで、収縮を効果的に回避することができます。
ダイカストは割れやすい?
割れは通常、金属が不均一に流れたり、急速に冷えすぎたりした場合に発生し、過剰な射出圧力や金型設計の不備が原因となることもある。射出速度、温度、圧力を制御し、高強度材料を使用することで、割れを減らすことができる。
ダイカストの寸法不安定性についてはどうですか?
寸法の不安定は、金型の摩耗、射出圧力の不安定、不適切な温度制御が原因かもしれない。安定した射出条件を維持するために、金型の定期的なオーバーホールとメンテナンス、および温度制御システムの微調整を行うことで、寸法不安定の問題を効果的に解決することができます。
金型の摩耗はダイカストの品質にどのような影響を与えますか?
金型の摩耗や損傷は、製品精度の低下につながり、鋳造品の外観や性能にまで影響を及ぼす可能性がある。鋳型の摩耗に対抗するには、鋳型を定期的に検査・交換し、耐摩耗性材料を使用し、鋳型の設計と工程を最適化する必要があります。
なぜダイカストは変形しやすいのか?
変形は通常、不均一な冷却や金型設計の不備によるもので、特に鋳物が大型であったり複雑であったりする場合に起こります。歪みのリスクは、冷却システムを調整し、金型設計を最適化することで低減できます。
どうすれば冷温分離を減らすことができるのか?
冷間偏析とは、鋳型に注入された金属が完全に融合しないために形成される層間剥離の欠陥である。冷偏析を防ぐには、スムーズなメタルフローを確保するために射出速度と温度を最適化し、注湯システムとランナーを適切に設計する必要がある。
ダイカストの後処理は必要ですか?
ダイカストの後処理要件は、部品の設計要件と表面品質基準によって異なります。部品によっては、厳しい公差と表面仕上げを満たすために、研削、穴あけ、バリ取りなどの追加加工が必要になります。