CNC旋盤開発の歴史:基本旋盤加工から複雑部品製造の技術革命へ
发布时间2025-02-24 分类広報 浏览量2228
工業文明の生きた化石として、CNC旋盤の進化は、精密製造の永遠の追求を描き出す。紀元前1300年のエジプトの職人がロープで駆動する木製の回転ベッドを持つことから、21世紀のAIアルゴリズムを搭載した5軸インテリジェント工作機械まで、技術は常に蒸気動力旋盤の産業革命期の境界の "精度 "の再定義にある0.1ミリメートルの加工誤差に圧縮されますが、現代のCNCシステムは、スケールのクローズドループ制御を介して0.0000ミリメートルを達成している。産業革命時代、蒸気動力旋盤は加工誤差を0.1mmに圧縮したが、現代のCNCシステムは閉ループスケール制御を通じて0.001mmの微細制御を実現した。特に高性能のアルミニウム部品製造の分野では、CNC旋盤の多軸相乗機能は従来の工程を完全に変えた。新エネルギー車のモーターシェルを例に取ると、その放熱歯片とベアリングビットの複合加工は、Y軸パワータレットと統合されたCNCシステムで一度に完了することができ、従来の逐次加工に比べて400%効率を向上させ、同軸度誤差を5μm以内に制御することができ、この技術的飛躍は生産工程を再構成するだけでなく、軽量化設計の工学的限界も促進する。この技術的飛躍は、生産工程を再構築するだけでなく、軽量設計の工学的限界を押し上げる。
CNC工作機械の発展
CNC工作機械は、デジタルコード(プログラム命令)の形の情報を使って工具を制御し、与えられた作業プログラム、移動速度、軌道に従って自動加工を行う工作機械で、CNC工作機械と呼ばれる。
時間間隔 | 開発イベント | 技術的特徴 |
1952 | パーソンズとマサチューセッツ工科大学(MIT)は共同で、パルス増倍原理を利用した世界初の3座標リンク式立型CNCフライス盤を製作した。 | 電子管制御によるCNC技術の初期探究 |
1954 | ベンディックスUSAは、世界初の産業用CNC工作機械を製造した。 | CNC工作機械の産業応用の始まりは、CNC技術の初期の成熟を意味する。 |
1959 | CNCシステムは、トランジスタ化された制御装置によって第2世代へと進化した。 | 真空管に比べて高い信頼性と安定性 |
1965 | CNCシステムは、小規模な集積回路制御を使用する第3世代へと進化した。 | 集積回路の使用は、CNCシステムの性能と信頼性を向上させます。 |
1970 | 第4世代のCNCが登場し、ミニコンがCNCに使われ始めた。 | コンピュータ技術の応用により、CNCシステムはより高度なインテリジェンスと自動化を実現している。 |
1974 | 第5世代のCNCが登場し、マイクロプロセッサーがCNCに使われ始めた。 | マイクロプロセッサの応用により、CNCはより柔軟で効率的になる |
1970年代後半~1980年代前半 | 米国、ドイツ、日本およびその他の国は、CNC工作機械の分野で大きな進歩を遂げ、一連の高性能CNC工作機械を発売した。 | CNC工作機械技術は徐々に成熟し、応用分野は拡大している。 |
1980s | 日本のCNC工作機械の生産台数は米国を上回り、世界一となっている。 | CNC工作機械分野における日本の技術革新と品質管理は、世界市場をリードしている。 |
1990年代から現在まで | CNC工作機械技術は発展を続けており、各国は高性能、高精度のCNC工作機械を導入している。 | CNC工作機械は、制御、精度、自動化、柔軟性の面で常に向上しており、航空宇宙、自動車、電子機器、その他のハイエンド製造分野で広く使用されています。 |
2020s | 中国のCNC工作機械産業は急速な発展を遂げ、著しい技術躍進を遂げ、外国の技術独占を打ち破っている。 | 中国はハイエンドCNC工作機械の分野で大きな進歩を遂げ、国産CNC工作機械の市場競争力は向上し続けている。 |
初期の手動旋盤
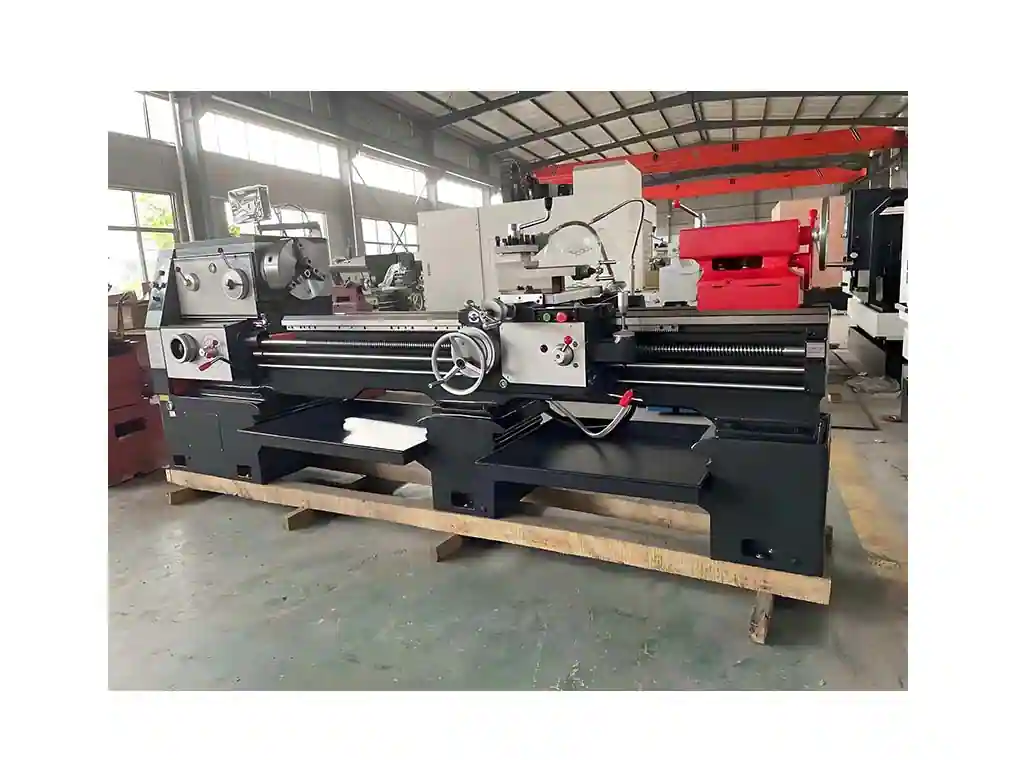
旋盤加工の真髄は、回転するワークと直線的な工具の繊細でダイナミックな相乗効果にある。この製造技術の起源は、紀元前1300年の古代エジプト文明まで遡ることができます。職人たちは、動物の腱で作ったロープを木材に巻きつけ、前後に引っ張ることで回転切削を実現し、円形部品を加工する最も初期の方法を開拓しました。
旋盤技術の最初の質的変化は、金属加工産業の爆発的な需要がもたらした産業革命の時代にもたらされた。蒸気動力の導入、ベルト駆動システムによる人力の代替、鋳鉄ベッドの耐振動設計により、旋盤は初めて標準部品を大量生産する能力を獲得した。この時期に誕生したオールギアトランスミッションシステムは、加工精度をミリメートルレベルまで押し上げ、近代機械工学の礎石を築いた。
今日、CNC技術の浸透は旋盤のDNAを完全に再構築した。オペレーターは、手作業の労働者からプログラムの設計者へと変貌し、工作機械は複雑なロジックを自律的に実行できるインテリジェントな端末へと進化する。この変革は、複雑な曲面の加工サイクルを60%短縮するだけでなく、ミクロン単位の寸法精度を安定させ、製造業がデジタル精密時代に正式に参入したことを示す。
手動旋盤の基本設計と機能
機械加工の礎である手動旋盤のモジュラーデザインは、今日でも現代の工作機械にインスピレーションを与え続けています。鋳鉄製のベッドから精密なドライブトレインに至るまで、各コンポーネントの相乗効果は、機械工学の独創的な知恵を示し、CNC技術の進化の基礎となる論理を提供しています。
ソファー
手動旋盤の鋳鉄ベッドは箱構造設計を採用し、内部の格子状補強はねじり剛性を大幅に向上させ、その振動減衰性能は80%以上の切削振動を吸収することができます。V型ガイドウェイと平面ガイドウェイとベッド表面の精密研削の組み合わせは、ドラッグプレートの移動の直線精度を0.02mm/m以内に制御することを保証します。この剛性の基礎は、旋盤が高硬度合金を加工する際の安定性を維持することを可能にし、時効処理された鋳鉄材料は効果的に温度上昇の変形を抑制し、長期加工の幾何学的精度を保証します。
スピンドルボックス
スピンドルボックスは、6速ギヤトランスミッションシステムを内蔵したパワーセンターとして機能し、スライドギヤセットにより45~2000rpmの幅広い速度調整を実現します。3爪セルフセンタリングチャックと弾性コレットのモジュラー設計により、Φ5~300mmのワークのクランプソリューションを素早く切り替えることができ、モールステーパースピンドルインターフェースと相まって、ワークのラジアル振れは0.03mm以下に抑えられています。 可変速ハンドルとクラッチのリンク設計により、オペレータは切削プロセス中に回転速度をシームレスに切り替えることができ、アルミ合金の仕上げ旋削からステンレス鋼の荒加工まで、様々なシーンのニーズに適応します。
バギー
複合ドラッグプレートシステムは、縦/横送り機能、縦スクリューガイド6mm/回転、ダイヤルにより0.02mmの微調整精度を実現。4ステーションタレットツールホルダーは、迅速なツール交換をサポートし、15秒以内に旋削、溝入れ、ねじ切りなどのマルチプロセスの切り替えを完了します。ハンギングホイールボックスのギア比により、0.5~10mmの標準ピッチを60個生成でき、ドライブシャフト、ネジなどの精密ネジ加工の需要に応え、繰り返し位置決め精度は±0.01mmに達する。
制御と相乗システム
左手で縦方向の送り(0.05~0.3mm/r)、右手で横方向の切り込み(精度±0.01mm)を制御し、フットペダルでクラッチを操作してスピンドルを始動・停止します。ツールキャリアの遊星ギアトレインがスピンドルの動きを正確な送り比に分解し、ハーフナット機構がねじ切り時の送り速度を自動的に同期させるというメカニカルロジックが、複雑な加工工程を直感的なマニュアル操作に変えます。
ツールホルダーと潤滑
調整可能な四辺形ツールホルダーは、工具の高さ±2mmの微調整をサポートし、ウェッジロック機構により切削工程の剛性を確保します。スプラッシュ潤滑システムは、ギヤへの連続給油と重要な摩擦部品への8箇所の手動給油を行い、複合潤滑プログラムにより8時間の連続運転でも安定した摩擦係数を維持します。ツールホルダの角度調整機構は、-5°から45°までの傾斜角度の設定をサポートし、テーパー、球体、その他の形状の輪郭の加工要件を満たします。
手動旋盤操作の限界を詳しく説明
リミテッドオートメーション
自動車用トランスミッションのギアを加工する場合、オペレーターは送り速度、切り込み深さ、主軸回転数を同期させる必要があり、1個の加工に最大50分かかるのに対し、CNC加工機ではわずか12分しかかからない。このように手作業への依存度が高いため、大量生産では35%の効率損失が発生し、初心者オペレーターのスクラップ率は熟練労働者の5倍も高かった。
精度の複雑さ
ディーゼルエンジンのインジェクターノズルハウジングを加工する場合、オペレーターの経験の差によって、クリティカルボアサイズが0.05~0.12mm変動することがあります。4時間の連続加工後のベッドの熱変形によって、テールストックが0.03mm移動し、工具の摩耗によって、20個ごとに0.1mmの誤差が蓄積されます。
時間のかかる設定
1,000ピースのベアリングハウジング加工のバッチは、従来の旋盤の切り替えは、テールストックの位置を調整する必要があることを示している(時間のかかる25分)、治具の再ロード(15分)、テスト切削キャリブレーション(30分)、準備時間は28%の総工数を占めた。 対照的に、CNC装置は、切り替えに8分でパラメータの全範囲を完了するプログラムを通じて呼び出すことができ、大量生産の手動モードの効率ボトルネックを強調している。
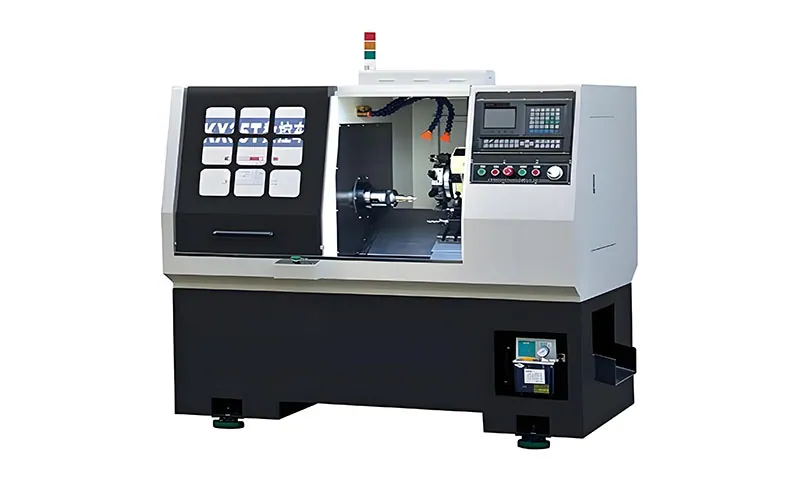
最新CNC旋盤
インテリジェント生産システムの核心設備として、現代CNC旋盤は、デジタル技術と機械工学の深い統合を通じて、精密製造の境界を再定義している。その技術進化は、ハードウェアのアップグレードだけでなく、インテリジェント制御システムの画期的な開発にも反映されています。
制御システム
最新のCNC旋盤はデジタル制御システムを搭載し、高速データバスを通じて、リアルタイムで主軸、送り軸、補助装置の協調動作を調整し、装置の中枢神経系として機能する。内蔵された誤差補正モジュールは、スケールのクローズドループフィードバック機構により、少量の偏差によってもたらされる機械的な伝達ギャップと熱変形を自動的に補正することができ、位置決め精度はミクロンレベルのカテゴリーで安定します。このデジタル制御ロジックは、手作業の経験に頼る従来の機械加工の操作モードを完全に変え、複雑な表面の輪郭精度を髪の毛の直径の1/10のレベルにまで到達させることを可能にします。
ユーザーフレンドリーなプログラミング・インターフェース
インテリジェントなヒューマン・マシン・インターフェースは、工具経路と材料除去プロセスを視覚化する3Dシミュレーションモジュールにより、加工プログラムの作成に革命をもたらします。オペレーターはドラッグ&ドロップのプログラミング機能により、素早くGコードを作成することができ、システムは自動的に切削パラメータの組み合わせを最適化し、さらに図面の特性を認識して加工ストラテジーを推奨します。タッチスクリーンと音声コマンドの融合設計は、60%による装置のデバッグ効率を向上させ、プログラミングの専門知識に頼る敷居を大幅に下げます。
適応制御アルゴリズム
この機械のインテリジェントコアは、切削力、振動スペクトル、温度変化のリアルタイムデータを収集するマルチセンサーネットワークを通じて、送り速度と主軸負荷を動的に調整する。航空宇宙用のチタンコンポーネントを加工する場合、アルゴリズムは材料のハードスポットを特定し、工具のチッピングを回避するために切込み深さを自動的に減らします。この自己最適化機能により、機械は連続加工中も最高の効率を維持し、工具寿命を30%以上延ばし、安定した面粗さRa0.8μm以下を保証します。
より高度な処理能力
5軸リンクテクノロジーは、従来の工作機械の運動寸法の限界を打ち破り、B軸振り子ヘッドとC軸ロータリーテーブルの相乗効果により、タービンブレードのような複雑なパーツの完全加工を実現します。ミーリングスピンドル一体型のパワータレットは、旋削加工中にクロスホールとエンドフィーチャーの同時加工を可能にし、二次クランプエラーを排除します。複合加工機能により、従来は3台の機械で加工していた工程を1台の機械に集中させることができ、生産サイクルタイムを40%短縮することができます。
統合オートメーション技術
モジュール式自動工具交換システムは、40ステーションの工具マガジンを装備しており、工具交換を0.8秒で完了し、RFIDチップを通して工具パラメータを自動的にチェックすることができます。インテリジェント冷却システムは、加工材料の特性に応じて切削液の噴霧角度と流量を調整し、微量潤滑技術を採用することで、アルミニウム合金の加工時に85%のクーラント消費量を削減します。内蔵のワーク検査プローブは、加工ギャップ中に主要寸法を自動的に測定し、リアルタイムフィードバックデータを制御システムにフィードバックして補正補正を行うことで、品質の完全なクローズドループ管理を形成します。
手動旋盤とCNC旋盤のコアの比較
比較次元 | ハンドメイド旋盤 | CNC旋盤 |
---|---|---|
加工精度 | ±0.05~0.1mm(作業者の技量による) | ±0.005~0.01mm (スケール閉ループ制御) |
生産効率 | 1個あたりの消費時間が長い(段付きシャフトの加工に30分など) | 高速バッチ生産(同じ部品を5分で加工) |
操作の複雑さ | 熟練技術者が必要(3年以上の経験) | プログラムによる自動運転(基本操作のトレーニングを1週間受けて業務開始) |
初期費用 | 30,000~100,000円(エントリーレベル装備) | 20万円~200万円(5軸モデル) |
柔軟な生産能力 | 単品/小ロットに最適(切替調整に1~2時間かかる) | 大量・複雑なピースにも対応(交換作業はわずか5分) |
典型的なアプリケーション | 金型メンテナンス、実習指導、手工芸品製作 | 航空宇宙部品、自動車部品、医療機器 |
エネルギー消費率 | 平均消費電力3~5kW・h(スタンバイロスなし) | 平均消費電力 10~30kW-h (冷却/工具交換システムを含む) |
維持費 | 年間メンテナンス費用 ¥0.5~10,000(機械部品の交換が容易) | 年間保守料 ¥30,000~100,000(保守には専門技術者が必要) |
メリットとデメリットを徹底分析
手動旋盤の利点
- 低コストでフレキシブルな生産
- スタートアップに最適:CNC装置の購入費用の1/10
- 変更への迅速な対応:ツールパスの調整にプログラミングが不要(例:ブロンズ形状の部品加工)
- 技術遺産の価値
- 機械的な直感を養う:オペレーターは切削力と材料特性を視覚化することができます。
- 寧波市の専門学校の統計:手旋盤実習で工具選択の精度が向上 40%
CNC旋盤の利点
- 複雑な部品の加工能力
- 5軸リンク:タービンブレード加工可能(面精度±0.005mm)
- ミルターン:穴あけ/タッピングの同時加工(例:自動車ステアリング・ナックルの加工における3工程の節約)。
- 生産一貫性保証
- 2000個のバッチ処理で寸法変動<0.01mm。
- 医療機器工場からのデータ:数値制御加工骨釘糸通過率99.7%、手技のみ82%
推薦セレクション
要件シナリオ | 推奨機材 | ラショナル |
---|---|---|
ティーチング/プロトタイピング(限られた予算) | ハンドメイド旋盤 | 低コストの試行錯誤で基礎力をつける |
多品種小ロット(100個未満) | 経済的なCNC旋盤 | プロセスの再利用による単位当たりのコスト削減 |
大量の精密部品(1000個以上) | ハイエンドCNC旋盤 | 生産自動化+品質トレーサビリティシステム、40%の総合コストダウン |
超複雑部品(航空宇宙部品など) | 5軸ターニング/ミーリングセンター | 1回のクランプで複数のサーフェスを加工することで、基準誤差を回避。 |
CNC旋盤の多様な応用シーン
現代製造業の核心設備として、CNC旋盤はその高精度と高い柔軟性により、工業生産の様々な主要分野に浸透している。ミクロンレベルの精密部品から大型で複雑な部品の加工に至るまで、その技術的優位性は世界の製造業を再構築している。
複雑な形状部品の製造
航空宇宙分野では、5軸リンクCNC旋盤は、葉根ほぞと溝、空気膜冷却穴加工のタービンブレード(図1のような)を一度に完了することができ、12工程の伝統的なプロセスが3工程に削減され、±0.005ミリメートルのブレード輪郭精度。航空エンジンの高圧加圧ディスク加工ケースのモデルでは、フライス加工と旋盤複合技術の使用は、生産サイクルが72時間から18時間に圧縮され、振れ誤差は5μm以内に抑えられている。
精密金型製造
浙江省寧波副省級市ダイカスト金型産業クラスターでは、CNC旋盤が主要な金型コアの精密加工を引き受けている。新エネルギー自動車用モーターシェルの金型加工では、ホットランナーシステムによる多角度深穴加工(深さ対直径比15:1)により、金型寿命が50万ダイサイクルに向上します。精密ネジ加工モジュールは、0.2mmのマイクロピッチを生成することができ、マイクロコネクタの成形要件を満たすことができます。
自動車部品の大量生産
- エンジンシステム真円度誤差0.003mm以下のクランクシャフトジャーナルの段階的旋削加工
- 伝送システム従来の研削加工に代わるギヤボックス用ブランクのハードターニング(HRC60)。
- 電化コンポーネント8000rpmで振幅<0.01mmのモーターローターの高速ダイナミックバランシング。
4.医療機器の製造
人工関節用チタン合金の旋削加工では、表面粗さRa0.2μmの微小潤滑技術を使用し、インプラントの要件を満たします。整形外科用スクリュー(M0.6×0.125)のマイクロスレッド加工では、C軸割り出しにより0.01°の位置決め精度を達成し、ねじ係合の信頼性を確保しています。
5.エネルギー機器加工
原子力発電所のメインポンプのインペラ用高温合金インコネル718の機械加工では、適応制御アルゴリズムにより切削パラメータを動的に調整することで、工具寿命が40%延びた。風力タービンのベアリングリングの間欠旋削では、振動抑制技術を採用し、加工効率を3倍に向上。
業界アプリケーションデータ比較
適用分野 | 代表的な部品 | 精度要件 | 効率向上の大きさ |
---|---|---|---|
航空宇宙 | タービンブレード | ±0.005mm | 300% |
自動車製造 | クランクシャフトジャーナル | 真円度 0.003mm | 150% |
医療機器 | 人工関節 | Ra0.2μm | 200% |
エネルギー設備 | 原子力インペラ | 輪郭0.01mm | 250% |
よくある質問と回答
CNC旋盤は、どのようにして基本的な加工から複雑な製造へと飛躍したのだろうか?
CNC旋盤は、3つの大きな技術革命を経て進化してきた:
- メカトロニクス期(1950-1970)::
- ピアシングテープを用いたプログラミングによる単純なシャフト部品の自動加工(精度±0.1mm)
- 典型的なケース:GMはトランスミッションのギア加工に初のCNC旋盤を使用し、効率を200%向上させた。
- デジタル制御段階(1980-2000)::
- マイクロプロセッサー技術を導入し、円弧補間と多軸リンケージをサポート(精度±0.02mm)
- 画期的な事例:ボーイング747エンジンのタービンディスクの5軸加工、生産リードタイムを30日から7日に短縮
- インテリジェント・マニュファクチャリング・フェーズ(2010年~現在)::
- 0.0001mmレベルの制御を実現するMazak iSMART FactoryのようなAIアルゴリズムとIoTテクノロジーの統合
- 寧波市のあるダイカスト金型企業は、デジタルツイン技術により、金型の試作回数を15回から3回に削減した。
CNC旋盤の効率と環境保護を両立させるには?
- 効率改善技術::
- 自動工具交換システム(工具交換時間0.8秒以下)により、60%のバッチ処理効率を向上
- 高速切削技術(主軸回転数30,000rpm)により、アルミ合金の加工サイクルタイムを40%短縮
- 持続可能なイノベーション::
- 切削油剤90%の使用量を削減する微量潤滑システム(MQL)により、年間15万円/台のコスト削減を実現。
- ブレーキエネルギーを電気エネルギーに変換して再利用するエネルギー回生モジュールにより、消費電力を25%削減
- ある新エネルギー自動車部品工場はCNCによって材料配置を最適化し、材料利用率が68%から92%に向上した。
最新のCNC旋盤は、単純な部品も複雑な部品も扱えるのか?
- 簡単な部品加工::
- マクロによる毎分60本の安定生産でボルトのバッチ生産に対応
- ステップ軸の加工誤差は±0.005mmに抑えられ、従来の旋盤の5倍の精度を実現している。
- 複雑な部品のブレークスルー::
- ワンクランプで200フィーチャーを持つ航空エンジンマガジンの5軸複合旋盤加工。
- Ra0.1μm(ミラー効果相当)の球面精度を持つ医療用人工股関節の加工
- 寧波のある企業は、0.2mmの薄肉アルミ合金シェルをCNC旋盤で加工しており、その変形は0.03mm未満である。