鋳造と機械加工:どう選ぶ?
发布时间2025-03-19 分类広報 浏览量1857
寧波禾欣鋳造技術チームのコアメンバーとして、高圧鋳造を担当しています、低圧鋳造,重力鋳造 私は20年以上アルミニウムとアルミニウム材料の分野で仕事をしており、何百もの工業規模のプロジェクトのプロセス開発を主導してきました。お客様から "鋳造と機械加工のどちらを選ぶべきか "という質問を受けると、私の答えはいつもこうです。"絶対的な有利不利はなく、その場面に最も適した技術の組み合わせがあるだけです"。 以下、三次元の技術原理、実務経験、業界動向から、両者の核心的な違いと選択の論理を徹底分析する。
キャスティングとは?
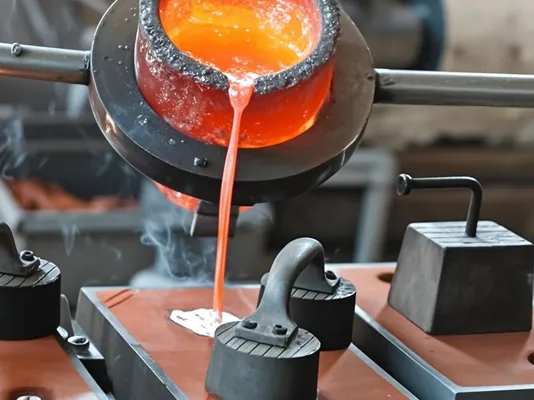
鋳造は金属を溶かし、鋳造を製造し、溶けた金属を鋳造に注ぎ、凝固させ、鋳造成形法の一定の形状と性能を得ることである。 鋳造および他の部品は生産の安価、プロセスの柔軟性、制限の複雑さの部分の構造のサイズそして形のほとんど独立した等と比較されるプロセスを、形作る。
人類文明の重要な原動力として、鋳造技術の歴史は紀元前4000年の古代ヨーロッパにまで遡ることができる。ブルガリアのヴァルナ遺跡で発掘された金の鋳物は、金属鋳造の初期の始まりを明らかにした。同じ時代、メソポタミアの職人たちはすでに銅合金を用いて道具を鋳造しており、中国の夏王朝と殷王朝の青銅器祭祀では、東洋の鋳造の知恵を示す分割鋳造法が用いられていた。エジプトのロストワックス法は精巧な彫像を形成し、中国宋の天公魁武は粘土鋳造を体系的に記録し、イスラム世界は精密機器の製造に鋳造を組み込んだ。
18世紀の産業革命は鋳造の歴史の転換点となり、コークス製鉄法と蒸気を動力とするダイカストマシンの組み合わせにより、鋳鉄部品は大規模な生産を実現し、鉄道、繊維機械、その他の産業システムの構築をサポートするようになりました。現代の鋳造は、よりハイテク分野に向かい、20世紀のアルミニウムとマグネシウム合金のダイカストは、航空産業を後押しし、3D印刷砂技術は、伝統的なプロセスの制限を打破する。現在、世界の鋳造年間生産量は1億トンを超え、自動車、エネルギー、医療などの主要分野をカバーしています。鋳物発祥の地の一つである中国は、現在、世界生産高40%で業界のリーダーであり、グリーンインテリジェント鋳造技術を通じて、技術革新をリードし続けています。この8,000年の歴史を持つ技術は、デジタル化と持続可能性をコンセプトに、現代の製造業の基盤を再構築しています。
キャスティングはどのように行われるのですか?
鋳造とは、溶融金属を特定の鋳型の空洞に注入し、冷却凝固させて所定の形状を得る工業技術である。伝統的な砂型鋳造では珪砂とバインダーを使い、注湯システムで空洞を作るが、インベストメント鋳造ではセラミックシェルやワックス型を使う。次に、原料を高温の炉で液状になるまで溶かす。アルミニウム 金属は700℃以上、鋳鉄の場合は1400~1500℃に加熱する必要があり、合金元素を加えて特性を調整する。注湯段階では、気孔や低温偏析の欠陥を避けるため、金属の流量と温度を正確に制御する必要があり、最新の真空ダイカスト技術は、負圧環境を通して金型の完全性を向上させます。
凝固プロセスは鋳物の内部品質を決定し、エンジニアは冷却システムの設計を通じて結晶粒の成長方向を調整し、船舶用ディーゼルエンジンブロックのような大型鋳物は、収縮穴をなくすために逐次凝固技術を使用することがよくあります。脱型後、砂の洗浄、スプルー切断などの加工を行い、CNC工作機械で主要部品の精密加工を行い、航空宇宙部品ではX線による内部欠陥の検出も必要です。現代の鋳造は、デジタル技術革新と統合されており、3D印刷砂技術は、複雑な油チャネル直接成形することができ、シミュレーションソフトウェアは、事前に金属の流れの軌道を予測することができ、古い砂の再生システムを介してグリーンキャスティングは、95%の廃棄物の利用率を向上させるために、インテリジェントな製造業と持続可能な開発の統合の深さを強調している。
鋳造の利点
複雑な部品の場合中空構造、曲面、不規則な輪郭を持つ金属部品は、金型設計によって成形することができ、他のプロセスでは困難な複雑な形状を解決することができます。
幅広い材料適合性溶融温度を金型の耐熱性に適合させるだけで、リサイクル・スクラップや低純度の原料を含め、さまざまな金属や合金を処理することができます。
スケールメリット金型に一度だけ投資した後は、同じ鋳物を何度も何度も大量に生産することができ、バッチサイズが大きくなればなるほど、1個あたりのコストは大幅に低下します。
サイズへの適応性が高い砂型鋳造は大型部品の製造に対応し、ダイカストなどの技術は中小型精密部品の成形に適しています。
マルチマテリアル統合能力金属または非金属のインサートを金型内にあらかじめ配置することで、複合構造部品(強化ブッシュなど)を直接鋳造する。
キャスティングのデメリット
内部欠陥のリスクプロセス・パラメーターの変動や材料の問題は、気孔、収縮、冷偏析などの欠陥につながりやすく、厳密な品質管理が必要となる。
マンパワー依存度が高い従来の鋳造工程では、鋳型の準備、注湯、洗浄など複数の手作業が必要で、自動化の程度は低い。
環境負荷金属を溶解すると有害なガスや粉塵が発生し、廃砂や廃スラグを不適切に処理すると環境を汚染する恐れがあるため、環境保護設備を備える必要がある。
機械加工とは?
加工(機械加工)とは、物理的な切削加工によって金属、プラスチック、その他の材料を精密に成形するための中核技術であり、現代の製造業の重要な局面で広く使われている。このプロセスでは、旋盤、フライス盤、CNC工作機械などの機器とドリル、切削工具、研削砥石を使用し、ミリメートル、あるいはマイクロメートルレベルの精度で材料の許容誤差を取り除き、ブランクを設計要件を満たす部品に加工する。自動車製造では、エンジンブロックのクランクシャフトの穴は、同心度を確保するために複数の工程を経て旋盤加工と穴あけ加工を行う必要がある。航空宇宙分野では、チタン合金フレームの複雑な表面を±0.005mm以内の公差で切り出すために、5軸CNC工作機械に依存している。鋳造や3Dプリンティングに比べて、機械加工はより高い表面仕上げを達成することができ、精密研削は、硬化鋼や他の超硬材料を加工しながら、Ra0.1μmの鏡面効果を達成するためにベアリングの軌道面を作ることができます。しかし、従来の切削加工では30%の材料ロスが発生する。近年では、微量潤滑と高速切削によるグリーン加工技術が40%の効率を向上させ、インテリジェントCNCシステムは自動的に工具経路を最適化し、エネルギー消費とコストを削減することができる。医療機器用ミニチュア骨釘から風力タービン用スピンドルに至るまで、機械加工は「サブトラクティブ・マニュファクチャリング」の精密な特性を活かして、ハイエンド機器や精密機器の工業化された生産ニーズを支え続けている。
機械加工の利点
高精度多軸CNC技術によりミクロン単位の精密制御が可能で、タービンブレードや医療用インプラントなど、寸法要求の厳しい複雑な部品に特に適しています。
小ロットへの迅速な対応複雑な金型開発の必要がなく、設計ファイルから直接加工できるため、試作や小規模生産のサイクルタイムを大幅に短縮できます。
安定した再現性CNCプログラムと標準化されたツールパスにより、連続生産における一貫した部品寸法と表面品質を保証します。
自動化生産CNCシステムは全工程を自動化し、手作業を減らし、操作ミスを減らし、装置の連続運転の効率を向上させる。
幅広い素材適応性金属、エンジニアリング・プラスチック、セラミック、複合材料に対応し、材料特性に関するさまざまな業界の多様なニーズに応える。
機械加工のデメリット
限定的な内部構造処理深い穴や空洞のような複雑な内部形状は、何度も工具を交換したり、特注の工具を使用したりする必要があるため、加工が大幅に難しくなり、コストも高くなる。
設備によるサイズの制約機械移動量や主軸剛性の制限により、大型ワークや重量ワークの全精密加工は困難です。
低い資源利用率切削加工では大量の金属屑や粉塵が発生し、積層造形やニアネットシェイプ加工に比べて原材料の損失率が高い。
機械加工と鋳造:種類と技術
加工タイプ
ミル回転多刃工具は、多軸方向に沿って被加工物を切削し、平面、曲面および複雑な三次元構造の加工に適しており、金型キャビティ、成形部品の製造に広く使用されています。
ターンシャフト、ディスク、ブッシュなどの回転部品を、カッターのリニアフィードと連動したワークの回転により、高能率に成形します。
ボーリングスパイラルドリルビットは、回転しながら材料を貫通して丸穴を形成するもので、スルーホール、ブラインドホール、ステップホールの加工に対応し、部品組立用の位置決め穴のバッチ生産によく使用される。
ふだつき高速回転する砥石で工作物の表面を微細切削し、寸法精度と仕上がりを向上させる。
つまらないエンジンブロックや油圧バルブボディなどの精密な内部空洞加工に使用される。
切出す多段の歯形を持つブローチを使用することで、キー溝、スプライン、または成形されたボアをワンパスで形成し、高い効率と安定した表面品質で、ギアやカップリングの大量生産に適しています。
ワイヤー浸食ガルバニック腐食の原理による導電性材料の切断は、超硬金属の複雑な輪郭の加工を可能にし、特に精密な抜き型や航空宇宙エンジンのブレードの成形に適しています。
プレーニング工具直線往復運動切断面や溝、大型工作機械のガイドレール、ベースプレート平面加工に適しています、簡単な操作ですが、低効率。
イーディーエムパルス放電を利用して導電性材料を腐食させることで、微細な穴や複雑な空洞、超硬金型を加工することができ、従来の切削加工における硬度の限界を打ち破る。
各工程は、工具の特性、軌跡、材料の適応性に応じて組み合わせて適用され、粗加工から超仕上げ加工までの産業チェーン全体のニーズに対応します。
鋳造タイプ
砂型鋳造珪砂、粘土または樹脂バインダーを使用し、鋳鉄、鋳鋼、その他の高融点金属の多様な生産に適した空洞を形成するためにエンボス加工モデルを介して、1回限りまたは半永久的な鋳造を行い、一般的にエンジンブロック、バルブ、その他の構造部品の製造に使用されます。
ダイカスト溶融した金属を高速で高強度鋼の金型に押し込み、急冷して成形する。自動車部品や電子筐体など、表面仕上げの要求が高い製品に広く使用される、アルミニウム、亜鉛、マグネシウムなどの非鉄金属製の精密薄肉部品の量産を専門とする。
インベストメント鋳造蝋型は固体模型の代わりに使用され、多層耐火被覆で包んでセラミック殻を形成し、蝋型を溶かしてから金属液に注入し、タービンブレード、アートワークなどの複雑で微細な構造を再現することができ、特に航空・宇宙分野の高温合金部品の小ロットカスタマイズに適している。
遠心鋳造これは、シームレス管やハブなどの回転対称部品で、遠心力によって液体金属が回転金型の内壁に均一に付着するため、材料の緻密化と生産効率の両方を兼ね備えており、パイプやベアリングリングの生産に使用される。
低圧鋳造金属液は空気圧によって密閉された金型にスムーズに注入され、乱流や酸化を抑え、高い気密性が要求されるアルミホイールのハブやシリンダーヘッドのような中空部品を、工程の安定性と材料の利用率の両方の利点を生かして成形する。
バニシングモールド鋳造(TCM)発泡模型は伝統的な鋳型の代わりに使用され、模型はガス化され、注湯中に液体金属で満たされ、複雑な内部空洞を持つ鋳物を形成するために統合することができ、鉱山機械、ポンプ、バルブハウジングなどの単品または少量生産に適しています。
連続鋳造液体金属を連続的に凝固させ、水冷式晶析装置を通して引き抜くことで、棒材、板材、形材を直接製造することができます。これにより、鉄鋼、銅合金、その他の材料の成形効率が飛躍的に向上し、冶金産業における大規模生産の中核プロセスとなります。
各鋳造技術は、鋳型の特性、金属の流動性、生産ニーズに応じて適合・適用され、美術鋳物から工業部品まで、あらゆる製造能力を形成している。
機械加工と鋳造の主な違い
工具の特徴
機械加工では、フライスカッター、ドリル、旋盤などの切削工具を使って直接部品を成形するが、鋳造では、模型の製作、鋳型の準備、その他の前工程を通じて成形空間を構築する必要があり、ワックス鋳型の彫刻から砂の準備までの全工程をツールチェーンでカバーする。
精密制御
機械加工は、CNCシステムによってミクロン単位の精度を達成し、特に高い表面仕上げと複雑な形状の細部を得意とする。鋳造部品は、金型の精度や金属の収縮などの影響を受けるため、精密ダイカストやインベストメント鋳造プロセスの助けを借りて寸法の一貫性を向上させる必要がある。
素材の互換性
鋳造材料は融点と流動性によって制限され、砂型鋳造は鋳鉄、鋳鋼、その他の高融点金属に適しており、ダイカストはアルミニウム、亜鉛、その他の低融点合金に焦点を当てています。
デザインの複雑さ
機械加工は、シャープなエッジ、薄肉構造、精密な穴や溝を成形するのは得意だが、深い空洞、内部曲線、その他の閉じた構造の加工には盲点がある。鋳造は、内部空洞、曲線の流線、複雑な部品(エンジンブロックなど)を一体成形できるが、細部のシャープさは低い。
生産規模の適応
鋳造は大量生産においてコスト面で有利であり、金型は1回限りの投資ですぐにコピーすることができる。金型なしの機械加工は、プログラムによって少量または単一ピースのカスタム要件、強力な柔軟性のニーズに対応するように調整することができる。
パート・パフォーマンス
凝固欠陥のない機械加工部品は、機械的特性がより均一である。方向性凝固、熱処理、および粒構造を最適化する他のプロセスによる鋳造部品は、原材料の強度に近いことができますが、微細な孔や介在物があるかもしれません。
プロトタイピングの効率化
機械加工はCADモデルからの直接切削が基本で、プロトタイプは数時間以内に試作される。鋳造プロトタイプは、鋳型の開発と金属の注入によってリードタイムが長くなるが、インベストメント鋳造はワックスモデルを3Dプリントすることでプロセスをスピードアップできる。
統合されたコスト構造
鋳造の初期段階では金型のコストが高く、スケールアップして1個のコストを薄めるのに適している。機械加工は金型のコストがなく、材料のロスや工数のコストがバッチサイズに応じて直線的に上昇するため、中小規模や高付加価値製品に適している。
鋳造は複雑な部品の一括成形に対応し、機械加工は精密な形状の最終的な修正を可能にするもので、この2つの工程が一体となって、ブランクから完成品までの完全な製造チェーンを支えている。
鋳造と機械加工はどこで使われているのですか?
産業分類 | 鋳造の代表的な用途 | 機械加工の代表的な用途 |
---|---|---|
自動車製造 | エンジンブロック、ギアボックスハウジング、ホイールハブ、サスペンションマウント | トランスミッションギア、ピストンリング、クランクシャフトジャーナル、ブレーキキャリパー |
航空宇宙 | タービンケーシング、エンジンブレード、着陸装置構造部品 | チタンフレーム、燃料ノズル、フライトコントロール精密部品 |
医療機器 | 医療用ベッドフレームベース、画像診断機器ハウジング | 人工関節、手術器具、マイクロインプラント(骨釘など) |
エネルギーと電力 | 風力タービンハウジング、原子炉圧力容器 | タービンブレード、油圧スプール、トランスミッションコネクション |
産業機器 | バルブハウジング、ポンプボディ、重機ベース | 高精度ベアリング、ネジ、金型インサート、自動ロボットアーム |
電子通信 | 5G基地局ヒートシンク、アルミ合金シェル(ダイカスト) | RFコネクター、チップヒートシンク、マイクロセンサーハウジング |
メトロ | ブレーキディスクブランク、レールファスナー | ホイールセット加工、台車精密ブッシュ、信号システム部品 |
造船 | プロペラ鋳物、舶用ディーゼルエンジンシリンダーライナー | 推進シャフトシステム、サーボ精密ギア、油圧ライン継手 |
消費財 | 鋳鉄製調理器具、ドアロック本体、バスルーム金物 | スマート家電用ギア、精密ヒンジ、電子製品用メタルベゼル |
建物とインフラ | 市営マンホール蓋、鋼構造物接続ノード、橋梁ベアリング | 建築型枠ファスナー、リフトガイドレール、耐震ブレースアクセサリー |
プロセス適応ロジック::
- キャスティング特に重視するのは複雑な一体成形例えば、内部空洞のあるエンジンブロック、薄肉のダイキャスト製電子機器ハウジング、耐高圧バルブなどである;
- 加工共焦点精密機能部品例えば、高速ベアリングの軌道面、ミクロンサイズの医療用インプラント、航空燃料用の精密ランナーなど。
この2種類の工程はしばしば併用される。つまり、鋳造でニアネットシェイプのブランクを提供し、機械加工で重要な部分を仕上げることで、高性能の最終製品を実現するのである。
どちらを選ぶべきか?機械加工か鋳造か
製造プロジェクトに機械加工と鋳造のどちらを使用するかを決定する場合、設計の特徴、生産目標、およびリソースの条件に基づいて包括的な評価を行う必要があります。以下では、工程をお客様のニーズに正確に適合させるための、重要な判断基準について詳しく説明します。
1.生産規模と拡張性
- キャスティングを選択長期的かつ安定的な大量生産が必要なプロジェクト(自動車部品、家電製品の構造部品など)の場合、鋳造プロセスでは、生産量が増加するにつれて部品あたりのコストが大幅に削減されます。鋳型の再利用性は、大規模生産、特に標準化された製品の迅速な再生産において、当然の利点となります。
- 機械加工を選択小ロットのカスタマイズ要件(プロトタイピング、航空宇宙専用部品など)や、頻繁な設計の繰り返しが必要な製品では、機械加工により、高価な金型投入が不要になり、注文変更への迅速な対応が可能になり、小・中ロットの生産に柔軟に対応できる。
2.部品の構造の複雑さ
- キャスティングを選択部品に内部空洞、薄肉構造、多方向流路などの複雑な幾何学的形状が含まれる場合(例:エンジンブロック、油圧バルブボディ)、鋳造は金型キャビティを通過する1回のパスで形成できるため、複数の工程で機械加工する時間のかかる問題を回避できる。
- 機械加工を選択外部精密輪郭、微細穴アレイ、超微細表面(光学機器ベース、医療用インプラントなど)に重点を置いた設計の場合、切削加工精度は複雑な表面のミリメートルレベルの制御を可能にし、特にオープン構造の深彫りに適しています。
3.正確性と一貫性の要件
- キャスティングを選択鋳造部品の寸法精度は通常、鋳型の品質と工程管理に依存し、中精度のシナリオ(パイプコネクター、装飾部品など)に適しています。高精度の合わせ面については、「鋳造+部分仕上げ」のハイブリッドプロセスにより、コストを削減することができます。
- 機械加工を選択ミクロン単位の公差やタイトフィットが要求される部品(精密歯車、半導体デバイスのキャビティなど)でも、機械加工はデジタルプログラミングと高剛性設備により、一貫して安定性の高い完成品を提供することができる。
4.材料特性と適合性
- キャスティングを選択アルミニウム合金、亜鉛合金、鋳鉄など、流動性の良い金属の場合。リサイクルされた材料(例えば、リサイクルされたアルミニウムインゴット)の場合、鋳造工程は効率的にそれらを溶解し、再成型するため、資源の利用が大幅に増加します。
- 機械加工を選択高硬度合金(チタン合金、焼き入れ鋼)、非金属(エンジニアリング・プラスチック、セラミック)、複合材など、より幅広い種類の材料に対応。溶融成形が困難な材料や熱に弱い材料の加工に特に適しています。
5.材料の利用と持続可能性
- キャスティングを選択ニアネットシェイプ技術は、材料の無駄を最小限に抑え、特に貴金属や希少金属の加工に適しています。リサイクルアルミ鋳造の炭素強度は、グリーン製造のトレンドに沿い、新しいアルミ機械加工のわずか1/3です。
- 機械加工を選択切断工程で発生する切り屑は、原料の重量に占める割合が大きく、環境コスト削減のためには廃棄物のリサイクルシステムが必要である。
6.生産スピードとリードタイム
- キャスティングを選択金型の開発段階には時間がかかるが、量産開始時には非常に効率的であるため、リードタイムが長く、生産量が安定しているプロジェクトに適している。
- 機械加工を選択図面から完成品までのサイクルタイムが短いため、急ぎの注文や迅速なプロトタイプの反復に適しており、特にデジタル製造の俊敏性の恩恵を受けています。
7.コスト構造の比較
- キャスティングのコアコスト項目金型設計と製造コストが初期投資の大半を占めるため、生産量のコスト希薄化シナリオに適している。
- 機械加工のコアコスト項目設備の減価償却費、工具の摩耗、労働力のプログラムコストが支配的で、小ロット、高付加価値製品に適している。
8.ハイブリッド・プロセスにおける革新的実践
ほとんどの産業シナリオでは、単一のプロセスではすべてのニーズを満たせないことが多い。推奨される戦略::
- 鋳造+仕上げ鋳造による複雑な車体構造の実現と、それに続く重要な合わせ面のCNC仕上げ(自動車用ギアボックスのハウジングなど);
- 積層造形+切削加工機械加工の許容誤差を減らすためのニアネットシェイプ・ブランクの3Dプリント(航空宇宙用ブラケットなど)。
要約:正確な意思決定のための動的トレードオフ
- 望ましいキャスティング・シナリオ大量生産、複雑な内部空洞構造、材料コスト重視、グリーン製造指向;
- 望ましい加工シナリオ小ロット、高精度、高硬度材加工、短納期;
- ハイブリッド・プロセスの黄金コンビ効率と精度のバランスをとり、コストと性能の最適解を達成する。
寧波禾欣の実務経験では、成功事例は上記の次元のダイナミックな評価から生まれることが多い。各プロジェクトのプロセス選択が科学的、経済的、持続可能であることを保証するために、企業は複数の部門が協力するプロセス検討メカニズムを確立し、必要に応じて第三者の技術コンサルティングを導入することをお勧めします。
一般的な問題
Q1: 生産需要に応じて、鋳造と機械加工のどちらを選べばよいですか?
鋳造は、複雑な構造部品(エンジンブロックなど)を大量に製造するのに適しており、空洞を成形することができるが、精度が限られている。機械加工は、高精度(精密歯車など)の少量のニーズを満たすために、さまざまな材料を扱うことができますが、削減の複雑さの効率。
Q2: 費用対効果が高いのはどのプロセスですか?
鋳造のプレ金型コストは高いが、1個あたりのコストは体積に応じて減少し、大規模生産(電子シェルの数百万個など)に適しています。金型投資を伴わない機械加工は、中小バッチのカスタマイズ(航空宇宙部品など)に適していますが、材料の損失は、3D印刷砂のような新興技術のコストを押し上げ、従来のコストの境界を破ることです。
Q3:材料の選択はプロセスの決定にどのような影響を与えますか?
鋳造は、金属の流動性(アルミダイカストなど)と融点(鋳鉄など)によって制限される。砂型鋳造一方、機械加工は超硬合金(チタン合金など)やエンジニアリングプラスチックを切削できるが、脆性材料(セラミックスなど)ではチッピングが発生しやすく、特殊な工具や工程が必要となる。
Q4:非常に複雑な部品はどのように扱うのですか?
溶融成形技術による鋳造は、複雑な内部空洞(タービンブレードなど)を形成するワンピース、5軸CNC切削精密表面(インペラなど)を機械加工するが、閉じた構造は、プロセスの組み合わせである必要があります:機能とコストのバランスを達成するために、鋳造ブランク+機械加工仕上げ(シリンダーボーリングなど)。
Q5:どちらのプロセスがより環境に優しいですか?
機械加工は、切削液の汚染や金属切屑のリサイクルに対処する必要があるが、グリーン技術(ドライ切削、マイクロ潤滑)によって環境への影響は徐々に軽減されている。
Q6: 2つのプロセスを組み合わせる必要があるのか?
鋳造はネットシェイプに近いブランクを提供し(例:ギヤ鋳造)、機械加工は高精度のフィーチャーを完成させる(例:歯面研削)。積層造形+CNC仕上げは、航空宇宙部品などの超複雑なニーズを満たすために、従来の限界を打ち破る。
Q7: プロトタイピングには、どちらが早いですか?
機械加工では、CADによるストレートカットの利点により、金属/プラスチックプロトタイプを数時間で提供し、3Dプリントされたワックスモデルと組み合わせた鋳造では、材料特性や構造強度の検証が必要な機能プロトタイプのサイクルタイムを数週間から数日に短縮します。
コア・ロジック鋳造は「成形効率」を重視し、機械加工は「精度と制御」を重視する。コスト、時間、性能の三次元を中心に選択する必要があり、ほとんどの場面は代替ではなく、補完する必要がある。