Grundlagen der maschinellen Bearbeitung
发布时间:2025-02-27 分类:Nachrichten 浏览量:2000
Bearbeitung
Als Kerntechnologie der modernen Fertigung, Bearbeitung, durch Drehbänke, Fräsmaschinen, Schleifmaschinen und andere professionelle Ausrüstung auf Metall, Kunststoff und andere Werkstücke für das Schneiden, Schleifen, Bohren und andere Prozesse, präzise Kontrolle der Geometrie der Teile, strukturelle Dimensionen und Oberflächengüte, um sicherzustellen, dass von der Automobil-Motor-Komponenten für die Luft-und Raumfahrt Präzisionsteile der gesamten Bereich der Herstellung braucht. Durch die tiefe Integration von CNC-Technologie und automatisierten Produktionslinien wurde der Bearbeitungsprozess von der traditionellen manuellen Bearbeitung auf eine intelligente Programmiersteuerung umgestellt, die die Effizienz der Bearbeitung verbessert und gleichzeitig die Produktionskosten wirksam kontrolliert. Das Qualitätskontrollsystem, das streng den internationalen Normen entspricht, gewährleistet die Prozessstabilität in der Massenproduktion durch die Echtzeitüberwachung des Werkzeugverschleißstatus und die Optimierung der Bearbeitungsparameter. Unter dem aktuellen Trend der Industrie 4.0 entwickelt sich die Bearbeitung in Richtung einer flexiblen Produktion und eines digitalen Managements und bietet zuverlässige Lösungen für die Anpassung komplexer Teile.
Bearbeitung mit numerischer Steuerung
Die CNC-Bearbeitung stützt sich auf die Computerprogrammierung, um die Bahn der Werkzeugmaschine genau zu steuern. Durch die automatisierte Ausführung von Dreh-, Fräs-, Bohr- und anderen Präzisionsbearbeitungsprozessen werden Metall, technische Kunststoffe und andere Rohmaterialien effizient in komplexe Komponenten umgewandelt, die den Konstruktionsspezifikationen entsprechen. Ihr Hauptvorteil liegt in der hohen Wiederholgenauigkeit und der Fähigkeit zur mehrachsigen Verkettung, die sich an die Anforderungen der Großserienfertigung von Mikrokomponenten für medizinische Geräte bis hin zu großen Strukturteilen für Energieanlagen anpassen lässt. Moderne intelligente Fabriken erreichen eine dynamische Optimierung der Bearbeitungsparameter und eine intelligente Vorhersage der Werkzeugstandzeit durch die Integration von CAM-Programmiersystemen und Online-Prüfgeräten, wodurch die Maßhaltigkeit in der Massenproduktion gewährleistet und die Bearbeitungseffizienz in High-End-Bereichen wie der Luft- und Raumfahrt und bei Automobilformen verbessert wird. Mit der tiefgreifenden Anwendung der IoT-Technologie und des digitalen Zwillingsmodells beschleunigt die CNC-Bearbeitung die Entwicklung der Cloud-basierten kollaborativen Fertigung und der adaptiven Prozessanpassung und bietet eine wichtige technische Unterstützung für die intelligente Fertigungsökologie.
Klassifizierung der Bearbeitung
Drehen
Das Werkstück wird durch die Drehspindel gedreht, kombiniert mit der radialen/axialen Vorschubbewegung des Werkzeugs. Sie ist spezialisiert auf die Innen- und Außenrundbearbeitung von rotierenden Teilen wie Wellen, Scheiben und Buchsen und demonstriert die Vorteile der hocheffizienten Zerspanung bei der Massenproduktion von Antriebswellen für Kraftfahrzeuge, Zylindern für Hydraulikzylinder usw. Sie ist in der Lage, Kohlenstoffstahl zu bearbeiten, Aluminium Die CNC-Drehmaschine ist in der Lage, Gewindedrehen und Präzisionsbearbeitung von exzentrischen Strukturen in einer breiten Palette von Werkstoffen von Hochtemperaturlegierungen bis hin zu hochwarmfesten Legierungen durchzuführen.
fräsen
Die Verwendung von vertikalen / horizontalen Fräsmaschine Multi-Welle Werkzeug Rotationsschneiden, in der Lage, komplexe Hohlräume, dreidimensionale Oberfläche bilden Verarbeitung, von der Form Einsätze der Trennfläche an den Roboter Gelenke der Gelenke sind typische Anwendungsszenarien, Fünf-Achsen-CNC-Fräsen Technologie, um durch die Grenzen der räumlichen Winkel, Impeller, Propeller und andere Formteile im Bereich der Verarbeitung ist unersetzlich.
Schleifen
Der Materialabtrag im Mikrometerbereich mit Hilfe von Schleifscheibenpartikeln ist das ultimative Verfahren zur Erzielung von Spiegelpräzision in gehärtetem Stahl, Keramik und anderen superharten Materialien. Lagerlaufringe in der Präzisionsspindelfertigung und die Oberflächenbehandlung von künstlichen Gelenken für medizinische Geräte sind auf diese Technologie angewiesen, und die Maßhaltigkeit im Submikrometerbereich wird durch ein Online-Messsystem und die Umgebungskontrolle in einer Werkstatt mit konstanter Temperatur gewährleistet.
Bohren, Reiben, Gewindeschneiden und andere Bearbeitungen
Die Tieflochbohrtechnologie deckt die gesamte Bandbreite von der einfachen Durchgangslochbearbeitung bis hin zur Präzisionsgewindeformung ab und erfüllt die Anforderungen von Tieflochbohrungen, Öl- und Gaspipelines und anderen speziellen L/D-Verhältnissen. Durch den Einsatz von Verbundwerkzeugen können Bohr-, Reib- und Gewindeschneidvorgänge in einer einzigen Aufspannung durchgeführt werden, was die Bearbeitungseffizienz von Motorblöcken, Hydraulikventilblöcken und anderen Mehrlochteilen erheblich verbessert. Auch häufig verwendet in Druckgussform Herstellung.
Ausrüstung für die Bearbeitung
Drehbänke
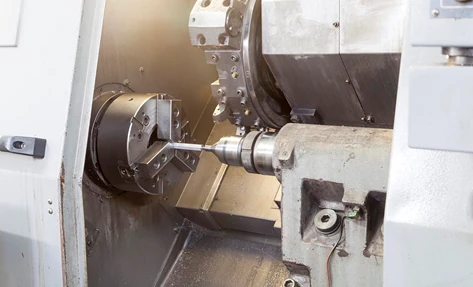
Als Kernstück der Rotationskörperbearbeitung treibt die Drehmaschine das Stangen- oder Scheibenwerkstück an, um es mit hoher Geschwindigkeit durch die Spindel zu drehen, und führt die zylindrische Dreh-, Planschneid- und Gewindebearbeitung durch Anpassung an die radiale/axiale Verbundvorschubbewegung des Revolvers genau aus. Die moderne CNC-Drehmaschine integriert die Funktion des angetriebenen Werkzeugs und der Y-Achse, die eine kombinierte Fräs- und Drehbearbeitung von rostfreiem Stahl, Titanlegierungen und anderen schwer zerspanbaren Materialien durchführen kann. Sie ist weit verbreitet in der Massenproduktion von Automobil-Nockenwellen, hydraulischen Ventileinsätzen und anderen Präzisionsteilen, und ihre Doppelspindelkonstruktion kann eine automatisierte kontinuierliche Bearbeitung erreichen.
Bearbeitungszentrum
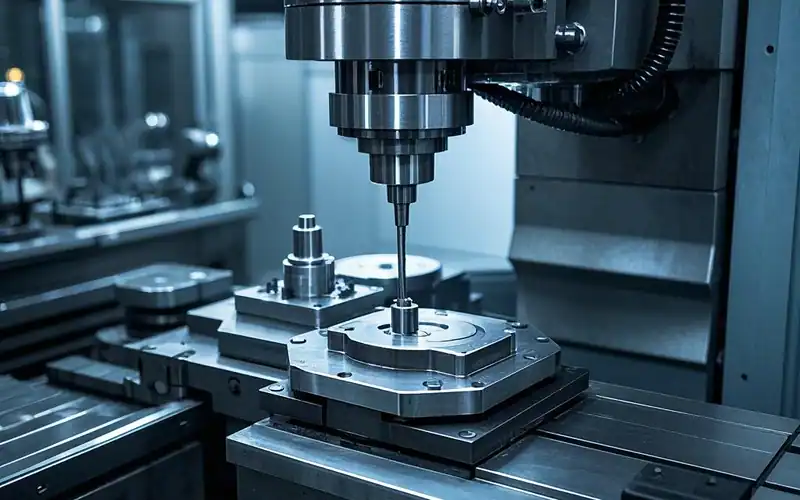
Die 5-Achsen-CNC-Fräsmaschine durchbricht die Begrenzung des Raumwinkels durch das Schwenken des Tisches, um die Unersetzlichkeit bei der dreidimensionalen Bearbeitung der gekrümmten Oberfläche der Schaufeln von Flugzeugtriebwerken und der Einsätze von Kunststoff-Spritzgussformen unter Beweis zu stellen. Das mit einem automatischen Werkzeugwechselsystem ausgestattete Bearbeitungszentrum kann den gesamten Prozess der Bearbeitung von Rahmenteilen aus Aluminiumlegierungen von der Grobbearbeitung bis zum Fertigfräsen in einem Arbeitsgang erledigen.
Bohrmaschine
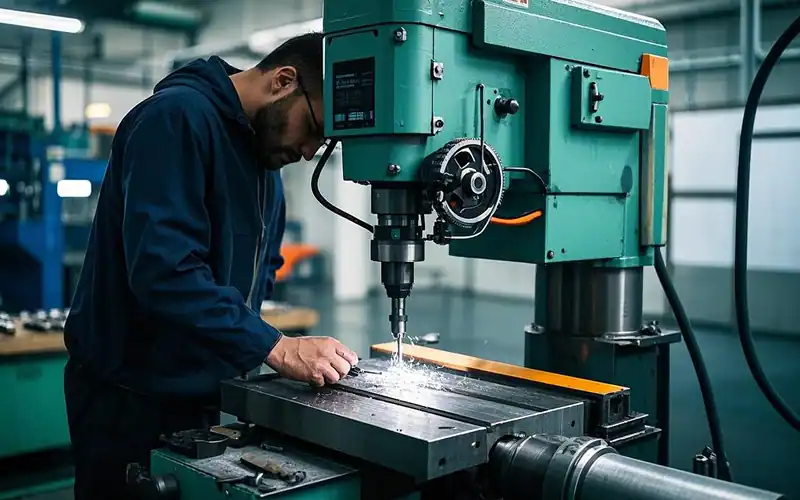
Als professioneller Lösungsanbieter im Bereich der Tieflochbearbeitung treibt die Bohrmaschine Spiralbohrer, Tieflochbohrer und andere Werkzeuge mit einer Hochgeschwindigkeitsspindel an, um eine präzise Lochbearbeitung zu erreichen, und die Pistolenbohrtechnologie mit einem Hochdruckkühlsystem kann Tieflochbohrungen mit einem Verhältnis von Länge zu Durchmesser von mehr als 30:1 durchführen. Das intelligente Bohrzentrum integriert Reib- und Bohrprozessmodule, um die Nachfrage nach einer effizienten Bearbeitung von Löchern mit mehreren Spezifikationen, wie z. B. Rohrplatten für Energieanlagen und Getriebeschalen für Kraftfahrzeuge, zu erfüllen, und ist mit einem Laser-Werkzeugeinstellgerät ausgestattet, um eine Echtzeitkompensation des Bohrerverschleißes zu erreichen.
Schleifer
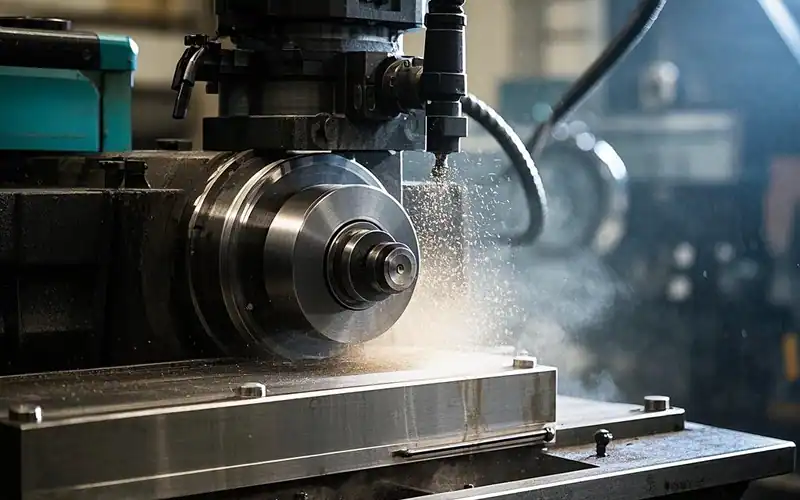
Als letzte Verteidigungslinie für die Qualität der Präzisionsfertigung verwendet die Schleifmaschine CBN-Schleifscheiben oder Diamantschleifscheiben, um superharte Materialien wie gehärteten Stahl und Hartmetall mit Nanopräzision zu bearbeiten, und die CNC-Profilschleifmaschine kann die Konturpräzision von Lagerlaufbahnen und Schraubengewinden durch ein geschlossenes Feedbacksystem stabil im Mikrometerbereich halten. Die spitzenlose Schleifmaschine, die mit einem Online-Messsystem ausgestattet ist, bietet vollautomatische Schleiflösungen für großvolumige, hochpräzise Teile wie Führungssäulen von optischen Instrumenten und Hydraulikventilspulen usw. Die Umgebungssteuerung der Werkstatt mit konstanter Temperatur gewährleistet die Bearbeitungsstabilität.
Sonstige Bearbeitungsmaschinen
CNC-Werkzeugmaschinen
Als Kernstück der intelligenten Fertigung verbindet sich die CNC-Werkzeugmaschine nahtlos mit dem CAM-Programmiersystem durch eine Mehrachsenverknüpfung, um die 3D-Modellierungsdaten komplexer Teile direkt in Präzisionsbearbeitungsbefehle umzuwandeln, was ihre technischen Vorteile bei der prozessintegrierten Bearbeitung von Strukturteilen aus Titanlegierungen für die Luft- und Raumfahrt sowie von Implantaten für medizinische Geräte unter Beweis stellt. Intelligente Werkzeugmaschinen, die mit adaptiven Steuerungssystemen ausgestattet sind, können Schwankungen der Zerspanungskraft und des Werkzeugverschleißes in Echtzeit erfassen und mit der industriellen Internet-of-Things-Plattform kombiniert werden, um eine Cloud-basierte Optimierung der Bearbeitungsparameter zu erreichen, die flexible Produktionslösungen für Automobilformen, optische Geräte und andere Präzisionsfertigungsbereiche bietet.
Laserschneidmaschine
Die Laserschneidanlage basiert auf einem Hochleistungs-Faserlaser und einer Galvanometer-Positionierungstechnologie und ermöglicht das Präzisionsschneiden von Edelstahl, Aluminiumlegierungen und anderen Metallblechen im Mikrometerbereich durch berührungslose Bearbeitung. Das intelligente Überwachungssystem kann automatisch die oxidierte Schicht von Kohlenstoffstahl erkennen und die Fokusposition anpassen, was die Effizienz bei der Bearbeitung von Batterieblechen für neue Energieautos und Kühlkörpern für elektronische Komponenten erheblich verbessert. Die 10.000-Watt-Laserschneidanlage durchbricht den Engpass beim Schneiden dicker Bleche, und mit dem automatischen Be- und Entlade-Roboterarm bietet sie einen wetterunabhängigen Dauerbetrieb für die Baumaschinen- und Schiffbauindustrie, und die Technologie zur Kontrolle der Wärmeeinflusszone garantiert effektiv die spätere Schweißqualität der Präzisionsteile.
Wasserstrahlschneidmaschine
Die Wasserschneidmaschine nutzt das Kaltschneideverfahren des mit Granatsand vermischten Ultrahochdruck-Wasserstrahls und bewahrt die ursprünglichen Materialeigenschaften bei der Bearbeitung von Kohlefaserverbundwerkstoffen und marmorförmigen Dekorationsteilen dank ihres einzigartigen Vorteils, dass sie sich nicht thermisch verformt. Der dynamische Fünf-Achsen-Schneidkopf ermöglicht eine präzise Trennung dreidimensionaler Konturen von keramischen Beschichtungen auf Turbinenschaufeln und Behältern aus lebensmittelechtem Kunststoff durch die Technologie des räumlichen Winkelausgleichs. Seine umweltfreundlichen Eigenschaften eliminieren die beim herkömmlichen Schneiden entstehende Staubbelastung vollständig und machen es zum bevorzugten Verfahren für anspruchsvolle Bearbeitungsszenarien in der medizinischen Verbrauchsgüterindustrie und der architektonischen Vorhangfassade.
Bearbeitungsverfahren
Schnittprinzipien
SchnittprinzipienZerspanungsbewegung: Die Zerspanungsbewegung ist die Relativbewegung zwischen dem Werkzeug und dem Werkstück, einschließlich der Hauptbewegung und der Vorschubbewegung.
SchnittgeschwindigkeitSchnittgeschwindigkeit: Die Schnittgeschwindigkeit ist die momentane Geschwindigkeit eines bestimmten Punktes an der Schneide eines Werkzeugs relativ zur Oberfläche des zu bearbeitenden Werkstücks in Richtung der Hauptbewegung.
SchnitttiefeSchnitttiefe: Die Schnitttiefe ist der vertikale Abstand zwischen der zu bearbeitenden Oberfläche und der zu bearbeitenden Fläche.
Schneidewerkzeuge
Werkstoffe für Schneidwerkzeuge:: Zu den häufig verwendeten Werkzeugmaterialien gehören Schnellarbeitsstahl, Hartmetall, Keramik und superharte Materialien.
Geometrie der WerkzeugeDie geometrischen Parameter des Werkzeugs, einschließlich der Vor- und Nachlaufwinkel, der Hauptauslenkung und der Wölbung, wirken sich unter anderem auf die Schnittkräfte, die Schnittwärme, die Lebensdauer und die Oberflächenqualität des Werkstücks aus.
Schärfen von Werkzeugen:: Das Schärfen von Werkzeugen umfasst die Auswahl der Schleifscheibe, das Schärfverfahren und die Qualitätsprüfung des Schärfens.
Schneidflüssigkeit
Die Rolle der Kühlschmierstoffe:: Zu den Aufgaben von Kühlschmierstoffen gehören Kühlung, Schmierung, Reinigung und Rostschutz.
Arten von Kühlschmierstoffen:: Zu den Arten von Kühlschmierstoffen gehören Emulsionen, synthetische Kühlschmierstoffe und Schneidöle.
Auswahl der Schneidflüssigkeit:: Die Auswahl des Kühlschmierstoffs sollte auf der Grundlage der Bearbeitungsanforderungen, der Werkstück- und Werkzeugwerkstoffe und anderer Faktoren erfolgen.
Bearbeitungsverfahren
Brutto Zubereitung
Auf der Grundlage der mechanischen Eigenschaften der Teile werden die endkonturnahen Rohlinge durch Gießen, Schmieden oder 3D-Druck hergestellt, das heißisostatische Pressverfahren wird zur Beseitigung interner Defekte bei Strukturteilen aus Titanlegierungen für die Luft- und Raumfahrt verwendet, und die Druckgussrohlinge aus Aluminiumlegierungen müssen röntgenologisch untersucht werden, um sicherzustellen, dass die Porositätsrate <0,2% beträgt. Intelligent Manufacturing Workshop gleicht die Rohlingschargen automatisch mit den Bearbeitungsaufträgen über das MES-System ab, wodurch eine lückenlose Prozessverfolgung vom Rohmaterial bis zur Grobbearbeitung erreicht wird. Intelligente Fertigungswerkstatt
Positionierung des Werkstücks
Das modulare Spannsystem nutzt das Prinzip der Sechs-Punkt-Positionierung. Der hydraulische Spreizdorn gewährleistet eine Rundlaufgenauigkeit von 0,005 mm für dünnwandige Zylinderteile, und der fünfflächige Vakuumsauger bietet eine zerstörungsfreie Spannlösung für geformte Verbundwerkstoffe. Für die Bearbeitung von Motorgehäusen für neue Energiefahrzeuge werden Laserscanner und adaptive Spannkraftregelung eingesetzt, um den Einfluss von Schwankungen der Rohteilgröße auf die Positionierungsreferenz zu kompensieren.
Vorbereitung der Werkzeuge
Basierend auf den Daten der Schnittsimulation zur Vorhersage der Werkzeuglebensdauer können PVD-beschichtete Hartmetallwerkzeuge das intermittierende Schneiden von Hochtemperaturlegierungen bewältigen, und diamantbeschichtete Bohrer können eine gratfreie Bearbeitung von Kohlefaserverbundwerkstoffen erreichen. Ein intelligentes Werkzeugmagazin identifiziert automatisch die Werkzeugparameter über einen RFID-Chip und kalibriert synchron den Werkzeugkompensationswert während des Werkzeugwechsels im Bearbeitungszentrum, um die Maßhaltigkeit bei der Bearbeitung von Formhohlräumen in der Automobilindustrie zu gewährleisten.
Bearbeitung
Die mehrachsigen CNC-Werkzeugmaschinen implementieren eine vollständige sequentielle Bearbeitungsstrategie, das Fräs-Dreh-Zentrum erledigt die Innen- und Außenprofilbearbeitung von Flugzeugtriebwerksmagazinen in einer Aufspannung, die Mikroschmierungstechnologie erhöht die Zerspanungsleistung von Inconel 718 um 40%. Das 5-Achsen-Bearbeitungszentrum verlängert die Werkzeugstandzeit bei der Bearbeitung von tiefen Nuten durch oszillierendes Fräsen um das Dreifache und arbeitet mit einem Online-Messsystem zusammen, um die Abweichung der Werkzeugwege in Echtzeit zu korrigieren.
Werkstück-Inspektion
Coordinate Measuring Machine (CMM), um digitale Inspektion geschlossenen Kreislauf zu bauen, blaues Licht-Scanner, um Turbinenschaufel Profilabweichung zu erfassen, industrielle CT zerstörungsfreie Prüfung von Aluminium-Legierung Gießen interne Schrumpfung. SPC-System statistische Analyse der wichtigsten Dimensionen der CPK-Wert, AI visuelle Inspektion von Oberflächenfehlern Identifizierung Genauigkeit von 99,7%, ist die Inspektion Daten automatisch auf die QMS-System hochgeladen, um elektronische Qualitäts-Dateien zu generieren.
Qualitätskontrolle bei der Bearbeitung
Fehleranalyse bei der Bearbeitung
ursprünglicher Fehler:: Bezieht sich auf Werkzeugmaschinen, Vorrichtungen, Werkzeuge und das Werkstück selbst, z. B. Herstellungs- und Montagefehler.
Verarbeitungsfehler:: Fehler, die auf verschiedene Faktoren im Bearbeitungsprozess zurückzuführen sind, wie Schnittkräfte, Schnittwärme, Werkzeugverschleiß und so weiter.
ErkennungsfehlerFehler, die durch Faktoren wie Messgeräte, Messverfahren und Messumgebung während des Messvorgangs verursacht werden.
Methoden der Qualitätskontrolle
prophylaktische Kontrolle:: Reduzierung von Fehlern und Verbesserung der Produktqualität durch Design und Prozesskontrolle.
Prozesssteuerung:: Sicherstellung einer konstanten Produktqualität durch Überwachung und Anpassung der Verarbeitung in Echtzeit.
Kontrolle des fertigen ProduktsInspektion und Prüfung von Fertigerzeugnissen, um sicherzustellen, dass sie die festgelegten Anforderungen erfüllen.
Qualität der bearbeiteten Oberfläche
OberflächenrauhigkeitDie Höhe der mikroskopischen Oberflächenunebenheiten, die die Verschleißfestigkeit und Dauerfestigkeit des Teils beeinflussen.
Grad der OberflächenwelligkeitForm und Größe der Oberflächenrillen, die sich auf die Ermüdungsfestigkeit und die Dichtigkeit des Teils auswirken.
Oberflächenveredelung Textur:: Die Oberflächenbearbeitung hinterlässt Spuren und Texturen, die das Aussehen und die Passgenauigkeit des Teils beeinträchtigen.
Kontrolle der Maßgenauigkeit bei der Bearbeitung
MaßhaltigkeitDer Grad der Übereinstimmung der tatsächlichen Abmessungen eines bearbeiteten Teils mit den angegebenen Abmessungen.
PositionsgenauigkeitPositioniergenauigkeit: Die Positioniergenauigkeit des Werkstücks relativ zur Werkzeugmaschine während der Bearbeitung beeinflusst die Montagegenauigkeit des Teils.
Wiederholung der PositionierungsgenauigkeitDie Genauigkeit der wiederholten Positionierung einer Werkzeugmaschine unter denselben Bedingungen, was die Stabilität und Zuverlässigkeit der Werkzeugmaschine widerspiegelt.
Beginn der Bearbeitung von Einzelteilen
Ningbo Hersin bietet CNC-Bearbeitungslösungen für komplexe Teile aus einer Hand und bietet Präzisionsbearbeitungsdienstleistungen für den gesamten Zyklus, vom Rapid Prototyping bis zur Massenproduktion. Hersin stützt sich auf vernetzte Fünf-Achsen-Bearbeitungszentren, Fräs-Dreh-Anlagen-Cluster und Schweizer Baume Ultrapräzisions-Werkzeugmaschinen und ist auf die Produktion von Automobilteilen und anderen Produkten spezialisiert. Laden Sie Ihre Zeichnungen in das Smart Quotation System hoch und erhalten Sie einen versicherungsmathematischen Bericht mit DFM-Optimierung und Werkzeugverschleißanalyse.Kontaktieren Sie uns
Sicherheitsvorschriften für Verarbeitungsgeräte
Inspektion der Ausrüstung vor der Inbetriebnahme
Überprüfen Sie die Druckstabilität des Hydrauliksystems (20-25 MPa) und die Dichtheit der Pneumatikleitung, verwenden Sie die Infrarot-Thermografie, um Anomalien bei der Temperatur der Spindelmotorwicklung festzustellen, und überprüfen Sie die doppelten Schutzeinstellungen des CNC-Systems für Soft-Limit und Hard-Limit. Bei Fünf-Achsen-Bearbeitungszentren sollte zusätzlich der Verriegelungsmechanismus des Drehtisches überprüft werden, der Fehler der Positioniergenauigkeit der Führungsbahn sollte mit einem Laserinterferometer ≤ 0,02 mm festgestellt werden, und die remanente Magnetstärke der Magnetsauger sollte ≤ 5 Gauß sein, wenn das Werkstück aus Kohlenstoffstahl eingespannt ist.
Betriebsverfahren für die Ausrüstung
Strenge Einhaltung der SOP-Parameter: Die Schnittgeschwindigkeit beim Schruppfräsen von Gusseisen ist auf 150-220 m/min begrenzt, und die Vorschubgeschwindigkeit des Hartmetallwerkzeugs wird entsprechend der Steigung von ap=2mm×ae=35mm eingestellt. Bei der Bearbeitung von Titanlegierungen muss das Mikroschmiersystem (MMS) aktiviert und die Rauchkonzentration im Schneidbereich überwacht werden, der Bediener muss eine stoßfeste Maske und flammhemmende Kleidung tragen, und bei einem Spindelüberlastungsalarm muss der Notbremsschalter sofort ausgelöst werden.
Wartung von Geräten nach der Abschaltung
Geschlossener Kreislauf zur Reinigung von Metallrückständen im Kühlschmierstofftank und Prüfung des pH-Werts (8,5-9,2), Verwendung einer Ultraschall-Reinigungsmaschine zur Entfernung von mikrometergroßen Ölfilmrückständen auf der Kegeloberfläche des Werkzeugschafts. Monatliche Kompensation des Kugelgewindespiels (C3-Präzisionsspindelkompensation ≤ 0,015 mm), Vorhersage der Spindellagerlebensdauer durch Schwingungsspektralanalyse, und die Fettfüllmenge ist auf ±0,5 ml genau.
Fallstudie: Bearbeitungsunfälle
Unfallfall I
Eine Autoteile Fabrik CNC-Drehmaschine Spindel Überhitzung Feuer: der Bediener verletzt die Abschaltung des Kühlmittels für Edelstahl kontinuierliche Drehen, Schneiden Temperatur über 900 ℃ induzierten Kraftstoffnebel. Nach dem Unfall war es zwingend erforderlich, ein Wärmebildüberwachungssystem zu installieren und ein thermodynamisches Schnittmodell in die SPS zu implantieren, um eine Temperatur-Geschwindigkeits-Kopplung zu erreichen.
Unfallfall II
Gantry-Fräsmaschine Schutz Türverriegelung Versagen der Behinderung: Ausrüstung Umwandlung Abschirmung Sicherheitsgitter Signale, Eisenspäne spritzen durch die 5mm Acryl-Schallwand. Rectification Programm auf IP67 Schutzniveau der druckempfindlichen Bodenmatten und Dual-Circuit-Gitter, Trigger Reaktionszeit ≤ 0,3 Sekunden aktualisiert.
Entwicklungstrends und Herausforderungen bei der Bearbeitung
Entwicklungstrend der Bearbeitungstechnologie
- Digitaler Zwillingsantrieb: Echtzeit-Abbildung des Werkzeugmaschinenstatus in der Cloud, Bearbeitungsfehler-Vorhersagegenauigkeit von 99,2%
- Revolution in der Composite-Bearbeitung: Integrierte Dreh-, Fräs-, Bohr- und Schleifeinrichtungen reduzieren die Anzahl der Aufspannungen und verkürzen die Zykluszeit für die Laufradbearbeitung um 60%
- Umweltfreundliche Produktion: Wasserstoffschneidetechnik ersetzt Emulsion und reduziert den Kohlenstoff-Fußabdruck von 45%
Herausforderungen für die zerspanende Industrie
- Hochqualifizierte Talente Fehler: 5-Achsen-Programmierung Techniker Mangel an 37%, müssen AR Remote Guidance System, um die Lücke zu füllen
- Engpass bei der Bearbeitung superharter Werkstoffe: Werkzeugstandzeit bei der Bearbeitung von Siliziumkarbidspiegeln nur 15 Minuten, dringender Bedarf an Durchbrüchen in der plasmagestützten Schneidtechnologie
- Datensicherheitsrisiko: Schwachstelle im CNC-System führt zur Manipulation des G-Codes, verschlüsselte Übertragung der Blockchain erforderlich
Perspektiven für die Entwicklung der Zerspanungstechnik
Die Quantenmesstechnik bringt die Genauigkeit der Maßkontrolle auf Nanometerebene voran, selbstentwickelnde KI-Algorithmen erhöhen die Effizienz der dynamischen Optimierung von Schneidparametern um 300%. 2030 werden die Gestensteuerung von Werkzeugmaschinen auf der Grundlage von Brain-Computer-Interfaces und emissionsfreie Trockenbearbeitungszentren zum Standard in der High-End-Fertigung werden, und das Modell der Mikrofabrik wird die Lieferkette in der Luft- und Raumfahrt neu strukturieren.