Rapid Tooling: Innovative Lösungen zur Beschleunigung von Produktentwicklung und Fertigung
发布时间:2025-02-14 分类:Nachrichten 浏览量:1734
Im Zeitalter des raschen technologischen Wandels durchläuft die Fertigungsindustrie einen tiefgreifenden Wandel von "scale first" zu "agil und effizient". Rapid Tooling (Schnelles Vorwort: Chinas Dilemma und Durchbrüche im Formenbau
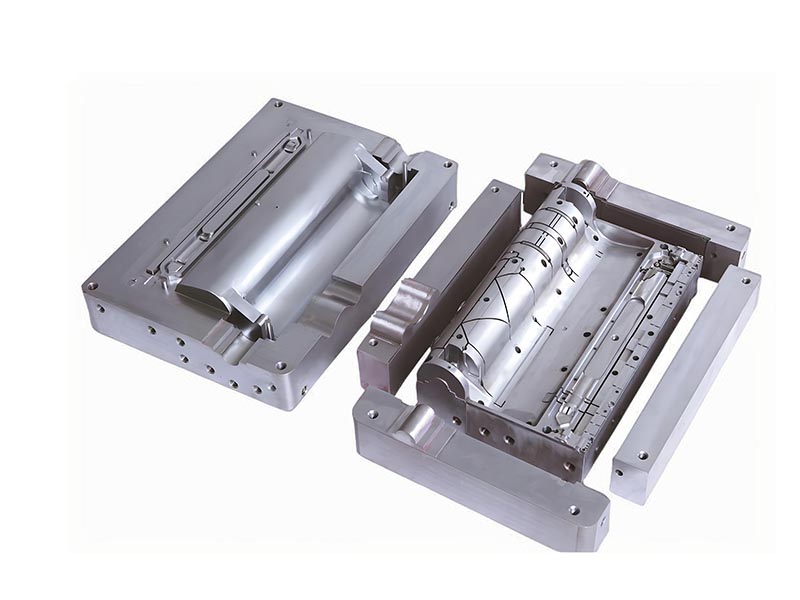
Als Ingenieur, der seit 23 Jahren in der Gießereiindustrie tätig ist, habe ich (He Xin) den Wandel Chinas von einem großen Importeur von Gussformen zu unabhängiger Innovation miterlebt. In Ningbo, dem Zentrum der Gießereiindustrie, haben wir die Erfahrung gemacht, dass der traditionelle Entwicklungszyklus von Stahlformen lang ist, dass hohe Kosten für Versuch und Irrtum anfallen, aber wir haben auch die revolutionären Durchbrüche erlebt, die durch die Schnellformtechnologie erzielt wurden. Dieses Papier wird das Hochdruckgießen kombinieren, Niederdruckguss und andere praktische Anwendungsszenarien, die die Rolle des Rapid Tooling in der Aluminium Kritische technische Logik in der Komponentenfertigung.
1. das Wesen der schnellen Formen: kein Kompromiss, sondern eine genaue Übereinstimmung
1.1 Drei Hauptprobleme der traditionellen Formen
- ZeitaufwandDie Entwicklung einer Druckgussform kann bis zu 8-12 Wochen dauern.
- finanzieller Druck: Form für Automotorengehäuse kostet über 2 Millionen Dollar
- Risiko durch Versuch und Irrtum:: Schwerkraftguss Eine bauliche Veränderung der Form kostet zusätzlich 150.000 $.
1.2 Technische Ausrichtung des Rapid Tooling
Erreicht durch dreifache Innovation in Materialwissenschaft, Verarbeitung und Simulationstechnologie:
- Zyklus Verdichtung 70%Mindestens 7 Arbeitstage vom Entwurf bis zur Probeformung
- Kostenreduzierung 50%-80%Aluminiumformen: Die Kosten für Aluminiumformen können auf $80.000 - $150.000 begrenzt werden.
- Präziser Abgleich von VersuchsproduktionsmengenUnterstützt den Bedarf an Pilotanlagen von 500 bis 30.000 Stück.
2、Schnelle Formlösungen für vier wichtige Gießverfahren
2.1 Druckguss-Szenario (HPDC)
Hochdruckguss ist ein Verfahren, bei dem geschmolzene Aluminiumlegierungssuppe von 680-720°C mit einer Geschwindigkeit von 10-50m/s unter einer Schließkraft von 1600-2000T in den Formhohlraum gepresst wird, und die zentrale Herausforderung besteht darin, dass die Form extremen thermomechanischen Belastungen standhalten muss. Die Innovation von Rapid Tooling in diesem Szenario spiegelt sich in der doppelten Optimierung von Material und Struktur wider: QRO90-Warmarbeitsstahl wird verwendet, um den traditionellen H13-Stahl zu ersetzen, dessen Molybdän-Vanadium-Legierungszusammensetzung die thermische Ermüdungsbeständigkeit um 40% erhöht und zusammen mit der Nitrierbehandlung der Oberfläche (Schichttiefe von 0,2-0,3mm) die Lebensdauer des Werkzeugs auf mehr als 30.000 Formzyklen verlängern kann. Strukturelle Gestaltung des modularen Einsatzes System, für gefährdete Bereiche (z. B. Tore, Auswerferstift Position) für die lokale Verstärkung, ein Unternehmen in Ningbo, die Produktion von neuen Energie-Motor Endabdeckung, durch den schnellen Austausch von Einsätzen zur Verkürzung der Form Wartungszeit von 8 Stunden auf 1,5 Stunden. Was die Wirtschaftlichkeit betrifft, so sinken die Kosten pro Stück von ¥18,6 auf ¥7,3 für herkömmliche Formen, und der Entwicklungszyklus wird auf 12 Tage verkürzt, was sich besonders für Projekte im Bereich der Kfz-Strukturteile mit einer Jahresproduktion von weniger als 50.000 Stück eignet.
Technische Schwierigkeiten::
- Die Form muss einer Schließkraft von 1600T standhalten
- Aluminiumlegierungen schmelzen bei Temperaturen von bis zu 700°C
- Anforderung an die Lebensdauer der Module >50.000 Zyklen
Rapid Tooling Lösungen::
- Material-UpgradesErsatz des herkömmlichen H13-Stahls durch den Warmarbeitsstahl QRO90
- Strukturelle OptimierungEinsätze werden im Kern verwendet, um kritische Bereiche lokal zu verstärken.
- EchtzeitdatenKühlkörpergehäuse für 5G-Basisstationen mit einer Lebensdauer von 32.000 Formzyklen in Ningbo, China.
2.2 Niederdruckguss-Szenarien (LPDC)
Beim Niederdruckguss wird die Aluminiumflüssigkeit mit einem Luftdruck von 0,5-0,8 MPa gleichmäßig in den Formhohlraum eingespritzt, was sich besonders für die Herstellung von dünnwandigen Teilen eignet, die eine hohe Dichte erfordern. Der Durchbruch der Schnellform in diesem Bereich konzentriert sich auf die Optimierung der Temperaturregelung und des Gießsystems: die Entwicklung eines Mehrzonen-Temperaturregelungssystems (±2℃ Genauigkeit) mit Gradienten-Kühlkanal-Design, so dass die Ausbeute der von einem Unternehmen in Ningbo hergestellten neuen Energie-Batterieplatte von 81% auf 95% gestiegen ist. das durch Topologie-Optimierungstechnologie entworfene Gießsystem hat die Füllzeit von 9,2 Sekunden auf 6,8 Sekunden verkürzt und die Nutzungsrate des Metalls um 12% erhöht. Die Rapid-Tooling-Lösung verwendet vorgehärteten P20-Stahl und Einsätze aus einer lokalen Kupferlegierung, was die Werkzeugkosten auf 45% im Vergleich zur herkömmlichen Lösung senkt. Sie eignet sich besonders für die Pilotprüfung komplexer Strukturteile wie Hydraulikgehäuse für die Luft- und Raumfahrt mit einer typischen Projektvorlaufzeit von 15-20 Tagen und unterstützt die Kleinserienproduktion von 3.000-8.000 Stück.
technologischer Durchbruch::
- Entwicklung eines speziellen Systems zur Kontrolle der Formtemperatur (±2℃ Genauigkeit)
- Design des Gradienten-Kühlkanals
- Fall (Recht)Ein neues Energiefahrzeug-Motorgehäuseprojekt, der Produktertrag stieg von 78% auf 93%.
2.3 Szenario Schwerkraftgießen
Das Schwerkraftgießen beruht auf der selbstgewichtigen Füllung der Metallflüssigkeit und wird häufig für die Herstellung großer und komplexer Teile verwendet. Rapid Mould hat drei wichtige Innovationen in diesem Bereich erreicht: erstens, 3D-Druck Sandform und Metallform Verbundtechnologie, durch das SLS-Verfahren, um einen Sandkern (Präzision CT8 Ebene) mit dem Stahl äußeren Form kombiniert zu produzieren, so dass der Motor Zylinderblock Versuch Produktionszyklus von 45 Tagen auf 12 Tage; zweitens, die Wärmebilanz Kontrollsystem, in den Schlüsselbereichen der Form Kupferlegierung Einsätze (Wärmeleitfähigkeit 380W/m-K) eingebettet, so dass ein Marine-Dieselmotor Zylinderkopf des Der Temperaturgradient wurde um 40% reduziert; drittens, intelligentes Auspuffdesign, das poröse Metallentlüftungsstopfen anstelle von traditionellen Auspuffschlitzen verwendet, reduzierte die Gussporositätsfehlerrate von 15% auf unter 3%. Wirtschaftliche Daten zeigen, dass die Anzahl der Versuchsformen des Schnellformprogramms im Durchschnitt um das 2,3-fache reduziert wird und die Kosten für eine einzelne Versuchsform ¥ 12-18.000 Yuan betragen, was sich besonders für die Entwicklung von großen Baumaschinenkomponenten mit einem Einzelstückgewicht von mehr als 50 kg eignet.
Innovative Praktiken::
- Kombinierte Technologie für 3D-Drucksand und Metallformen
- Örtliche Einlage einer Kupferlegierung zur Verbesserung des Wärmehaushalts
- wirtschaftlicher NutzenReduzierung der Anzahl der Formversuche um 40% und der Zykluszeit um 65% durch Optimierung des Gießsystems
3、Fünf Kerntechnologien der Schnellformtechnik
3.1 Matrix für die Materialauswahl
Anwendungsszenario | Empfehlungsmaterial | Härte (HRC) | Wärmeleitfähigkeit (W/m-K) | Kostenindex |
---|---|---|---|---|
Hochdruckguss | H11+ Oberflächen-Nitrierung | 48-52 | 24.3 | ★★★★ |
Aluminiumlegierungen in kleinen Mengen | 7075 Aluminium für die Luft- und Raumfahrt | 35-40 | 130 | ★★★ |
Hochpräzise Strukturteile | S7-Werkzeugstahl | 54-56 | 29.4 | ★★★★☆ |
3.2 Vergleich von Oberflächenbehandlungsverfahren
- Mikro-Lichtbogen-OxidationBildung einer 10-30μm dicken Keramikschicht, temperaturbeständig >800°C
- DLC-BeschichtungReduzierung des Reibungskoeffizienten auf 0,1, wodurch sich die Lebensdauer der Form um das Dreifache erhöht
- Beispiel aus der PraxisDie Form eines Turboladergehäuses wird mit einer Kompositbeschichtung behandelt, und die Form hält mehr als 80.000 Mal.
3.3 Modell zur Vorhersage der Lebenszeit
Basierend auf Moldflow-Simulationsdaten mit Feldüberwachung:
L=K× (σappliedσUTS)m×Nthermal
Darunter:
- KMaterialkonstanten (0,8-1,2 für Aluminiumlegierungen)
- mErmüdungsindex (6,5 für Stahlformen, 4,2 für Aluminiumformen)
- Beispiele für AnwendungenVorhersagefehler innerhalb von ±8%
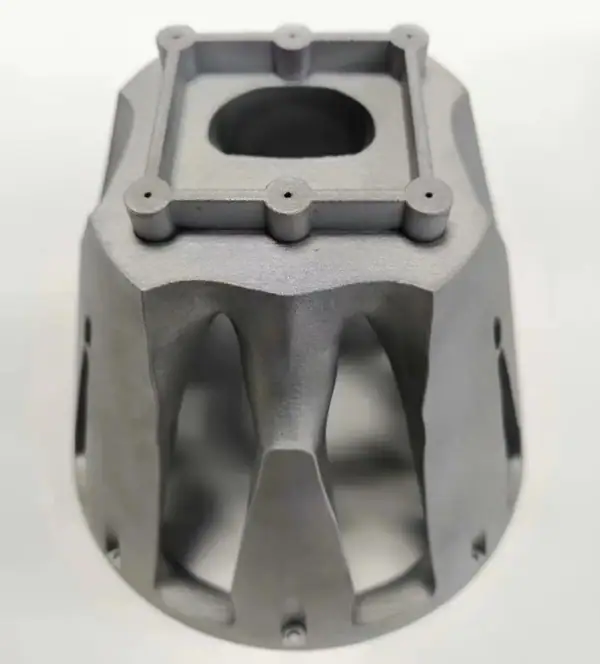
3D-Druck Rapid Prototyping
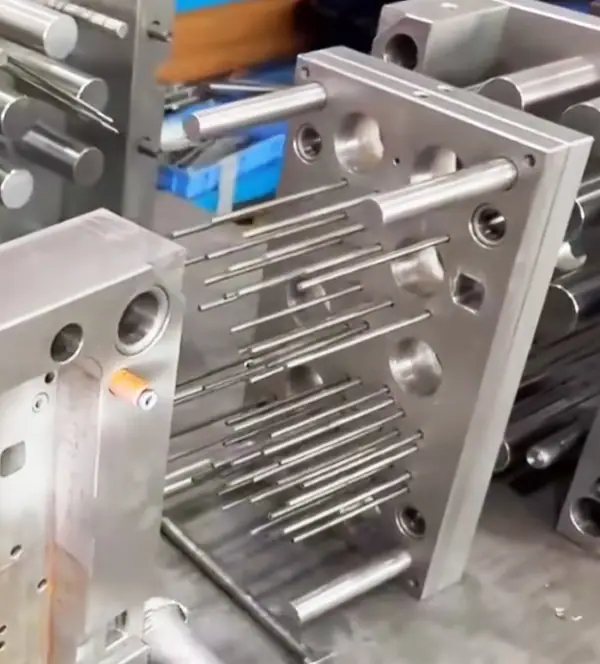
Rapid Tooling
4、Die Integration von 3D-Druck und schneller Formeninnovation
Der konforme Kühlwasserkanal ist der Hauptvorteil von 3D-Druckformen: Bei Formen, die mit der SLM-Technologie hergestellt werden, kann der Abstand zwischen dem Kühlkanal und der Produktkontur auf 1,5-2 mm eingestellt werden (herkömmlicher Bohrprozess ≥ 8 mm), so dass der Einspritzzyklus eines Kühlergrills von 48 Sekunden auf 32 Sekunden verkürzt und der Verformungsgrad von 0,8 mm auf 0,3 mm reduziert werden kann.Mit der Gradientenmaterial-Drucktechnologie kann die Kombination der hohen Härte von HRC55 auf der Oberfläche des Kerns und der hohen Zähigkeit von HRC35 im Kern erreicht werden. Durch die Kombination der hohen Härte von HRC35 auf der Oberfläche des Kerns und der hohen Zähigkeit von HRC35 im Kern wurde eine Form für eine Drohnenhalterung mit dieser Technologie behandelt, und die Schlagfestigkeit wurde um 60% verbessert. Eine wirtschaftliche Analyse zeigt, dass bei komplexen Formen mit mehr als 5 geformten Wasserwegen die Gesamtkosten der 3D-Drucklösung im Vergleich zu CNC um 42% gesenkt werden können, was sich besonders für Präzisionsszenarien wie Formen für medizinische Mikrofluidikchips eignet. Die derzeitigen technischen Beschränkungen liegen in der maximalen Formgröße (die meisten Geräte ≤ 500 mm) und den Anforderungen an die Nachbearbeitung (wichtige Passflächen müssen noch CNC-gefertigt werden), aber mit der Entwicklung der Multilasertechnologie wird erwartet, dass der Gesamtdruck von Formen im Metermaßstab im Jahr 2025 erreicht werden kann.
4.1 Technologische Durchbruchspunkte
- Konforme KühlkanäleVerkürzung der Einspritzzykluszeit um 23% und Reduzierung der Verformung um 40%.
- Druck von Material mit FarbverlaufKernoberflächenhärte HRC55, innere Zähigkeit HRC35
- FalldatenA: Verbesserung der Kühlleistung der LED-Lampenschirmform um 37%
4.2 Wirtschaftliche Analyse
Norm | Konventionelle CNC-Formen | 3D-gedruckte Gussformen |
---|---|---|
Entwicklungszyklus | 18 Tage | 6 Tage |
Komplexe Strukturkosten | 100% | 65% |
Kosten der Änderung | 30% | 8% |
5) Drei praktische Empfehlungen für Unternehmen des verarbeitenden Gewerbes
- Einführung eines Systems zur Einstufung von Formen::
- Formen der Klasse A (>100.000 Formen): konventionelle Stahlformen
- Formen der Klasse B (10.000-50.000 Formen): Schnellstahl-Formen
- Formen der Klasse C (<10.000 Formen): 3D-Druck/Aluminium-Formen
- Implementierung von digitalen Zwillingen::
- Einführung des MAGMA-Simulationssystems in der Phase der Werkzeugkonstruktion
- Installation von IoT-Sensoren zur Überwachung der Spannungsverteilung während der Produktionsphase
- Aufbau eines Krisenreaktionsmechanismus::
- Reservebibliothek mit standardisierten Formteilen (für die gemeinsame Spezifikation 80%)
- Aufbau regionaler Kooperationsnetze (Ningbo hat einen 2-Stunden-Kreis für die Lieferkette gebildet)
Schlussfolgerung: Die nächsten zehn Jahre der Formenbauindustrie
Mit dem Projekt der Ningbo Mould Cloud Platform, das wir derzeit umsetzen, wandeln sich Schnellformwerkzeuge in intelligente und serviceorientierte Werkzeuge:
- Intelligentes Angebotssystem5 Minuten, um eine Formlösung durch Eingabe von Parametern zu erstellen
- Blockchain-RückverfolgbarkeitRückverfolgbarkeit der Qualität über den gesamten Lebenszyklus
- Gemeinsame FormenbibliothekSenkung der Lagerkosten von SME 30%
Rapid ToolingHäufig gestellte Fragen (FAQ)
F1: Kann Rapid Tooling für die Massenproduktion verwendet werden?
A: Eine szenariobasierte Bewertung ist erforderlich:
- Form aus Aluminiumlegierung: geeignet für Kleinserien <5000 Stück
- Vorgehärtete Stahlformen: können 30.000-50.000 Stück tragen
- Es wird empfohlen, ein digitales Überwachungssystem einzubauen, um den Zustand der Form in Echtzeit zu beurteilen.
Q2:Wie lässt sich die Maßhaltigkeit von Rapid Tooling kontrollieren?
A: Empfohlenes Programm:
- Bearbeitungsphase: mit 5-Achsen-Werkzeugmaschinen + Inline-Messung (Genauigkeit ±0,02 mm)
- Erprobungsphase der Form: vollständige Prüfung der kritischen Abmessungen mit einer Koordinatenmessmaschine (KMG)
- Phase der Massenproduktion: Probenahme und Prüfung alle 500 Gussformen
F3: Welches sind die innovativen Technologien für die Oberflächenbehandlung von Rapid Tooling?
A: Drei Spitzentechnologien:
- Laserauftragsschweißen: Reparatur verschlissener Stellen zu geringeren Kosten 40%
- Nanokomposit-Beschichtung: Reibungskoeffizient auf 0,08 reduziert
- Plasmanitrierung: Oberflächenhärte bis zu HV1200
F4: Wo liegen die Grenzen von 3D-gedruckten Formen?
A: Derzeitige wesentliche Einschränkungen:
Nachbearbeitungsanforderungen: Häufig ist eine CNC-Bearbeitung kritischer Oberflächen erforderlich.
Maximale Größe: Die meisten Geräte sind auf 500 x 500 x 500 mm begrenzt.
Materialauswahl: Derzeit die wichtigsten Unterstützung für die Stahl, Aluminium-Legierung