Die Geschichte der Entwicklung von CNC-Drehmaschinen: vom einfachen Drehen bis zur technologischen Revolution bei der Herstellung komplexer Teile
发布时间:2025-02-24 分类:Nachrichten 浏览量:1612
Als lebendes Fossil der industriellen Zivilisation zeigt die Entwicklung der CNC-Drehmaschine das ewige Streben nach Präzisionsfertigung. Von 1300 v. Chr. ägyptischen Handwerker mit seilbetriebenen hölzernen Drehbett, bis zum 21. Jahrhundert mit AI-Algorithmen fünf-Achsen-intelligente Werkzeugmaschinen ausgestattet, hat die Technologie immer in der Neudefinition der "Präzision" der Grenzen der industriellen Revolution Zeit der dampfbetriebenen Drehmaschine wird auf 0,1mm Bearbeitungsfehler komprimiert werden, während das moderne CNC-System durch die Skala Closed-Loop-Steuerung erreicht hat 0,0000mm. Während der industriellen Revolution, dampfbetriebene Drehmaschinen komprimiert Bearbeitungsfehler zu 0,1mm, während die modernen CNC-Systeme haben mikroskopische Kontrolle von 0,001mm durch Closed-Loop-Skala Kontrolle erreicht. Besonders in der HochleistungsAluminiumIm Bereich der Komponentenherstellung hat die mehrachsige synergetische Fähigkeit der CNC-Drehmaschine den traditionellen Prozess vollständig verändert: Nehmen wir das Motorgehäuse eines neuen Energiefahrzeugs als Beispiel, so kann die Verbundbearbeitung des Wärmeableitungszahnstücks und der Lagerbohrung gleichzeitig in dem CNC-System mit integriertem Y-Achsen-Leistungsrevolver abgeschlossen werden, was die Effizienz der 400% im Vergleich zur traditionellen sequentiellen Bearbeitung verbessert und den Koaxialitätsfehler auf weniger als 5 μm kontrolliert, und dieser Technologiesprung konfiguriert nicht nur den Produktionsprozess neu, sondern fördert auch die technischen Grenzen des Leichtbaus. Dieser technologische Sprung rekonfiguriert nicht nur den Produktionsprozess, sondern verschiebt auch die technischen Grenzen des Leichtbaus.
Die Entwicklung von CNC-Werkzeugmaschinen
Eine CNC-Werkzeugmaschine ist eine Werkzeugmaschine, die Informationen in Form eines digitalen Codes (Programmanweisungen) zur Steuerung des Werkzeugs verwendet, um automatische Bearbeitungen gemäß einem vorgegebenen Arbeitsprogramm, einer bestimmten Bewegungsgeschwindigkeit und einer bestimmten Bahn durchzuführen; sie wird als CNC-Werkzeugmaschine bezeichnet.
Zeitintervall | Entwicklungsveranstaltung | Technische Merkmale |
1952 | Parsons und das Massachusetts Institute of Technology (MIT) arbeiteten zusammen, um die weltweit erste vertikale CNC-Fräsmaschine mit Drei-Koordinaten-Gestänge zu bauen, die nach dem Impulsvervielfältigerprinzip arbeitet. | Erste Erkundungen der CNC-Technik mit Elektronenröhrensteuerung |
1954 | Bendix USA stellte die erste industrielle CNC-Werkzeugmaschine der Welt her. | Der Beginn der industriellen Anwendung von CNC-Werkzeugmaschinen markiert die erste Reife der CNC-Technologie |
1959 | CNC-Systeme der zweiten Generation mit transistorisierten Steuerungen | Höhere Zuverlässigkeit und Stabilität von Transistoren im Vergleich zu Röhren |
1965 | CNC-Systeme haben sich zur dritten Generation weiterentwickelt, die mit kleinen integrierten Schaltkreisen gesteuert werden. | Der Einsatz integrierter Schaltungen verbessert die Leistung und Zuverlässigkeit von CNC-Systemen |
1970 | Die vierte Generation von CNCs erschien und Minicomputer begannen, für CNCs verwendet zu werden. | Die Anwendung der Computertechnologie verleiht dem CNC-System ein höheres Maß an Intelligenz und Automatisierung. |
1974 | Mit dem Erscheinen der fünften Generation von CNCs wurden Mikroprozessoren in CNCs eingesetzt. | Mikroprozessoranwendungen machen CNCs flexibler und effizienter |
Ende der 1970er bis Anfang der 1980er Jahre | Die Vereinigten Staaten, Deutschland, Japan und andere Länder haben erhebliche Fortschritte auf dem Gebiet der CNC-Werkzeugmaschinen gemacht und eine Reihe von Hochleistungs-CNC-Werkzeugmaschinen auf den Markt gebracht | Die CNC-Werkzeugmaschinentechnologie reift allmählich heran, und der Anwendungsbereich wird immer größer. |
1980s | Die japanische Produktion von CNC-Werkzeugmaschinen übertrifft die der Vereinigten Staaten und ist damit der weltweit größte Hersteller von CNC-Werkzeugmaschinen. | Japans technologische Innovation und Qualitätskontrolle auf dem Gebiet der CNC-Werkzeugmaschinen haben das Land zu einem führenden Unternehmen auf dem Weltmarkt gemacht. |
1990er Jahre bis heute | Die CNC-Werkzeugmaschinentechnologie entwickelt sich weiter, die Länder haben leistungsstarke und hochpräzise CNC-Werkzeugmaschinen eingeführt. | CNC-Werkzeugmaschinen werden in Bezug auf Steuerung, Präzision, Automatisierung und Flexibilität ständig verbessert und sind in der Luft- und Raumfahrt, in der Automobilindustrie, in der Elektronik und in anderen High-End-Produktionsbereichen weit verbreitet. |
2020s | Chinas CNC-Werkzeugmaschinenindustrie entwickelt sich rasant, mit bemerkenswerten technologischen Durchbrüchen, die das ausländische Technologiemonopol brechen. | China hat erhebliche Fortschritte im Bereich der hochwertigen CNC-Werkzeugmaschinen gemacht, und die Wettbewerbsfähigkeit der im Inland hergestellten CNC-Werkzeugmaschinen hat sich weiter verbessert. |
Frühe manuelle Drehmaschine
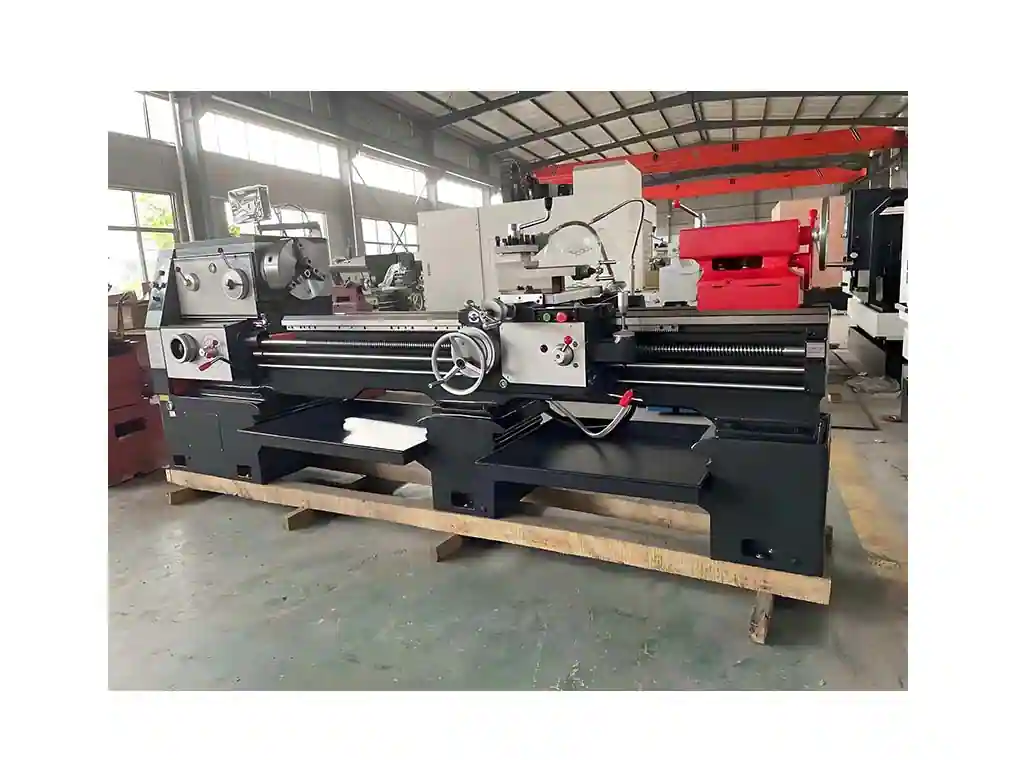
Das Wesen der Drehbearbeitung liegt in der delikaten dynamischen Synergie zwischen einem rotierenden Werkstück und einem linearen Werkzeug. Die Ursprünge dieser Fertigungstechnik lassen sich bis in die altägyptische Zivilisation um 1300 v. Chr. zurückverfolgen - Handwerker benutzten Seile aus Tiersehnen, die sie um Holz wickelten und durch Hin- und Herziehen einen Drehschnitt erzielten, und leisteten damit Pionierarbeit für die früheste Methode der Bearbeitung runder Bauteile.
Der erste qualitative Wandel in der Drehtechnik erfolgte während der industriellen Revolution, als die explosionsartige Nachfrage der metallverarbeitenden Industrie den ersten qualitativen Wandel in der Drehtechnik zur Folge hatte. Die Einführung der Dampfkraft, die Ersetzung der menschlichen Kraft durch ein Riemenantriebssystem und die vibrationsfeste Konstruktion des gusseisernen Bettes ermöglichten es der Drehmaschine erstmals, Standardteile in großen Mengen zu produzieren. Das in dieser Zeit entstandene Allrad-Getriebe ermöglichte eine Bearbeitungsgenauigkeit im Millimeterbereich und legte den Grundstein für den modernen Maschinenbau.
Heute hat das Vordringen der CNC-Technologie die DNA der Drehmaschine völlig neu strukturiert. Der Bediener wird vom Handarbeiter zum Programmarchitekten, und die Werkzeugmaschine entwickelt sich zu einem intelligenten Terminal, das selbständig komplexe Logik ausführen kann. Dieser Wandel verkürzt nicht nur den Bearbeitungszyklus komplexer Oberflächen um 60%, sondern stabilisiert auch die Maßgenauigkeit im Mikrometerbereich und markiert den offiziellen Eintritt der Fertigungsindustrie in das Zeitalter der digitalen Präzision.
Grundlegender Aufbau und Funktion von Handdrehmaschinen
Der modulare Aufbau der manuellen Drehmaschine, dem Grundstein der Zerspanung, ist auch heute noch die Inspiration für moderne Werkzeugmaschinen. Die Synergie der einzelnen Komponenten, vom gusseisernen Bett bis zum Präzisionsantriebsstrang, veranschaulicht die ursprüngliche Weisheit des Maschinenbaus und liefert die zugrunde liegende Logik für die Entwicklung der CNC-Technologie.
Liege
Das gusseiserne Bett der manuellen Drehmaschine ist in Kastenbauweise ausgeführt. Die interne gitterartige Verstärkung verbessert die Torsionssteifigkeit erheblich, und die Schwingungsdämpfungsleistung kann Schnittschwingungen von mehr als 80% absorbieren. Die Kombination aus V-Führung und ebener Führung mit Präzisionsschliff auf der Bettfläche stellt sicher, dass die lineare Genauigkeit der Schleppplattenbewegung innerhalb von 0,02 mm/m kontrolliert wird. Diese Steifigkeitsbasis ermöglicht es der Drehmaschine, die Stabilität bei der Bearbeitung von hochharten Legierungen beizubehalten, während das alterungsbehandelte Gusseisenmaterial die Verformung durch Temperaturerhöhung wirksam unterdrückt und die geometrische Genauigkeit der Langzeitbearbeitung garantiert.
Spindelkasten
Der Spindelkasten dient als Leistungszentrum mit einem eingebauten Sechsgang-Getriebe, das über einen Schiebegetriebesatz einen breiten Drehzahlbereich von 45-2000 U/min erreicht. Das modulare Design des selbstzentrierenden Dreibackenfutters und der elastischen Spannzange ermöglicht einen schnellen Wechsel der Spannlösung für Φ5-300 mm große Werkstücke, was zusammen mit der Morsekegel-Spindelschnittstelle sicherstellt, dass der Radialschlag der Werkstücke nicht mehr als 0,03 mm beträgt. Das Verbindungsdesign des drehzahlvariablen Griffs und der Kupplung ermöglicht dem Bediener ein nahtloses Umschalten der Drehzahlen während des Bearbeitungsprozesses und passt sich den Anforderungen verschiedener Szenarien an, die vom Schlichten von Aluminiumlegierungen bis zum Schruppen von Edelstahl reichen.
Buggy
Das Schleppplattensystem aus Verbundwerkstoff verfügt über eine Längs- und Quervorschubfunktion, eine Längsschraubenführung mit 6 mm/Umdrehung und ein Einstellrad für eine Feineinstellung von 0,02 mm. Der Revolverwerkzeughalter mit vier Stationen unterstützt den schnellen Werkzeugwechsel und ermöglicht den Wechsel zwischen mehreren Prozessen wie Drehen, Einstechen und Gewindeschneiden innerhalb von 15 Sekunden. Durch das Übersetzungsverhältnis des hängenden Radkastens können 60 Standardsteigungen von 0,5-10 mm erzeugt werden, um die Nachfrage nach Präzisionsgewindebearbeitung von Antriebswellen, Schrauben und anderen Teilen zu erfüllen, und die Wiederholpositioniergenauigkeit erreicht ±0,01 mm.
Kontrollen und synergetische Systeme
Das Drei-Handrad-Steuerungssystem bildet ein einzigartiges Paradigma der Mensch-Maschine-Interaktion: Die linke Hand regelt den Längsvorschub (0,05-0,3 mm/r), die rechte Hand steuert die Schnitttiefe in Querrichtung (±0,01 mm Genauigkeit), und das Fußpedal betätigt die Kupplung zum Starten und Stoppen der Spindel. Das Planetengetriebe im Werkzeugträger zerlegt die Spindelbewegung in präzise Vorschubverhältnisse, während der Halbmuttermechanismus die Vorschubgeschwindigkeit während des Gewindeschneidens automatisch synchronisiert - eine mechanische Logik, die komplexe Bearbeitungsprozesse in intuitive manuelle Vorgänge verwandelt.
Werkzeughalter und Schmierung
Der verstellbare viereckige Werkzeughalter unterstützt die Feineinstellung der Werkzeughöhe um ±2 mm und gewährleistet die Steifigkeit des Schneidprozesses durch einen Keilverriegelungsmechanismus. Das Tauchschmiersystem bietet eine kontinuierliche Ölversorgung für die Zahnräder und 8 manuelle Schmierpunkte für kritische Reibungsteile, und das Verbundschmierprogramm ermöglicht es der Maschine, auch nach 8 Stunden Dauerbetrieb einen stabilen Reibungskoeffizienten beizubehalten. Der Mechanismus zur Winkeleinstellung des Werkzeughalters unterstützt Neigungswinkeleinstellungen von -5° bis 45°, um die Anforderungen an die Bearbeitung von Kegeln, Kugeln und anderen geformten Konturen zu erfüllen.
Die Grenzen der manuellen Bedienung einer Drehmaschine im Detail erklärt
begrenzte Automatisierung
Bei der Bearbeitung von Getrieberädern für Kraftfahrzeuge muss der Bediener die Vorschubgeschwindigkeit, die Schnitttiefe und die Spindeldrehzahl synchronisieren, was für ein einziges Werkstück bis zu 50 Minuten dauert, während die CNC-Ausrüstung nur 12 Minuten benötigt. Diese hohe Abhängigkeit von manuellen Eingriffen führte zu einem Effizienzverlust von 35% in der Massenproduktion, und die Ausschussrate war bei unerfahrenen Bedienern fünfmal höher als bei Facharbeitern.
Die Komplexität der Genauigkeit
Bei der Bearbeitung von Diesel-Einspritzdüsengehäusen können Unterschiede in der Erfahrung des Bedieners zu Schwankungen der kritischen Bohrungsgrößen von 0,05-0,12 mm führen. Die thermische Verformung des Bettes verschiebt den Reitstock nach 4 Stunden kontinuierlicher Bearbeitung um 0,03 mm, und der Werkzeugverschleiß kumuliert einen Fehler von 0,1 mm pro 20 Stück - Variablen, die es schwierig machen, die Konsistenz von Serienteilen zu gewährleisten.
Zeitaufwendige Einstellungen
Eine Charge von 1.000 Stück Lagergehäuse Verarbeitung Fall zeigt, dass die traditionelle Drehmaschine Umstellung muss die Reitstock-Position (zeitaufwendig 25 Minuten), Nachladen Vorrichtungen (15 Minuten), Test-Schneiden Kalibrierung (30 Minuten), die Vorbereitung Zeit entfielen die gesamten Mann-Stunden von 28%. Im Gegensatz dazu kann die CNC-Ausrüstung durch das Programm aufgerufen werden, um die gesamte Palette von Parametern in 8 Minuten zu wechseln, die Hervorhebung der Effizienz Engpass der manuellen Modus der High-Volume-Produktion.
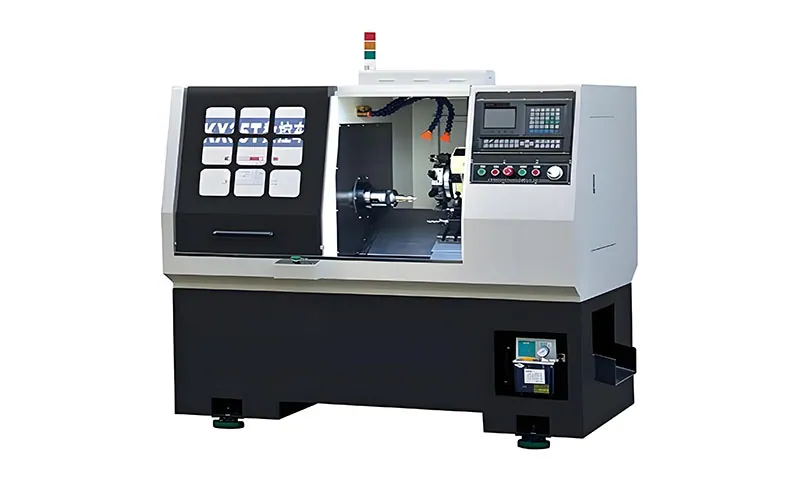
Moderne CNC-Drehmaschine
Als Kernstück eines intelligenten Fertigungssystems definiert die moderne CNC-Drehmaschine die Grenzen der Präzisionsfertigung durch die tiefgreifende Integration von Digitaltechnik und Maschinenbau neu. Die technologische Entwicklung spiegelt sich nicht nur im Hardware-Upgrade wider, sondern auch in der bahnbrechenden Entwicklung des intelligenten Steuerungssystems.
Kontrollsystem
Moderne CNC-Drehmaschinen sind mit einem digitalen Steuersystem ausgestattet, das als zentrales Nervensystem der Anlage fungiert und den koordinierten Betrieb der Spindel, der Vorschubachsen und der Hilfsgeräte in Echtzeit über einen Hochgeschwindigkeits-Datenbus koordiniert. Das eingebaute Fehlerkompensationsmodul ist in der Lage, den mechanischen Übertragungsspalt und die thermische Verformung, die durch eine geringe Abweichung verursacht werden, automatisch zu korrigieren; mit dem geschlossenen Rückkopplungsmechanismus der Waage wird die Positioniergenauigkeit im Mikrometerbereich stabilisiert. Diese digitale Steuerungslogik ändert die Arbeitsweise der traditionellen Bearbeitung, die auf manueller Erfahrung beruht, vollständig und ermöglicht es, die Konturgenauigkeit komplexer Oberflächen auf das Niveau von 1/10 des Durchmessers einer Haarsträhne zu bringen.
Benutzerfreundliche Programmierschnittstelle
Die intelligente Mensch-Maschine-Schnittstelle revolutioniert die Erstellung von Bearbeitungsprogrammen mit einem 3D-Simulationsmodul, das Werkzeugwege und Materialabtragsprozesse visualisiert. Der Bediener kann über die Drag-and-Drop-Programmierfunktion schnell G-Code erzeugen, und das System optimiert automatisch die Kombination von Schnittparametern und erkennt sogar die Merkmale der Zeichnung, um Bearbeitungsstrategien zu empfehlen. Die Verschmelzung von Touchscreen und Sprachsteuerung verbessert die Debugging-Effizienz der Anlage 60% und reduziert die Schwelle, sich auf Programmierkenntnisse zu verlassen, erheblich.
Adaptive Kontrollalgorithmen
Der intelligente Kern der Maschine passt die Vorschubgeschwindigkeit und die Spindellast dynamisch über ein Multisensornetzwerk an, das Echtzeitdaten zu Schnittkräften, Schwingungsspektren und Temperaturänderungen erfasst. Bei der Bearbeitung von Titanbauteilen für die Luft- und Raumfahrt identifiziert der Algorithmus harte Stellen im Material und reduziert automatisch die Schnitttiefe, um Werkzeugausbrüche zu vermeiden. Dank dieser Selbstoptimierungsfunktion kann die Maschine während der kontinuierlichen Bearbeitung ihre Spitzenleistung beibehalten und die Werkzeugstandzeit um mehr als 30% verlängern, während gleichzeitig eine stabile Oberflächenrauheit von Ra0,8μm oder weniger garantiert wird.
Erweiterte Verarbeitungsmöglichkeiten
Die 5-Achsen-Verkettungstechnologie durchbricht die Begrenzung der Bewegungsdimensionen traditioneller Werkzeugmaschinen und realisiert die Komplettbearbeitung komplexer Teile wie Turbinenschaufeln durch die Synergie des B-Achsen-Pendelkopfs und des C-Achsen-Rundtischs. Die Konstruktion des Power-Revolvers mit integrierter Frässpindel ermöglicht die gleichzeitige Bearbeitung von Querbohrungen und Endbearbeitungen während des Drehens, wodurch sekundäre Spannfehler vermieden werden. Die Multitasking-Fähigkeit ermöglicht es, Prozesse, für die sonst 3 Maschinen erforderlich wären, auf eine einzige Maschine zu konzentrieren, wodurch die Produktionszykluszeit um 40% verkürzt wird.
Integrierte Automatisierungstechnik
Das modulare automatische Werkzeugwechselsystem ist mit einem 40-Stationen-Werkzeugmagazin ausgestattet, das den Werkzeugwechsel in 0,8 Sekunden abschließen und die Werkzeugparameter über RFID-Chips automatisch überprüfen kann. Das intelligente Kühlsystem passt den Sprühwinkel und die Durchflussmenge der Schneidflüssigkeit an die Eigenschaften des zu bearbeitenden Materials an, und die Mikroschmierungstechnologie wird eingesetzt, um den Kühlmittelverbrauch bei der Bearbeitung von Aluminiumlegierungen um 85% zu reduzieren. Der eingebaute Werkstückmesstaster misst die Hauptabmessungen automatisch während des Bearbeitungsspalts, und die Echtzeit-Rückmeldedaten werden an das Steuersystem zurückgegeben, um kompensatorische Korrekturen vorzunehmen, wodurch ein vollständiges Closed-Loop-Management der Qualität entsteht.
Manuelle Drehmaschine vs. CNC-Drehmaschine Kernvergleich
Vergleichsmaßstab | handgefertigte Drechselbank | CNC-Drehmaschine |
---|---|---|
Präzision bei der Bearbeitung | ±0,05~0,1mm (abhängig von den Fähigkeiten des Bedieners) | ±0,005~0,01mm (Skala im geschlossenen Regelkreis) |
Produktionseffizienz | Hoher Zeitaufwand pro Stück (z.B. 30 Minuten für die Bearbeitung von abgesetzten Wellen) | Schnelle Serienproduktion (Bearbeitung desselben Teils in 5 Minuten) |
Betriebskomplexität | Qualifizierte Techniker erforderlich (3+ Jahre Erfahrung) | Programmiert, um automatisch zu laufen (1 Woche Schulung in der Grundbedienung, um die Arbeit aufzunehmen) |
Anfängliche Kosten | ¥30.000~100.000 (Einstiegsgerät) | ¥200.000~2 Millionen (5-Achsen-Modell) |
Flexible Produktionskapazität | Geeignet für Einzelstücke/Kleinserien (die Umstellung dauert 1~2 Stunden) | Unterstützt große Mengen/komplexe Teile (Umrüstvorgang dauert nur 5 Minuten) |
typische Anwendung | Formenwartung, Lehrpraktikum, handwerkliche Produktion | Luft- und Raumfahrtteile, Automobilteile, medizinische Geräte |
Energieverbrauchsquote | Durchschnittlicher Stromverbrauch 3~5kW-h (kein Standby-Verlust) | Durchschnittliche Leistungsaufnahme 10~30kW-h (einschließlich Kühlung/Werkzeugwechselsystem) |
Wartungskosten | Jährliche Wartungskosten ¥0,5~10.000 (mechanische Teile sind leicht zu ersetzen) | Jährliche Wartungsgebühr ¥30.000~100.000 (erfordert professionelle Ingenieure zur Wartung) |
Eingehende Analyse der Vor- und Nachteile
Vorteile der manuellen Drehbänke
- Flexible Produktion zu niedrigen Kosten
- Geeignet für Existenzgründer: 1/10 der Anschaffungskosten für CNC-Maschinen
- Schnelle Reaktion auf Änderungen: keine Programmierung zur Anpassung der Werkzeugwege erforderlich (z. B. Bearbeitung von Formteilen aus Bronze)
- Technischer Wert des Erbes
- Entwicklung eines mechanischen Gespürs: Der Bediener kann sich die Schnittkräfte und die Materialeigenschaften vorstellen.
- Statistik einer technischen Schule in Ningbo: Die praktische Ausbildung an einer manuellen Drehmaschine ermöglicht es den Schülern, die Genauigkeit der Werkzeugauswahl zu verbessern 40%
Vorteile der CNC-Drehmaschine
- Fähigkeit zur Bearbeitung komplexer Teile
- 5-Achsen-Kopplung: Turbinenschaufeln können bearbeitet werden (Oberflächengenauigkeit ±0,005 mm)
- Mill-Turn: Gleichzeitiges Bohren/Gewindeschneiden (z.B. Einsparung von 3 Prozessen bei der Bearbeitung von Automobil-Achsschenkeln).
- Garantie der Produktionskonsistenz
- Maßschwankungen <0,01 mm bei einer Serienfertigung von 2000 Stück.
- Daten aus einer Fabrik für medizinische Geräte:Bearbeitung mit numerischer SteuerungDurchgangsrate für Knochennagelgewinde 99,7%, nur manuell 82%
Vorschläge für die Auswahl
Anforderungs-Szenarien | Empfohlene Ausrüstung | Begründung |
---|---|---|
Lehre/Prototyping (begrenztes Budget) | handgefertigte Drechselbank | Kostengünstiges Ausprobieren zum Aufbau grundlegender Fähigkeiten |
Kleinserie mit vielen Sorten (<100 Stück) | Wirtschaftliche CNC-Drehmaschine | Geringere Kosten pro Einheit durch Wiederverwendung von Prozessen |
Große Mengen von Präzisionsteilen (>1000 Stück) | Hochwertige CNC-Drehmaschine | Automatisierte Produktion + Rückverfolgbarkeit der Qualität, umfassende Kostensenkung des 40% |
Ultrakomplexe Teile (z. B. Luft- und Raumfahrtteile) | 5-Achsen-Dreh- und Fräszentrum | Mehrseitenbearbeitung in einer Aufspannung, Vermeidung von Nullpunktfehlern. |
Vielfältige Anwendungsszenarien für CNC-Drehmaschinen
Als Kernstück der modernen Fertigungsindustrie ist die CNC-Drehmaschine dank ihrer hohen Präzision und großen Flexibilität in verschiedene Schlüsselbereiche der industriellen Produktion vorgedrungen. Von Präzisionsteilen im Mikrometerbereich bis hin zur Bearbeitung großer und komplexer Komponenten - die technologischen Vorteile der CNC-Drehmaschine verändern die globale Fertigungslandschaft.
Herstellung von komplexen geometrischen Teilen
In der Luft-und Raumfahrt, Fünf-Achsen-Gestänge CNC-Drehmaschine kann einmal die Turbinenschaufel (wie Abbildung 1) des Blattes Wurzel Nut und Feder und Luftfilm Kühlung Loch Verarbeitung, den traditionellen Prozess der 12 Prozesse auf 3, Blatt Konturgenauigkeit von ± 0,005 mm reduziert. ein Modell der Flugzeugtriebwerk Hochdruck Druck druckbeaufschlagten Scheibe Bearbeitung Fall zeigt, dass die Verwendung von Fräsen und Drehen Composite-Technologie, die Produktion Zyklus von 72 Stunden auf 18 Stunden komprimiert, und der Rundlauf Der Fehler wird innerhalb von 5μm kontrolliert.
Präzisionsformenbau
Ningbo, Unterprovinzstadt in ZhejiangDruckgussformIm industriellen Cluster übernehmen CNC-Drehmaschinen die Aufgabe der Präzisionsbearbeitung von wichtigen Formkernen. Bei der Bearbeitung von Formen für die Motorhaube von Fahrzeugen mit neuer Energie erhöht das Mehrwinkel-Tieflochdrehen (mit einem Verhältnis von Tiefe zu Durchmesser von 15:1) durch das Heißkanalsystem die Lebensdauer der Form auf 500.000 Formzyklen. Das Modul für die Präzisionsgewindebearbeitung kann eine Mikrosteigung von 0,2 mm erzeugen, um die Anforderungen an das Gießen von Mikrosteckern zu erfüllen.
Massenproduktion von Automobilteilen
- MotorsystemSchrittweises Drehen von Kurbelwellenzapfen mit Rundheitsfehler ≤ 0,003mm
- ÜbertragungssystemHartdrehen von Zahnradrohlingen für Getriebe (HRC60) als Alternative zu herkömmlichen Schleifverfahren
- Elektrifizierte KomponentenDynamisches Hochgeschwindigkeitsauswuchten von Motorrotoren mit einer Amplitude <0,01 mm bei 8000 U/min.
4. die Herstellung von Medizinprodukten
Beim Drehen von Titanlegierungen für künstliche Gelenke wird die Technologie der Mikroschmierung mit einer Oberflächenrauhigkeit von Ra0,2μm eingesetzt, um die Anforderungen der Implantation zu erfüllen. Bei der Bearbeitung von Mikrogewinden für orthopädische Schrauben (M0,6×0,125) wird durch die Indexierung der C-Achse eine Positioniergenauigkeit von 0,01° erreicht, was einen zuverlässigen Gewindeeingriff gewährleistet.
5. die Verarbeitung von Energieanlagen
Die Bearbeitung der Hochtemperaturlegierung Inconel 718 für das Laufrad der Hauptpumpe eines Kernkraftwerks verlängert die Werkzeugstandzeit um 40%, indem die Schnittparameter durch adaptive Steuerungsalgorithmen dynamisch angepasst werden.Das intermittierende Drehen von Lagerringen für Windkraftanlagen nutzt eine schwingungsdämpfende Technologie, um die Bearbeitungseffizienz um das Dreifache zu steigern.
Vergleich der Anwendungsdaten der Industrie
Anwendungsbereiche | Typische Teile | Anforderungen an die Präzision | Umfang der Effizienzgewinne |
---|---|---|---|
Luft- und Raumfahrt | Turbinenschaufel | ±0,005 mm | 300% |
Automobilbau | Kurbelwellenzapfen | Rundheit 0,003mm | 150% |
medizinische Ausrüstung | künstliches Gelenk | Ra0,2μm | 200% |
Energietechnische Ausrüstung | Nukleares Laufrad | Kontur 0,01 mm | 250% |
Häufig gestellte Fragen und Antworten
Wie haben die CNC-Drehmaschinen den Sprung von der einfachen Bearbeitung zur komplexen Fertigung geschafft?
CNC-Drehmaschinen haben sich durch drei große technologische Revolutionen entwickelt:
- Phase der Mechatronik (1950-1970)::
- Automatisierte Bearbeitung von einfachen Wellenteilen durch Programmierung mit Lochstreifen (Genauigkeit ±0,1mm)
- Typischer Fall: GM setzt die erste CNC-Drehmaschine zur Bearbeitung von Getrieberädern ein und steigert damit die Effizienz um 200%.
- Digitale Kontrollphase (1980-2000)::
- Einführung der Mikroprozessortechnologie, Unterstützung von Bogeninterpolation und Mehrachsenkopplung (Genauigkeit ±0,02 mm)
- Durchbruch: 5-Achsen-Bearbeitung von Turbinenscheiben für Boeing 747-Triebwerke, Verkürzung der Produktionsvorlaufzeit von 30 auf 7 Tage
- Phase der intelligenten Fertigung (2010 bis heute)::
- Integration von KI-Algorithmen und IoT-Technologien wie der Mazak iSMART Factory für die Steuerung auf 0,0001 mm Ebene
- Ein Druckgießereiunternehmen in Ningbo reduzierte die Anzahl der Formversuche durch die digitale Zwillingstechnologie von 15 auf 3
Wie lassen sich Effizienz und Umweltschutz bei CNC-Drehmaschinen in Einklang bringen?
- Technologie zur Verbesserung der Effizienz::
- Automatisches Werkzeugwechselsystem (Werkzeugwechselzeit ≤ 0,8 Sekunden) erhöht die Effizienz der Stapelverarbeitung um 60%
- Die Hochgeschwindigkeits-Zerspanungstechnologie (30.000 U/min Spindeldrehzahl) verkürzt die Bearbeitungszeit von Aluminiumlegierungen um 40%
- Nachhaltige Innovation::
- Mikromengen-Schmiersystem (MQL) zur Reduzierung des Einsatzes von 90%-Schneidflüssigkeit, jährliche Kosteneinsparungen von ¥ 150.000 pro Einheit
- Das Energierückgewinnungsmodul wandelt die Bremsenergie in wiederverwendbare elektrische Energie um und reduziert so den Stromverbrauch um 25%
- Eine Fabrik für neue Energie-Autoteile optimierte die Materialanordnung durch CNC, die Materialauslastung stieg von 68% auf 92%.
Können moderne CNC-Drehmaschinen sowohl einfache als auch komplexe Teile bearbeiten?
- Bearbeitung einfacher Teile::
- Stabiler Ausstoß von 60 Stück pro Minute durch Makros für die Serienproduktion von Bolzen
- Der Fehler bei der Bearbeitung mit der Schrittachse wird auf ±0,005 mm kontrolliert, was 5 Mal genauer ist als bei herkömmlichen Drehmaschinen.
- Komplexe Teile - Durchbruch::
- 5-Achs-Dreh-Fräsbearbeitung von Flugzeugtriebwerksmagazinen mit 200 Merkmalen in einer Aufspannung.
- Bearbeitung von künstlichen Hüftgelenken im medizinischen Bereich mit einer sphärischen Genauigkeit von Ra0,1μm (entspricht dem Spiegeleffekt)
- Ein Unternehmen in Ningbo bearbeitet mit einer CNC-Drehmaschine 0,2 mm dünnwandige Schalen aus Aluminiumlegierungen mit einer Verformung von <0,03 mm.