주조와 가공: 최선의 선택은 어떻게 할까요?
发布时间:2025-07-15 分类:공개 정보 浏览量:717
제조업의 세계에서.캐스팅노래로 응답가공는 가장 기본적이고 널리 사용되는 두 가지 부품 성형 기술입니다. 특정 부품 요구 사항에 직면했을 때 이 두 가지 중에서 어떻게 정보에 입각한 선택을 할 수 있을까요? 이는 제품의 품질, 비용 및 리드 타임과 직접적인 관련이 있습니다. 이 기사에서는 주조와 가공의 핵심 원리, 장단점, 주요 차이점 및 적용 시나리오를 분석하여 정확한 결정을 내릴 수 있도록 도와드립니다.
캐스팅이란 무엇인가요?
주조는 오랜 전통을 자랑하는 제조 공정입니다.용융 금속(또는 합금)을 미리 준비된 캐비티(금형)에 붓기. 금속은 금형에서 냉각되고 응고되어 결국 금형 캐비티 모양의 단단한 부품을 형성합니다. 이렇게 만들어진 부품을 "주조"라고 합니다.
캐스팅은 어떻게 진행되나요?
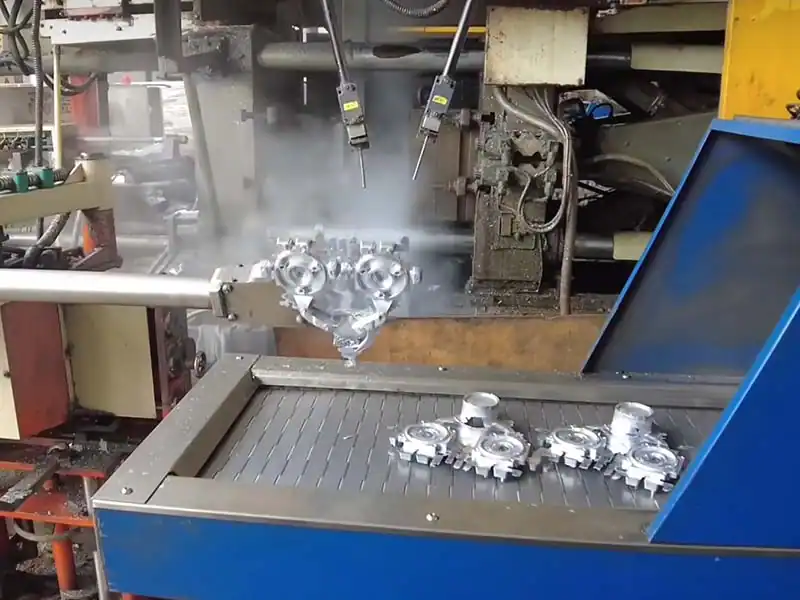
알루미늄 주조고압 다이 캐스팅자녀 출산
캐스팅 프로세스는 몇 가지 주요 단계로 구성됩니다:
- 금형 제조: 부품 도면에 따라 목재, 금속 또는 기타 재료로 부품의 모양에 해당하는 금형(모델)을 제작합니다. 캐비티 부품의 경우 내부 캐비티를 형성하는 코어도 만들어야 합니다.
- 스타일링: 금형을 모래 상자에 넣고 금형 주위에 모래(또는 기타 성형 재료)를 단단히 채워 주조 캐비티를 형성합니다. 금형을 제거하면 캐비티의 모양이 원하는 부품의 음수 모양이 됩니다.
- 일배체형 및 준비: 코어(필요한 경우)를 하단 샌드 박스에 넣은 다음 상단과 하단 샌드 박스를 정확하게 결합하고 고정하여 타설할 전체 주물을 형성합니다.
- 녹이고 붓기: 금속 재료를 녹는점 이상으로 가열하여 액체 상태로 녹인 다음 용융된 금속을 주조 패턴에 부드럽게 붓는 주입 시스템입니다.
- 냉각 및 응고: 용융 금속은 주조 금형 내에서 냉각되어 액체에서 고체 상태로 서서히 변합니다.
- 모래 낙하 및 청소: 금속이 완전히 굳고 냉각된 후 모래 주형을 부수고(또는 금속 주형을 열어서) 주물을 꺼냅니다. 그런 다음 스프 루 제거, 플라잉 에지 버 연마, 모래 청소, 표면 처리 등과 같은 일련의 후처리 작업을 수행합니다.
캐스팅의 장점
- 모양 복잡도가 높습니다: 복잡한 캐비티, 곡면 및 형상 구조(예: 엔진 블록, 펌프 하우징, 인공물)가 있는 부품을 생산할 수 있습니다.
- 다양한 소재: 모든 종류의 금속 및 합금, 특히 가공하기 어려운 일부 재료에 적합합니다.
- 대형 부품 제조: 몇 그램에서 수백 톤에 이르는 대형 부품을 생산할 때 선호되는 방법입니다.
- 일괄 생산의 비용 효율성: 일반적으로 대량 생산 시 부품당 비용은 기계 가공보다 저렴합니다.
- 전반적인 기계적 특성이 우수합니다: 주조는 거의 등방성 속성을 얻을 수 있습니다.
- 그물 모양 또는 그물 모양에 가까운 모양을 만들 수 있습니다: 특정 정밀 주조 방법(예: 인베스트먼트 주조, 다이캐스팅)을 사용하면 치수가 정확하고 표면이 깨끗한 주물을 만들 수 있어 후속 가공의 필요성을 줄일 수 있습니다.
캐스팅의 단점
- 상대적으로 낮은 표면 품질과 정밀도: 일반 주조는 기계 가공에 비해 표면이 거칠고 일반적으로 치수 및 기하학적 정확도가 낮습니다(정밀 주조 제외).
- 내부 결함의 위험: 다공성, 수축, 구겨짐, 내포물, 균열 등과 같은 내부 결함이 존재하여 강도와 밀봉에 영향을 미칠 수 있습니다.
- 높은 금형 비용: 금속 주형(특히 다이캐스팅, 인베스트먼트 주조) 또는 복잡한 목재 주형의 제조는 비용이 더 많이 들고 대량 생산에 적합합니다.
- 생산 리드 타임이 길어집니다: 금형 제작 및 성형 공정은 특히 단일 부품이나 소량 배치의 경우 시간이 많이 소요됩니다.
- 재료 제한: 특정 고융점, 내화성 금속 또는 합금은 주조하기 어렵습니다.
- 환경 영향: 용융 공정은 에너지 집약적이며 연기와 배기가스가 발생할 수 있고 폐모래 처리도 문제가 될 수 있습니다.
가공이란 무엇인가요?
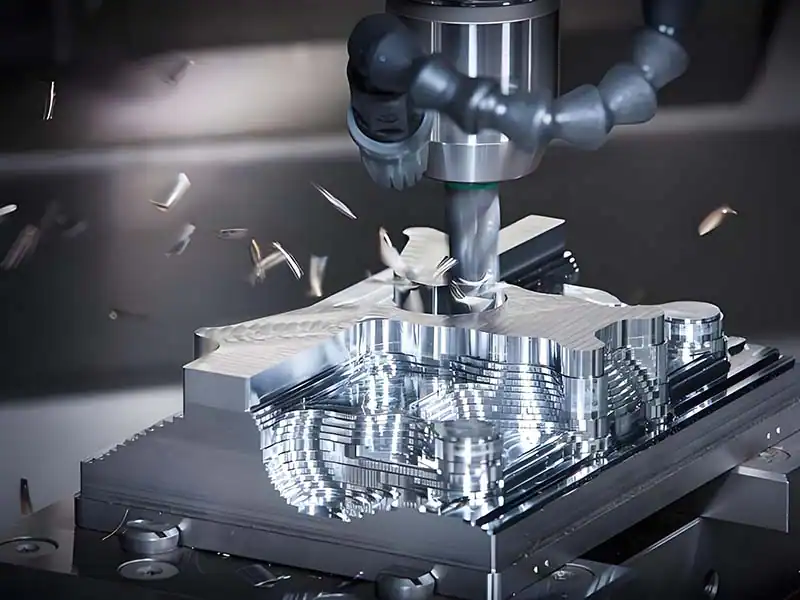
가공 생산
가공(또는 기계 가공, 절단)이란절삭 공구를 사용하여 기계적 힘으로 공작물 블랭크(예: 봉재, 단조품, 주조품)에서 여분의 재료를 점진적으로 제거합니다.디자인에 필요한 기하학적 모양, 치수 정확도 및 표면 품질을 얻기 위한 가공 방법입니다. 일반적인 장비로는 선반, 밀링 머신, 드릴링 머신, 연삭기, 머시닝 센터 등이 있습니다.
가공의 장점
- 높은 표면 품질로 높은 정밀도를 제공합니다: 매우 높은 치수 및 기하학적 정확도와 우수한 표면 마감을 얻을 수 있습니다.
- 디자인 유연성: 프로그래밍(CNC)을 사용하면 설계 변경과 복잡한 표면 및 정밀 피처의 가공에 빠르게 적응할 수 있습니다.
- 폭넓은 소재 적용성: 모든 종류의 금속, 플라스틱 및 복합 소재를 가공할 수 있습니다.
- 일관성과 반복성이 좋습니다: 특히 CNC 가공은 대량의 부품에 대해 높은 수준의 일관성을 보장합니다.
- 부품의 우수한 기계적 특성: 절단 공정은 일반적으로 재료 매트릭스 속성을 크게 변경하지 않으며(연삭 제외), 작업 경화는 때때로 표면 경도를 향상시킵니다.
- 소량 생산의 유연성: 값비싼 툴링이 필요하지 않으므로 프로토타입 제작, 소량 생산 및 맞춤형 부품 제작에 특히 적합합니다.
가공의 단점
- 물질적 낭비가 많습니다: 많은 양의 재료를 제거하면 칩이 발생하고 재료 활용도가 상대적으로 낮아집니다.
- 복잡한 내부 캐비티와 벽이 얇은 대형 부품 가공이 어렵습니다: 공구 접근성이 제한적이고 폐쇄형 캐비티 가공이 어려우며 벽이 얇은 대형 부품은 변형이 발생하기 쉽습니다.
- 복잡성이 증가하면 생산 비용도 증가합니다: 모양이 복잡하고 정밀도가 높을수록 더 많은 가공 공정이 필요하고 시간이 오래 걸리며 비용도 높아집니다.
- 배치 생산 비용이 더 높을 수 있습니다: 대량 생산의 경우 시간당 인건비가 캐스팅보다 높을 수 있습니다.
- 잔여 스트레스가 발생할 수 있습니다: 절단 공정은 공작물의 표면과 표면 아래에 잔류 응력을 발생시켜 치수 안정성이나 피로 강도에 영향을 줄 수 있습니다.
- 도구 비용 및 마모: 공구는 소모품이며, 특히 단단한 재료를 가공할 때는 빨리 마모되고 비용도 무시할 수 없습니다.
가공 및 주조: 유형 및 기술
가공 유형
- 선회: 공작물이 회전하고 공구가 직선으로 이동합니다. 원통형, 원뿔형, 끝면, 나사산 등을 가공하는 데 사용됩니다.
- 밀링: 공구가 회전하고 공작물이 움직입니다. 평평한 표면, 홈, 기어, 복잡한 곡면 등을 가공하는 데 사용되며 매우 다재다능합니다.
- 드릴링: 회전 드릴 비트는 공작물에 구멍을 뚫습니다.
- 지루합니다: 공작물의 기존 구멍을 확대하거나 마감하여 정확도와 마감을 개선합니다.
- 연삭: 고속 회전 연삭 휠로 마감하여 매우 높은 정밀도와 마감 품질을 제공합니다.
- 특수 가공: 방전 가공(EDM), 레이저 절단, 워터젯 절단 등 초경질 재료나 복잡한 형상을 가공하는 데 사용됩니다.
캐스팅 유형
- 모래 주조: 모래를 몰딩 재료로 사용하는 가장 일반적이고 유연하며 비용이 가장 적게 드는 방법입니다. 정확도와 표면 품질은 평균 수준입니다.
- 다이 캐스팅: 용융 금속을 고속, 고압으로 정밀 금속 금형의 캐비티에 압입합니다. 정밀도와 표면 품질이 우수하고 복잡한 형상을 가진 대량의 중소형 얇은 벽 부품에 적합합니다.
- 투자 캐스팅: 금형은 용융 가능한 재료로 만들어지고 쉘은 다층 내화 재료로 만들어지며 금형은 녹은 후 부어집니다. 고정밀, 매끄러운 표면, 고온 합금에 적합한 복잡한 부품을 주조 할 수 있습니다.
- 금속 주조: 재사용 가능한 금속 주형 사용(중력 주조). 주물의 품질이 모래 주형보다 우수하고 생산 효율이 높습니다.
- 저전압/차동 캐스팅:: 저압 또는 압력 차이에서 응고, 주물의 고밀도화.
- 원심 주조: 액체 금속을 고속 회전 금형에 붓고 원심력에 의해 성형합니다. 튜브형 및 링형 부품에 사용됩니다.
가공과 주조의 주요 차이점
- 금형:
- 캐스팅: 반드시 금형(모래, 금속 등)을 사용하여 부품의 모양을 형성합니다. 금형 비용이 주요 선행 투자 비용입니다.
- 가공: 불필요한 부품의 모양에 맞는 특수 금형. 범용 고정 장치와 절삭 공구로 충분합니다. 초기 비용은 주로 장비와 프로그래밍에 사용됩니다.
- 정밀도와 정확성:
- 캐스팅: 일반 방법(예: 샌드 몰딩)은 정확도(밀리미터 단위의 공차)가 낮고 표면이 거칠어집니다. 정밀 주조(다이캐스팅, 몰딩)는 더 높은 정확도(0.1mm 공차)와 마감을 얻을 수 있지만 일반적으로 기계 가공보다 낮습니다.
- 가공: 최고의 정밀도표준 가공은 IT7-IT8 등급 정확도(0.01-0.05mm 공차)에 도달할 수 있습니다. 일반 가공은 IT7-IT8 수준의 정확도(0.01-0.05mm 수준 공차)에 도달할 수 있으며, 미세 연삭 등은 IT5 수준 이상(미크론 수준)에 도달할 수 있습니다. 표면 거칠기는 거울 효과에 도달할 수 있습니다.
- 소재 호환성:
- 캐스팅: 처리 가능우수한 이동성금속 합금. 특정 고융점, 내화성, 산화성 합금은 주조하기 어렵습니다. 플라스틱도 사출 성형이 가능합니다(주조와 유사).
- 가공: 매우 광범위한 적합한 재료이 기계는 공구가 충분히 단단하기만 하면 거의 모든 고체 재료(금속, 플라스틱, 목재, 복합재)를 가공할 수 있습니다. 초경질 재료(예: 카바이드, 세라믹)를 가공하는 것은 비효율적이고 비용이 많이 듭니다.
- 부품의 설계 복잡성 및 크기:
- 캐스팅: 매우 복잡한 제조 전문형상, 특히 복잡한 캐비티, 곡면 및 얇은 벽 구조가 있는 부품에 적합합니다. 제조에 가장 적합한 방법입니다.대형 부품(예: 공작 기계 베이스, 선박용 엔진 블록)교장너무 많이고유방법.
- 가공: (기계의) 작업복잡한 내부 구멍과 깊은 구멍은 매우 어렵습니다.(도구 길이, 직경 및 접근성에 따라 제한됨).벽이 얇은 대형 부품은 변형되기 쉽습니다.. 외부 기하학적 특징 또는 상대적으로 개방된 내부 특징을 처리하는 데 더 적합합니다.
- 생산량과 속도:
- 캐스팅: 매우 빠른 대량 생산(특히 다이캐스팅) 개별 부품에 대한 사이클 타임이 짧습니다.소량 생산 시 느리고 비경제적임(높은 금형 비용 분담).
- 가공: 유연하고 빠른 소량 생산(금형 없음).상대적으로 느린 대량 생산단일 부품 가공 시간이 길어집니다. 다축 CNC 및 자동화된 생산 라인은 효율성을 향상시킬 수 있습니다.
- 부품 강도:
- 캐스팅: 주물에는 다공성, 수축 등과 같은 결함이 있을 수 있으며, 이는 응력 집중 지점으로서 피로 강도를 감소시킵니다. 입자 구조가 단조품만큼 조밀하지 않습니다. 그러나 무결성은 좋습니다.
- 가공: 일반적으로 밀도가 높고 섬유가 연속적인 소재와 기계적 특성(특히 강도, 인성, 피로 강도)을 갖춘 압연 및 단조 빌릿이 사용됩니다.일반적으로 캐스팅보다 낫습니다.. 그러나 절단하면 섬유 흐름선이 절단될 수 있습니다.
- 프로토타입 제작에 적합합니다:
- 캐스팅: 프로토타이핑높은 비용과 긴 리드 타임3D 프린팅 모래/용융 주형과 같은 쾌속 주조 기술을 사용하지 않는 한(금형을 먼저 만들어야 함). 일체형 프로토타입 제작에는 적합하지 않습니다.
- 가공: 프로토타입 제작에 적합. 금형이 필요하지 않으며 프로그래밍을 통해 디자인을 실제 개체로 빠르게 변환하여 반복적인 디자인 검증을 용이하게 할 수 있습니다.
- 생산 비용:
- 캐스팅: 높은 초기 툴링 비용 + 낮은 한계 비용. 대량 생산 시단위당 최저 비용. 소량으로 개당 비용이 매우 높습니다.
- 가공: 낮은 초기 비용(금형 없음) + 높은 한계 비용(인건비, 도구). 소량 생산좋은 경제. 대량으로 제작할 경우 개당 비용이 캐스팅보다 높을 수 있습니다.
- *요점: 비용 손익분기점. 일반적으로 "경제적 생산 로트" 임계값이 있습니다. 이 점 이하에서는 기계 가공이 더 경제적이며, 이 점 이상에서는 주조가 더 경제적입니다. 이 점은 부품의 복잡성, 재료, 정확도 요구 사항에 따라 크게 달라집니다.
주조 및 가공 적용 분야
- 캐스팅: 자동차 엔진 블록/실린더 헤드/변속기 하우징, 펌프 및 밸브 하우징, 터빈 블레이드(용융 금형), 대형 장비 베이스/프레임, 파이프 피팅, 아트웍, 조리기구, 항공우주 구조 부품.
- 가공: 정밀 기어, 샤프트 부품, 금형, 정밀 기기 부품, 광학 장치 베이스, 유압 밸브 블록, 커넥터, 지그 및 픽스처, 고정밀 결합 표면이 필요한 부품, 모든 유형의 부품에 대한 마감 공정.
어느 것을 선택해야 하나요? 가공 또는 주조?
만능 정답은 없습니다. 의사 결정에는 다음과 같은 핵심 요소에 대한 종합적인 평가가 필요합니다:
- 생산량:
- 아주 작은 배치(1~10개): 거의 항상 가공을 선택합니다.. 높은 금형 비용을 피하세요.
- 중소규모 배치(수십~수백 개): 기계 가공이 더 경제적인 경우가 많습니다.. 금형 비용을 배분하면 총 가공 비용보다 여전히 높을 수 있습니다.
- 대량(수천 개): 주조(특히 다이캐스팅)는 일반적으로 가장 비용 효율적입니다.. 금형 비용이 크게 희석되어 개당 생산 비용이 가장 낮습니다.
- *주의: 복잡한 부품과 단순한 부품의 경제적인 배치 크기 임계값에는 큰 차이가 있습니다. 단순한 부품은 수백 개로 주조하는 것이 적합할 수 있지만 복잡한 부품은 수천 개 이상이 필요할 수 있습니다.
- 부품의 복잡성:
- 매우 복잡한 경우(특히 복잡한 구멍, 곡면, 얇은 벽이 있는 경우): 캐스팅이 선호됩니다.. 가공이 불가능하거나 비용이 매우 많이 들 수 있습니다.
- 비교적 단순합니다(샤프트, 디스크, 블록과 같은 외부 특징이 지배적임): 더 유연하고 효율적인 가공기억해야 할 가장 중요한 점은 소량 배치뿐만 아니라 소량 배치도 가능하다는 것입니다.
- 적당히 복잡합니다: 두 프로세스를 비교하려면 자세한 비용 분석이 필요합니다.
- 정확성과 반복성이 요구됩니다:
- 매우 높은 정밀도(미크론 수준)와 완벽한 표면이 필요합니다: 가공을 선택해야 합니다.(특히 연삭, 미세 밀링 및 선삭).
- 높은 정밀도와 좋은 표면이 필요합니다: 정밀 주조(다이캐스팅, 인베스트먼트 주조)는 다음과 같은 요구 사항을 충족할 수 있습니다.리비아 아랍 자마히리야가공이 더 쉽고 안정적으로 이루어집니다..
- 정확도 요구 사항은 평균입니다(허용 오차 > 0.2mm): 일반 주조(모래 성형)로 충분합니다.비용이 더 저렴합니다.
- 머티리얼 유형:
- 캐스팅에 적합한 우수한 재료 흐름(예알루미늄(아연 합금, 주철, 구리 합금): 캐스팅은 좋은 옵션입니다..
- 재료가 내화성이거나 쉽게 산화되거나 주조 특성이 좋지 않은 경우(예: 특정 티타늄 합금, 고융점 합금): 기계 가공이 더 적합할 수 있습니다..
- 비금속 재료(플라스틱, 복합재)의 가공이 필요합니다: 가공이 주요 옵션입니다.(플라스틱 몰딩은 주조와 유사합니다).
- 재료가 매우 비쌉니다: 캐스팅(그물 모양에 가까운 형태)은 재료 낭비를 줄일 수 있습니다.그러나 스크랩 비율을 고려해야 합니다;높은 가공 폐기물와 비슷하지만 수익률이 높습니다. 종합적인 계산이 필요합니다.
- 재료 낭비:
- 자료 활용도를 극대화하세요: 그물 모양에 가까운 캐스팅(예: 용융 금형, 정밀 모래 금형)은 낭비가 적습니다.
- 재료 비용이 매우 높습니다: 주조 스크랩(타설 라이저 포함)과 가공 스와프를 모두 고려해야 합니다. 두 공정의 순 자재 소비량과 스크랩 비율에 대한 자세한 설명이 필요합니다.
- 생산 속도(리드 타임):
- 프로토타입이나 소량의 배치가 긴급하게 필요한 경우: 더 빠른 가공 응답(금형 제작 주기 시간 없음).
- 대량으로 빠르게 시장에 출시할 수 있습니다: 금형이 제자리에 있으면 주조(특히 다이캐스팅)가 매우 빠릅니다.총 배송 주기는 더 짧아질 수 있습니다.
평결에 도달하기
주조와 기계 가공은 경쟁하는 핵심 제조 기술이 아니라 상호 보완적인 기술입니다. 주조는 '처음부터 다시 만드는' 마스터 몰더와 마찬가지로 특히 대량 생산에서 부품당 낮은 비용으로 복잡하고 큰 부품을 효율적으로 제조하는 데 탁월합니다. 반면에 기계 가공은 부품에 타의 추종을 불허하는 정밀도, 마감 및 디자인 자유도를 제공하는 '우수성'의 조각가이며 소량 및 프로토타입 생산에서 대체할 수 없는 기술입니다.
현명한 선택은 부품 요구 사항을 철저히 이해하는 것에서 시작됩니다: 생산 수량, 기하학적 복잡성, 정확도 요구 사항, 재료 특성, 비용 목표 및 리드 타임에 대한 심층 분석. 주조는 정확도 요구 사항이 덜 까다로운 복잡한 형상의 대량 생산에 경제적인 선택인 경우가 많습니다. 작은 로트 크기, 높은 정확도, 빈번한 설계 반복 또는 주조하기 어려운 재료의 경우 기계 가공이 더 유리합니다. 많은 실제 애플리케이션에서 이 두 가지(주조 블랭크 + 기계 가공 마감)를 결합하면 비용, 효율성 및 품질 간에 최상의 균형을 이루면서 이점을 극대화할 수 있습니다.
자주 묻는 질문(FAQ)
- Q: 주조와 가공을 결합할 수 있나요?
A: 매우 일반적이며 권장합니다! 대부분의 주조 부품은 최종 치수 정확도, 표면 마감 및 중요한 결합 표면(예: 드릴링 홀, 밀링 플랫, 터닝 나사산)을 달성하기 위해 가공됩니다. 주조는 그물 모양에 가까운 블랭크를 제공하고 기계 가공을 통해 마감을 완성합니다. 이 두 가지를 모두 활용하는 것이 표준 관행입니다. - Q: 3D 프린팅(적층 제조)이 주조와 가공을 대체할 수 있나요?
A: 단기적으로는 완전한 대체가 아니라 상호 보완이 이루어질 것입니다. 3D 프린팅은 소량, 매우 복잡한 맞춤형 프로토타입과 가공하기 어려운 재료로 만든 부품에 탁월한 성능을 발휘합니다. 그러나 주조 및 가공(적층 가공)은 대량 생산, 비용 효율성, 다양한 재료 선택, 부품(특히 금속)의 기계적 특성, 대형 부품 제조 측면에서 여전히 대체 불가능한 장점을 가지고 있습니다. 3D 프린팅은 주조용 금형이나 코어를 만드는 데에도 종종 사용됩니다(쾌속 주조). - Q: 작지만 매우 복잡한 부품의 경우 기계 가공 외에 다른 옵션이 있나요?
A: 예. 이 점을 고려하세요:- 래피드 캐스팅 기술: 3D 프린팅을 사용하여 모래 또는 인베스트먼트 주조용 왁스/레진 주형을 직접 제조하면 기존 주형 제작에 드는 시간과 비용을 절감하고 소량의 복잡한 부품에 적합한 주조를 할 수 있습니다.
- 금속 3D 프린팅: 금속 부품의 직접 프린팅은 기존 방식으로는 제조할 수 없는 매우 복잡한 구조(예: 팔로우온 냉각 채널)에 특히 적합합니다. 하지만 비용, 속도, 크기 및 재료 특성 측면에서 여전히 한계가 있습니다.
- Q: 어떤 공정이 더 강력한 부품을 생산하나요?
A: 일반적으로 단조 또는 압연 빌릿으로 가공된 부품은 더 강하고 밀도가 높습니다(특히 피로 강도의 경우). 주물에는 강도에 영향을 미치는 내부 결함(다공성, 수축)이 있을 수 있습니다. 그러나 특정 고성능 주조 공정(예: 등온 단조 + 정밀 주조)을 통해 고강도 부품을 만들 수도 있습니다. 이는 재료, 공정 및 품질 관리에 따라 달라집니다. - Q: 선택할 때 가장 중요한 요소는 무엇인가요?
A: 가장 중요한 단일 요소는 없지만, 일반적으로 '생산 로트 크기'와 '부품 기하학적 복잡성'이 비용 효율성을 위한 가장 중요한 출발점입니다. 다음은 정확도 요건과 자료입니다. 최종 결정을 내릴 때는 모든 관련 요소를 고려해야 합니다. 중요한 프로젝트의 경우 상세한 공정 비용 분석(DFM - 제조를 위한 설계)이 필수적입니다.