Quelle est la différence entre l'extrusion d'aluminium et le moulage sous pression d'aluminium ?
Temps de publication:2025-04-23 Trier par:Le blog Nombre de vues:1093
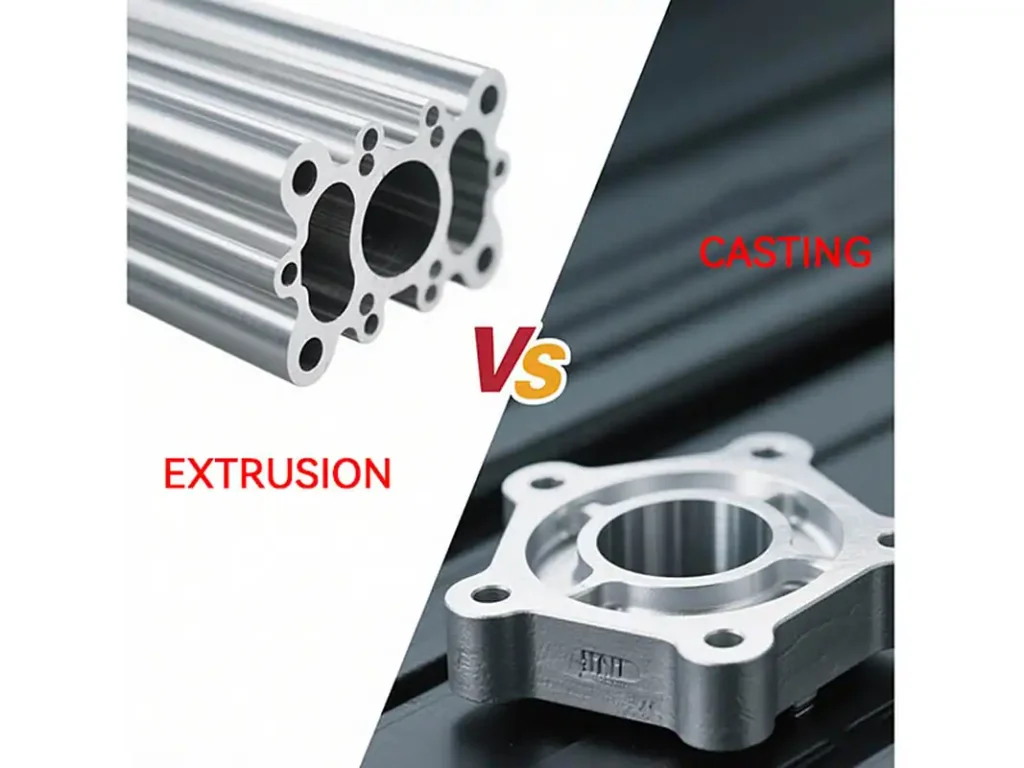
Dans le domaine de la fabrication industrielle, l'aluminium est devenu le matériau de choix dans les secteurs de l'automobile, de l'électronique et de la construction en raison de sa légèreté, de sa résistance à la corrosion et de sa grande solidité. Cependant, l'aluminium n'est pas un matériau à part entière.extrusion d'aluminium(Extrusion d'aluminium)avecMoulage sous pression de l'aluminium (moulage sous pression de l'aluminium)La différence fondamentale entre les deux processus affecte directement le coût de production, la précision structurelle et l'efficacité de la production de masse. En tant que domaine profondément enraciné du moulage sous pression de l'aluminium20 ansd'experts techniques.Ningbo Hexin Die Casting FactoryCet article analyse la logique technique des deux processus et explique comment réduire les coûts et accroître l'efficacité pour les clients grâce à la technologie du moulage sous pression de précision.
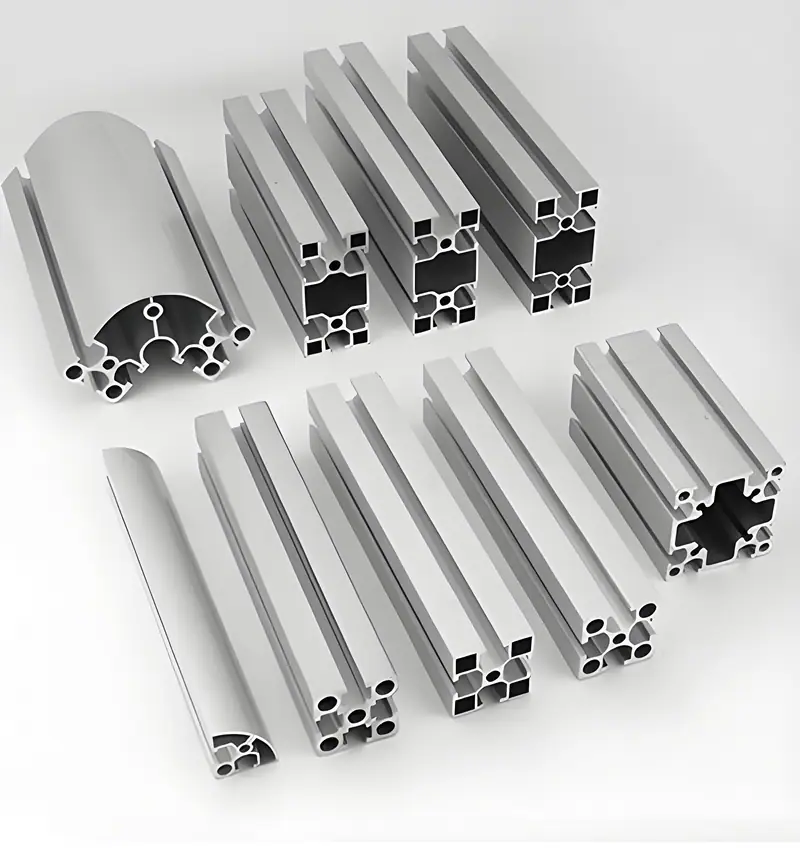
Comparaison de la nature du principe de moulage
(Différences fondamentales dans la manière dont les matériaux circulent)
Le processus d'extrusion de l'aluminium force les lingots chauffés à 400-500°C à travers des trous de filière spéciaux au moyen d'une pression hydraulique pouvant atteindre 15 000 tonnes, un processus de déformation plastique continue similaire au principe de "l'écrasement du dentifrice". Le métal est remodelé à l'état solide, tout en conservant la continuité de la structure originale du grain de l'aluminium. En revanche, le moulage sous pression de l'aluminium utilise un bouillon d'aluminium liquide à 680-720°C, injecté dans une cavité de moule en acier sous une pression élevée de 800-1200 bars à une vitesse de 30-100m/s, et solidifié par un refroidissement rapide (jusqu'à 1000°C/sec).
Cette différence d'état physique entraîne une différence fondamentale dans les performances du produit : les pièces extrudées ont des caractéristiques mécaniques anisotropes, le long de la direction de l'amélioration de la résistance à l'extrusion 20-30% ; le moulage sous pression est dû à une solidification rapide pour former une organisation cristalline fine, mais il y a un défaut de porosité de 3-5%. D'après la microstructure, les grains d'aluminium extrudés sont allongés pour former un tissu fibreux, et les pièces moulées sous pression présentent une structure maillée de phase eutectique interdendritique.
Duel de processus dans les systèmes d'équipement
(Comparaison de l'ensemble du processus, du four au produit fini)
L'équipement de base de la ligne d'extrusion consiste en un four de chauffage des barres longues, des cylindres d'extrusion, un système de contrôle de la température des filières et des dispositifs de transport, pour un investissement en équipement d'environ 2 à 5 millions de dollars. Les vitesses d'extrusion typiques sont de 5 à 50 m/min, avec une durée de vie des filières pouvant atteindre 50 à 100 tonnes de production. Le système de moulage sous pression, quant à lui, se compose d'un four de fusion, d'une unité d'éjection et d'un mécanisme de serrage. La force de serrage de la machine de moulage sous pression à chambre froide est comprise entre 800 et 5 000 tonnes, avec un coût d'équipement de 3 à 8 millions de dollars et une durée de vie de la filière d'environ 100 000 à 200 000 cycles de moulage.
En termes de consommation d'énergie, la consommation d'énergie pour l'extrusion d'une tonne d'aluminium est d'environ 500-800kWh, la principale consommation d'énergie étant concentrée dans le processus de déformation plastique ; la consommation d'énergie pour le moulage sous pression d'une tonne d'aluminium est de 800-1200kWh, dont 60% de consommation d'énergie pour la fusion du métal et le contrôle de la température de la matrice. Performance environnementale : le processus d'extrusion permet de recycler jusqu'à 951 tonnes de déchets, voire plus, tandis que le moulage sous pression, en raison de la quantité de soupe et du taux de rebut (environ 5-151 tonnes de déchets), produit davantage de déchets à renvoyer au four.
Analyse de l'application des caractéristiques des produits
(La logique du choix, des smartphones aux engins spatiaux)
Le processus d'extrusion permet de produire des composants linéaires avec une section transversale constante, une épaisseur de paroi typique de 1,5-25 mm, une rugosité de surface Ra0,8-3,2μm. Dans le domaine du mur-rideau architectural, les profilés extrudés en alliage 6063-T5 représentaient plus de 80% ; la longueur de l'ensemble du plancher extrudé des wagons de chemin de fer peut aller jusqu'à 26 mètres. Le moulage sous pression convient à la modélisation tridimensionnelle complexe, l'épaisseur minimale des parois pouvant atteindre 0,6 mm, la surface Ra1,6-6,3μm, le bloc moteur automobile couramment utilisé pour le moulage sous pression de l'A380, intégrant plus de 30 structures fonctionnelles en une seule.
En termes de propriétés mécaniques, l'état extrudé T6aluminiumLa résistance à la traction peut atteindre 350 MPa, ce qui convient aux pièces structurelles porteuses ; la résistance typique de l'alliage ADC12 coulé sous pression est de 280 MPa, ce qui permet de mettre davantage l'accent sur la complexité de la forme. La nouvelle technologie de moulage sous vide permet d'obtenir un allongement supérieur à 10%, ce qui modifie la perception traditionnelle de fragilité du moulage sous pression.
Le choix du procédé doit être envisagé de manière globale : pour une production mensuelle de 50 000 pièces, il est recommandé d'opter pour l'extrusion (le coût du moule ne dépasse pas 10 000 dollars), et pour une production en grande série pour le moulage sous pression (bien que le coût de l'outillage atteigne 50 000 à 200 000 dollars, le coût d'une seule pièce peut être réduit de 60%). Pour la nécessité d'anodiser la coque des produits électroniques, le choix prioritaire de l'alliage 6063 d'extrusion à faible teneur en impuretés ; et la coque de la transmission automobile, en raison de la conception complexe du canal d'huile, choisit inévitablement le processus de coulée sous pression. Avec la popularité de la technologie hybride, les pièces de carrosserie intégrées moulées sous pression déclenchent une révolution dans la fabrication automobile. La plaque inférieure arrière du modèle Y de Tesla utilise une machine de moulage sous pression de 6000 tonnes, soit 70 pièces intégrées en une seule.