Moulage ou usinage : comment faire le meilleur choix ?
Temps de publication:2025-07-15 Trier par:Le blog Nombre de vues:715
Dans le monde de la fabrication.couléerépondre en chantantusinagesont deux des technologies de formage de pièces les plus fondamentales et les plus utilisées. Comment faire un choix éclairé entre les deux lorsqu'on est confronté à une exigence spécifique en matière de pièces ? Ce choix est directement lié à la qualité, au coût et au délai de production du produit. Dans cet article, nous analyserons les principes fondamentaux, les avantages et les inconvénients, les principales différences et les scénarios d'application du moulage et de l'usinage afin de vous aider à prendre une décision précise.
Qu'est-ce que le casting ?
Le moulage est un procédé de fabrication ancestral qui repose sur l'utilisation de la matière première.Coulée de métal (ou d'alliage) en fusion dans des cavités (moules) préparées à l'avance.. Le métal est refroidi et solidifié dans le moule et finit par former une pièce solide ayant la forme de la cavité du moule. La pièce ainsi obtenue est appelée "coulée".
Comment fonctionne le casting ?
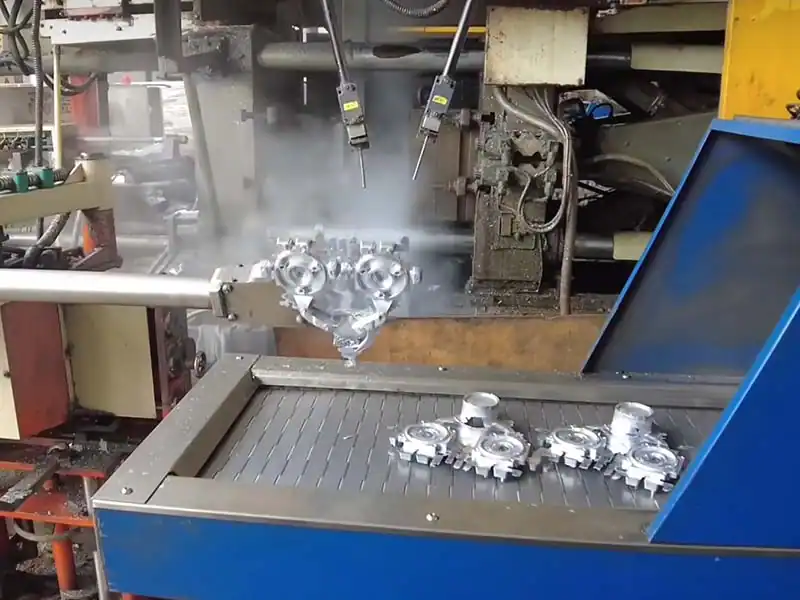
fonte d'aluminiumMoulage sous pressiondonner naissance à un enfant
Le processus de moulage se compose de plusieurs étapes clés :
- Fabrication de moules : Un moule (modèle) correspondant à la forme de la pièce est fabriqué en bois, en métal ou en d'autres matériaux selon le dessin de la pièce. Pour les pièces à cavité, il est également nécessaire de fabriquer le noyau qui forme la cavité intérieure.
- Stylisme : Le moule est placé dans un bac à sable et rempli hermétiquement de sable (ou d'un autre matériau de moulage) autour du moule pour former une cavité de coulée. Lorsque le moule est retiré, la forme de la cavité est la forme négative de la pièce souhaitée.
- Haplotype et préparation : Le noyau (si nécessaire) est placé dans le bac à sable inférieur, et les bacs à sable supérieur et inférieur sont ensuite rapprochés avec précision et fixés pour former la coulée complète à couler.
- Fondre et verser : Système de coulée qui chauffe un matériau métallique au-dessus de son point de fusion pour le faire fondre à l'état liquide et qui verse ensuite le métal fondu en douceur dans le modèle de coulée.
- Refroidissement et solidification : Le métal en fusion se refroidit dans le moule de coulée et passe progressivement de l'état liquide à l'état solide.
- Chute de sable et nettoyage : Une fois le métal complètement solidifié et refroidi, le moule en sable est cassé (ou le moule en métal est ouvert) et la pièce est retirée. Ensuite, une série de travaux de post-traitement tels que l'enlèvement de la carotte, le meulage de la bavure du bord volant, le nettoyage du sable, le traitement de surface, etc. sont effectués.
Avantages de la coulée
- Grande complexité des formes : Capable de produire des pièces présentant des cavités complexes, des surfaces incurvées et des structures façonnées (par exemple, des blocs moteurs, des logements de pompe, des objets d'art).
- Large gamme de matériaux : Convient à tous les types de métaux et d'alliages, en particulier à certains matériaux difficiles à usiner.
- Fabrication de grandes pièces : C'est la méthode privilégiée pour produire de grandes pièces pesant de quelques grammes à des centaines de tonnes.
- Rentabilité de la production par lots : Le coût par pièce est généralement inférieur à celui de l'usinage lorsqu'il s'agit de produire de grandes quantités.
- Bonnes propriétés mécaniques générales : Les pièces moulées peuvent avoir des propriétés presque isotropes.
- Il est possible d'obtenir une forme nette ou proche de la forme nette : Certaines méthodes de moulage de précision (par exemple, le moulage à la cire perdue, le moulage sous pression) permettent d'obtenir des pièces moulées aux dimensions précises et aux surfaces propres, ce qui réduit la nécessité d'un usinage ultérieur.
Inconvénients de la coulée
- Qualité de surface et précision relativement faibles : Par rapport à l'usinage, les moulages ordinaires présentent des surfaces plus rugueuses et une précision dimensionnelle et géométrique généralement inférieure (sauf pour les moulages de précision).
- Risque de défauts internes : Des défauts internes tels que la porosité, le retrait, le froissement, les inclusions, les fissures, etc. peuvent exister et affecter la résistance et l'étanchéité.
- Coûts élevés des moules : La fabrication de moules métalliques (en particulier le moulage sous pression, le moulage à la cire perdue) ou de moules complexes en bois est plus coûteuse et convient mieux à la production de masse.
- Délais de production plus longs : Les processus de fabrication et de façonnage des moules prennent beaucoup de temps, en particulier pour les pièces uniques ou les petits lots.
- Limitations matérielles : Certains métaux ou alliages réfractaires à point de fusion élevé sont difficiles à couler.
- Impact sur l'environnement : Le processus de fusion consomme beaucoup d'énergie et peut produire des fumées et des gaz d'échappement, et l'élimination des déchets de sable est également problématique.
Qu'est-ce que l'usinage ?
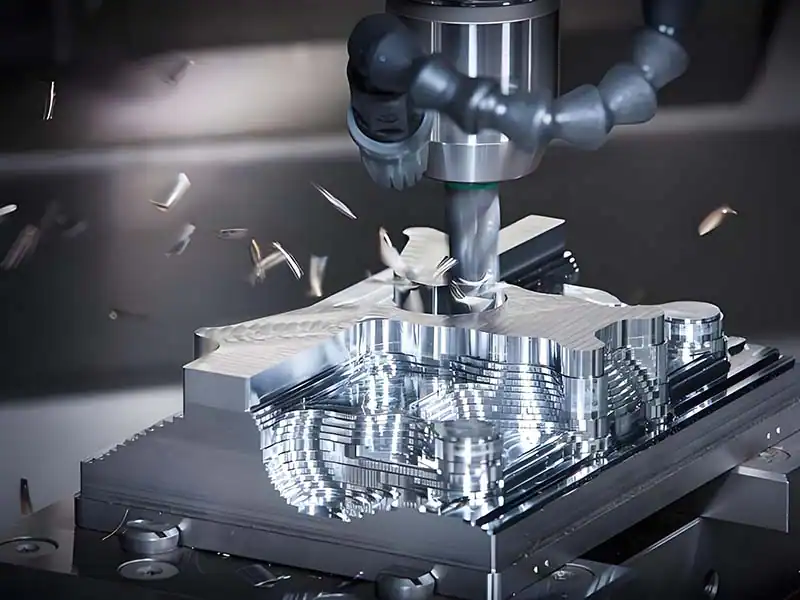
Production d'usinage
L'usinage (ou l'usinage, la coupe) est un type deEnlèvement progressif de l'excès de matière des pièces brutes (par exemple, barres, pièces forgées, pièces moulées) par une force mécanique à l'aide d'outils de coupe.Méthode d'usinage permettant d'obtenir la forme géométrique, la précision dimensionnelle et la qualité de surface requises par la conception. L'équipement courant comprend les tours, les fraiseuses, les perceuses, les rectifieuses, les centres d'usinage, etc.
Avantages de l'usinage
- Haute précision et haute qualité de surface : Il est possible d'obtenir une très grande précision dimensionnelle et géométrique ainsi qu'un excellent état de surface.
- Flexibilité de la conception : La programmation numérique (CNC) permet une adaptation rapide aux changements de conception et l'usinage de surfaces complexes et de caractéristiques de précision.
- Large applicabilité des matériaux : Il peut traiter toutes sortes de métaux, de plastiques et de matériaux composites.
- La cohérence et la répétabilité sont bonnes : L'usinage CNC, en particulier, garantit un degré élevé de cohérence pour de grandes quantités de pièces.
- Excellentes propriétés mécaniques des pièces : Le processus de coupe ne modifie généralement pas de manière significative les propriétés de la matrice du matériau (à l'exception de la rectification), et l'écrouissage améliore parfois la dureté de la surface.
- Flexibilité dans la production de petits lots : Aucun outil coûteux n'est nécessaire, ce qui le rend particulièrement adapté au prototypage, à la production de petits lots et aux pièces personnalisées.
Inconvénients de l'usinage
- Il y a beaucoup de déchets matériels : L'enlèvement d'une grande quantité de matière génère des copeaux et une utilisation relativement faible de la matière.
- Difficulté à usiner des cavités internes complexes et de grandes pièces à parois minces : Accessibilité limitée de l'outil, difficulté à usiner des cavités fermées ; les grandes pièces à parois minces sont sujettes à la déformation.
- Les coûts de production augmentent avec la complexité : Plus la forme est complexe et plus la précision requise est élevée, plus le nombre de processus d'usinage est important, plus le temps nécessaire est long et plus le coût est élevé.
- Les coûts de production par lots peuvent être plus élevés : Pour une production en grande quantité, le coût par heure de travail peut être plus élevé que pour le moulage.
- Des contraintes résiduelles peuvent être introduites : Le processus de coupe génère des contraintes résiduelles sur la surface et les sous-surfaces de la pièce, qui peuvent affecter la stabilité dimensionnelle ou la résistance à la fatigue.
- Coût et usure des outils : Les outils sont des consommables, surtout lorsqu'il s'agit d'usiner des matériaux durs. Ils s'usent rapidement et leur coût ne peut être ignoré.
Usinage et moulage : types et technologies
Types d'usinage
- Tournant : La pièce tourne et l'outil se déplace en ligne droite. Utilisé pour l'usinage de pièces cylindriques, coniques, de faces frontales, de filets, etc.
- Fraisage : L'outil tourne et la pièce se déplace. Il est utilisé pour l'usinage de surfaces planes, de rainures, d'engrenages, de surfaces courbes complexes, etc. et est extrêmement polyvalent.
- Forage : Le foret rotatif réalise des trous ronds dans la pièce à usiner.
- Ennuyeux : Agrandir ou finir les trous existants dans la pièce pour améliorer la précision et la finition.
- Broyage : Finition à l'aide de meules rotatives à grande vitesse pour une précision et une finition très élevées.
- Usinage de spécialités : Comme l'usinage par décharge électrique (EDM), la découpe au laser, la découpe au jet d'eau, etc., pour l'usinage de matériaux très durs ou de formes complexes.
Types de moulage
- Coulée en sable : La méthode la plus courante, la plus souple et la moins coûteuse, qui utilise le sable comme matériau de moulage. La précision et la qualité de la surface sont moyennes.
- Moulage sous pression : Le métal en fusion est pressé dans la cavité du moule métallique de précision à grande vitesse et à haute pression. Convient pour les pièces à paroi mince de grande quantité, de petite et moyenne taille et de forme complexe, avec une bonne précision et une bonne qualité de surface.
- Coulée à la cire perdue : Le moule est en matériau fusible, la coquille est en matériau réfractaire multicouche et le moule est coulé après la fusion. Haute précision, surface lisse, possibilité de couler des pièces complexes, convient aux alliages à haute température.
- Moulage de type métallique : Utilisation de moules métalliques réutilisables (coulée par gravité). La qualité des pièces moulées est supérieure à celle des moules en sable et l'efficacité de la production est élevée.
- Basse tension/moulage différentiel: : Solidification sous faible pression ou différence de pression, forte densification des pièces moulées.
- Coulée centrifuge : Le métal liquide est versé dans un moule tournant à grande vitesse et façonné par la force centrifuge. Utilisé pour les pièces tubulaires et en forme d'anneau.
Principales différences entre l'usinage et le moulage
- Moules :
- Casting : nécessairement Un moule (sable, métal, etc.) est utilisé pour former la forme de la pièce. Le coût du moule constitue le principal investissement initial.
- Usinage : inutile Un moule spécial correspondant à la forme de la pièce. Des montages universels et des outils de coupe suffisent. Les coûts initiaux sont principalement liés à l'équipement et à la programmation.
- Précision et exactitude :
- Casting : Les méthodes ordinaires (par exemple, le moulage au sable) sont moins précises (tolérances de l'ordre du millimètre) et les surfaces sont plus rugueuses. Le moulage de précision (moulage sous pression, moulage) permet d'obtenir une plus grande précision (tolérance de 0,1 mm) et une meilleure finition, mais reste généralement inférieur à l'usinage.
- Usinage : La plus grande précisionL'usinage standard peut atteindre une précision de niveau IT7-IT8 (tolérance de 0,01-0,05 mm). L'usinage conventionnel peut atteindre le niveau de précision IT7-IT8 (tolérance de 0,01-0,05 mm), la rectification fine, etc. peut atteindre le niveau IT5 ou même plus (niveau du micron). La rugosité de la surface peut atteindre l'effet miroir.
- Compatibilité des matériaux :
- Casting : capable de gérerbonne mobilitéles alliages métalliques. Certains alliages à point de fusion élevé, réfractaires et oxydants sont difficiles à couler. Les matières plastiques peuvent également être moulées par injection (comme le moulage).
- Usinage : Très large gamme de matériaux appropriésLa machine est capable d'usiner presque tous les matériaux solides (métaux, plastiques, bois, composites) à condition que l'outil soit suffisamment dur. L'usinage de matériaux très durs (carbure, céramique, etc.) est inefficace et coûteux.
- Complexité de la conception et taille de la pièce :
- Casting : Spécialisée dans la fabrication de produits extrêmement complexesLes pièces en acier inoxydable peuvent avoir des formes variées, en particulier des pièces comportant des cavités complexes, des surfaces incurvées et des structures à parois minces. C'est la meilleure façon de fabriquerGrandes pièces(par exemple, bases de machines-outils, blocs de moteurs marins)principalà tel point queuniqueMéthodes.
- Usinage : travail (de la machine)Les cavités internes complexes et les trous profonds sont très difficiles à réaliser.(limité par la longueur, le diamètre et l'accessibilité de l'outil).Les grandes pièces à parois minces sont sujettes à la déformation. Meilleur traitement des caractéristiques géométriques externes ou des caractéristiques internes relativement ouvertes.
- Volume et vitesse de production :
- Casting : Production de masse extrêmement rapide(en particulier le moulage sous pression) avec des temps de cycle courts pour les pièces individuelles.Lenteur et manque de rentabilité de la production en petites séries(partage des coûts des moules élevés).
- Usinage : Production flexible et rapide de petits lots(pas de moules).Une production de masse relativement lenteLe temps d'usinage d'une seule pièce est long. La CNC multi-axes et les lignes de production automatisées peuvent améliorer l'efficacité.
- La force de la pièce :
- Casting : La pièce coulée peut présenter des défauts tels que la porosité, le retrait, etc., qui réduisent la résistance à la fatigue en tant que point de concentration des contraintes. La structure du grain n'est pas aussi dense que celle des pièces forgées. Mais l'intégrité est bonne.
- Usinage : On utilise généralement des billettes laminées et forgées, dont le matériau est dense et contient des fibres, et dont les propriétés mécaniques (en particulier la résistance, la ténacité et la résistance à la fatigue) sont les suivantesGénéralement meilleurs que les pièces moulées. Cependant, le découpage peut couper la ligne d'écoulement des fibres.
- Convient pour le prototypage :
- Casting : PrototypageCoûts élevés et longs délais de mise en œuvre(il faut d'abord fabriquer des moules), à moins d'utiliser une technique de coulée rapide telle que des moules en sable ou en fonte imprimés en 3D. Ne convient pas au prototypage d'une seule pièce.
- Usinage : Idéal pour le prototypage. Aucun moule n'est nécessaire et la programmation permet de transformer rapidement les conceptions en objets physiques, ce qui facilite la validation itérative des conceptions.
- Coûts de production :
- Casting : Coût initial élevé de l'outillage + coût marginal plus faible. Dans la production de masseCoût le plus bas par unité. Coût par pièce très élevé pour les petites quantités.
- Usinage : Faible coût initial (pas de moules) + coût marginal plus élevé (heures de travail, outils). Production en petites sériesUne bonne économie. Le coût par pièce peut être plus élevé que celui du moulage pour les grandes quantités.
- *Point clé : le seuil de rentabilité. Il existe généralement un seuil de "lot de production économique". En dessous de ce seuil, l'usinage est plus économique ; au-dessus, le moulage est plus économique. Ce seuil dépend de la complexité de la pièce, du matériau, des exigences de précision qui varient considérablement.
Domaines d'application pour le moulage et l'usinage
- Casting : Blocs moteurs, culasses, boîtiers de transmission, boîtiers de pompes et de soupapes, aubes de turbines (moules de fusion), bases/cadres de grands équipements, raccords de tuyauterie, objets d'art, ustensiles de cuisine, composants structurels pour l'aérospatiale.
- Usinage : Engrenages de précision, pièces d'arbres, moules, pièces d'instruments de précision, bases d'appareils optiques, blocs de vannes hydrauliques, connecteurs, gabarits et montages, pièces nécessitant des surfaces d'accouplement de haute précision, et processus de finition pour tous types de pièces.
Lequel dois-je choisir ? L'usinage ou le moulage ?
Il n'existe pas de réponse unique. La prise de décision nécessite une évaluation complète des facteurs clés suivants :
- Volume de production :
- Très petits lots (1 - dizaines de pièces) : Choisir presque toujours l'usinage. Éviter les coûts élevés des moules.
- Petites et moyennes séries (dizaines - centaines de pièces) : Souvent plus économique à usiner. Le coût du moule peut encore être plus élevé que le coût total de l'usinage lorsqu'il est réparti.
- Grandes quantités (milliers de pièces) : Le moulage (en particulier le moulage sous pression) est souvent la solution la plus rentable.. Les coûts des moules sont fortement dilués et le coût de production par pièce est le plus bas.
- *Attention : Il existe une grande différence entre les seuils économiques de taille des lots pour les pièces complexes et les pièces simples. Les pièces simples peuvent être moulées en quelques centaines de pièces, tandis que les pièces complexes peuvent nécessiter plus de quelques milliers de pièces.
- Complexité des pièces :
- Très complexe (en particulier avec des cavités complexes, des surfaces incurvées, des parois minces) : Le moulage est préférable. L'usinage peut être impossible ou extrêmement coûteux.
- Relativement simple (dominée par des éléments externes tels que des arbres, des disques, des blocs) : L'usinage est plus souple et plus efficaceCeci est particulièrement vrai pour les petits lots.
- Moyennement complexe : Une analyse détaillée des coûts est nécessaire pour comparer les deux procédés.
- La précision et la répétabilité requises :
- Une très grande précision (de l'ordre du micron) et des surfaces parfaites sont requises : L'usinage doit être sélectionné(en particulier le broyage, le fraisage fin et le tournage).
- Une grande précision et une bonne surface sont requises : Le moulage de précision (moulage sous pression, moulage à la cire perdue) peut répondre aux exigences deJamahiriya arabe libyenneL'usinage est plus facile et plus fiable.
- Les exigences de précision sont moyennes (tolérance > 0,2 mm) : La coulée ordinaire (moulage au sable) est suffisanteLe coût est moins élevé.
- Type de matériau :
- Bon écoulement du matériau, adapté à la coulée (par ex.aluminium(alliage de zinc, fonte, alliage de cuivre) : La fonte est une bonne option.
- Le matériau est réfractaire, facilement oxydable ou présente de mauvaises propriétés de coulée (par exemple, certains alliages de titane, des alliages à point de fusion élevé) : L'usinage peut être plus facile à mettre en œuvre.
- Le traitement de matériaux non métalliques (plastiques, composites) est requis : L'usinage est la principale option(Le moulage plastique est similaire au coulage).
- Le matériel est très cher : Le moulage (forme proche du filet) peut réduire les déchets de matériaux.mais il faut tenir compte du taux de rebut ;Déchets d'usinage élevésmais avec un rendement élevé. Des calculs détaillés sont nécessaires.
- Déchets de matériaux :
- Chercher à maximiser l'utilisation des matériaux : moulage en forme de filet(par exemple, les moules à fusion, les moules à sable de précision) sont moins coûteux.
- Le coût des matériaux est extrêmement élevé : Il faut tenir compte à la fois des rebuts de coulée (y compris les rejets de coulée) et des copeaux d'usinage. Une comptabilité détaillée de la consommation nette de matériaux et des taux de rebut pour les deux processus est nécessaire.
- Vitesse de production (délai) :
- Des prototypes ou de petits lots sont nécessaires de toute urgence : Une réponse plus rapide à l'usinage(Pas de temps de cycle pour la fabrication des moules).
- Les grandes quantités sont rapidement mises sur le marché : Une fois les moules en place, le moulage (en particulier le moulage sous pression) est extrêmement rapide.Le cycle de livraison total peut être plus court.
rendre un verdict
Le moulage et l'usinage sont des technologies de fabrication complémentaires plutôt que concurrentes. La fonderie, comme le maître mouleur "à partir de zéro", excelle dans la fabrication efficace de pièces complexes et de grande taille à un faible coût par pièce, en particulier dans la production en grande série. L'usinage, quant à lui, est le sculpteur de l'"excellence", donnant aux pièces une précision, une finition et une liberté de conception inégalées, et est irremplaçable dans la production de faibles volumes et de prototypes.
Pour faire des choix judicieux, il faut d'abord bien comprendre les exigences des pièces : Analyses approfondies des quantités produites, de la complexité géométrique, des exigences de précision, des propriétés des matériaux, des objectifs de coûts et des délais. Le moulage est souvent le choix économique pour les volumes importants, les formes complexes et les exigences de précision moindres. L'usinage est plus avantageux pour les petits lots, la haute précision, les itérations de conception fréquentes ou les matériaux difficiles à mouler. Dans de nombreuses applications réelles, la combinaison des deux (ébauches moulées + finitions usinées) permet souvent de maximiser les avantages, en trouvant le meilleur équilibre entre le coût, l'efficacité et la qualité.
Foire aux questions (FAQ)
- Q : Puis-je combiner le moulage et l'usinage ?
R : Très courant et recommandé ! La grande majorité des pièces moulées sont usinées pour obtenir la précision dimensionnelle finale, l'état de surface et les surfaces d'accouplement critiques (par exemple, perçage de trous, fraisage de plats, tournage de filets). Le moulage fournit l'ébauche de forme presque nette et l'usinage complète la finition. Il s'agit d'une pratique courante qui permet de tirer parti des deux méthodes. - Q : L'impression 3D (fabrication additive) remplacera-t-elle le moulage et l'usinage ?
R : À court terme, il n'y aura pas de remplacement complet, mais plutôt une complémentarité. L'impression 3D excelle dans la fabrication de prototypes et de pièces personnalisées, extrêmement complexes et en petits volumes, à partir de matériaux difficiles à usiner. Toutefois, le moulage et l'usinage (matériaux soustractifs) conservent des avantages irremplaçables en termes de production en grande quantité, de rentabilité, de choix des matériaux, de propriétés mécaniques des pièces (en particulier des métaux) et de fabrication de pièces surdimensionnées. L'impression 3D est également souvent utilisée pour fabriquer des moules ou des noyaux pour le moulage (moulage rapide). - Q : Pour les pièces de petite taille mais très complexes, existe-t-il d'autres options que l'usinage ?
R : Oui. Considérez ceci :- Technologie de coulée rapide : L'utilisation de l'impression 3D pour fabriquer directement des moules en cire ou en résine pour le moulage en sable ou à la cire perdue élimine le temps et le coût de la fabrication traditionnelle des moules et rend le moulage adapté aux petites quantités de pièces complexes.
- Impression 3D de métaux : L'impression directe de pièces métalliques est particulièrement adaptée aux structures extrêmement complexes (par exemple, les canaux de refroidissement) qui ne peuvent pas être fabriquées par des méthodes conventionnelles. Toutefois, des limites subsistent en termes de coût, de vitesse, de taille et de propriétés des matériaux.
- Q : Quel procédé permet d'obtenir des pièces plus résistantes ?
R : En général, les pièces usinées à partir de billettes forgées ou laminées sont plus résistantes et plus denses (en particulier pour la résistance à la fatigue). Les pièces moulées peuvent présenter des défauts internes (porosité, retrait) qui affectent la résistance. Toutefois, certains procédés de moulage à haute performance (par exemple, forgeage isotherme + moulage de précision) peuvent également donner lieu à des pièces à haute résistance. Cela dépend du matériau, du procédé et du contrôle de qualité. - Q : Quels sont les facteurs les plus importants lors du choix ?
R : Il n'existe pas de facteur unique le plus important, mais la "taille du lot de production" et la "complexité géométrique de la pièce" sont généralement les points de départ les plus critiques en matière de rentabilité. Viennent ensuite les exigences de précision et les matériaux. Tous les facteurs pertinents doivent être pris en compte dans la décision finale. Pour les projets importants, une analyse détaillée du coût du processus (DFM - Design for Manufacturing) est essentielle.