低圧鋳造アルミホイールハブの亀裂発生原因と改善策
发布时间2025-01-27 分类広報 浏览量2662
低圧鋳造 機械化と自動化の高度を達成することができ、生産性を向上させる(10〜15型/時間)、それはまた、生産工程における多くの有害な人的要因を減らすことができ、完成品の割合を向上させ、大幅に労働者の労働強度を低減します。しかし、工程計画、工程パラメータ、金型構造、手動操作などの要因による低圧鋳物の品質は、リンクの任意の不合理な設計や不適切な操作は、低圧鋳物の欠陥につながる可能性があります。アルミホイールの亀裂の発生は、企業の生産コストと生産性に影響を与える重要な要因である。したがって、低圧鋳造アルミホイールのクラックの原因について議論することは特に重要です。次に、中国の低圧鋳造工場の鋳造について説明します。 アルミニウム 自動車ホイールのひび割れの発生とその対策。
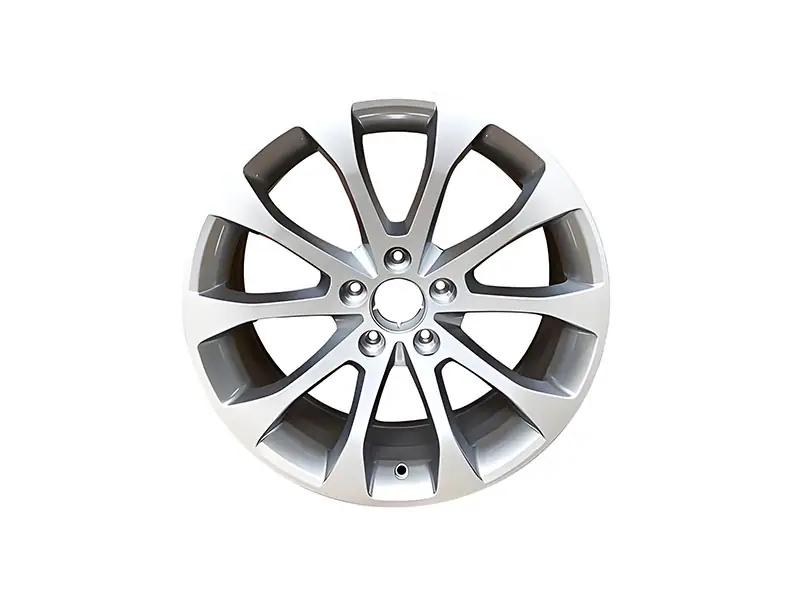
低圧鋳造ホイールとは何ですか?
低圧鋳造ホイールは、低圧鋳造技術によって製造され、高密度、高強度、良好な品質管理を実現します。低圧鋳造は、液状の合金を低圧で金型に注入し、冷却して凝固させます。低圧鋳造は、高密度、均質な構造、良好な強度と靭性を持つホイールを生産し、大量生産に適しています。
製造工程はいくつかのステップに分かれています。まず、液状の合金を金型に注入します。次に、合金を冷却して固化させます。最後に、熱処理、仕上げ、塗装の工程を経てホイールが完成します。この工程により、気泡や不純物が減少し、強度と精度が向上し、ホイールの安全性が高まります。
とともに重力鋳造低圧鋳造の方が効率的で、品質の良い製品ができる。重力鋳造は重力に頼って金属を流すため、分布が不均一になり、品質と安全性が損なわれます。低圧鋳造は圧力を加えることでアルミニウム合金の流れを制御し、ホイールの精度と強度を確保します。
その結果、低圧鋳造ホイールは自動車製造において、高い効率性、品質、安全性を提供し、ますます重要性を増している。
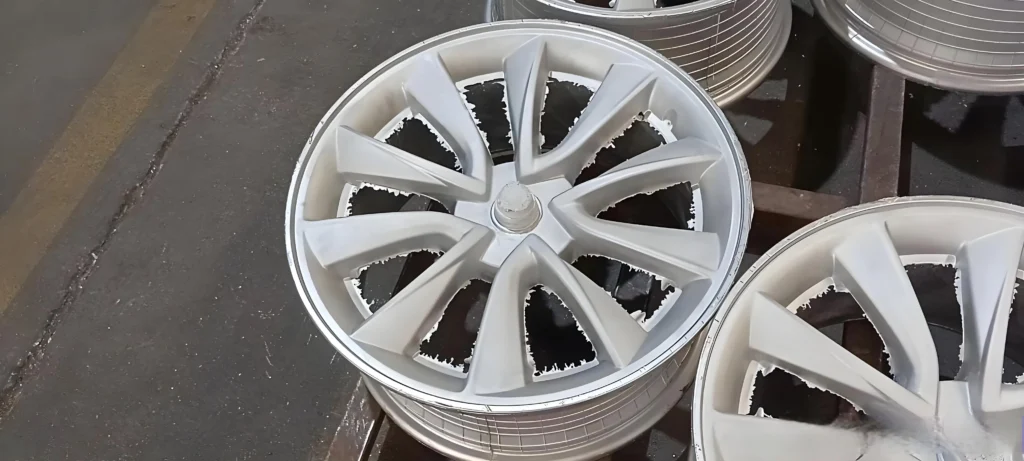
低圧鋳造ホイール技術の優位性と産業価値の改造
メカニカル・オートメーションが牽引する精密製造革命
低圧鋳造技術は、高度な機械化と自動化により、従来の重力鋳造の効率を約30%上回る、毎時10~15個の安定した生産能力を達成した。その核心原理は、低圧ガス(0.02~0.08MPa)を使用して、液体アルミニウム合金を金型キャビティにスムーズに押し込むことであり、重力鋳造で金属液体が自由に流動することによって発生する巻き上がりガスや酸化スラグの問題を回避することができる。クローズドループ金型温度制御システムとインテリジェント圧力センサーの組み合わせにより、鋳物粒子はミクロンレベルまで微細化され、ホイールハブの動的曲げ疲労寿命は100万サイクルを超え、ハイエンド車の軽量化と安全性の要求を完全に満たしました。これはハイエンドモデルの軽量化と安全性という2つの要求を完全に満たしている。
低圧鋳造ホイールの亀裂原因の学際的診断
亀裂形態と破壊メカニズムの深い相関性
アルミ合金ホイールの製造工程では、材料特性、構造設計、工程パラメータなど、複数の要因が絡み合って亀裂が発生することが多い。破壊力学的解析によると、ホイールのクラックは大きく3つのタイプに分けられる:
- 熱亀裂(凝固欠陥)熱割れは主にスポークとリムの接合部で発生し、粒界に沿って分布する網目状の割れとして現れる。その本質は、凝固末期の樹枝状骨格の間に残留する液体金属が収縮応力に耐えられないことにあり、典型的な事例では、局所冷却速度が4℃/秒を超えると、熱割れの発生確率が60%上昇する。
- コールドクラック(機械的応力)この破壊は一般的にハブフランジの付け根で見られ、破壊は典型的な脆性破壊特性を示す。商用車用ハブの故障解析から、脱型時にリフトチューブ内に残った凝固金属が鋳物に200MPa以上の引張応力を与え、これが貫通き裂の直接の引き金になったことがわかった。
- 応力腐食割れ(環境との相互作用)沿岸部の高湿度環境では、ハブ内の残留応力が塩化物イオンと相乗的に作用し、結晶粒界に沿ってゆっくりと亀裂が進展する。このようなクラックは、顕微鏡観察で特徴的な樹枝状の分岐形態を示す。
主要な破砕要因の体系的分析
1.構造設計上の欠陥の機械的増幅
- 鋭角部での応力集中ホイールスポークの移行領域におけるインナーフィレットの半径が3mm未満の場合、応力集中係数(Kt)は3.5~4.2に達する可能性があり、これはA356-T6アルミ合金の降伏強度(220MPa)をはるかに上回ります。スポーツホイールのシミュレーションデータによると、R角度を2mmから5mmに最適化した後、最大等価応力は315MPaから185MPaに減少した。
- 肉厚変異効果隣り合う部分の肉厚差が3:1を超えると、冷却過程で発生する熱応力勾配が材料の引張強さの限界を突破する可能性があります。軽量ホイールハブの破壊事例では、リムとスポークの接合部の肉厚が8mmから3mmに減少し、280MPaの局所応力ピークが発生した。
2.プロセス・パラメータの不一致によるシステミック・リスク
- 圧力を保持できる時間が短い保持時間が15秒未満では、収縮の中断と収縮ゆるみの形成につながり、40秒を超えると、上昇管内の金属の凝固に機械的抵抗が生じる。プロジェクトのDOEテストでは、保持時間を25~30秒の範囲に制御すると、割れ率が7.2%から0.8%に減少することが確認された。
- 充填率の不適切な管理充填速度が120mm/sを超えると、金属と液体の乱流ガスロールの発生確率が40%増加し、ガス滞留によって形成される微細欠陥が亀裂発生の起点となる。ステップアッププロセス(初期0.03MPa、最終0.06MPa)は、充填速度とガスロールのリスクのバランスを効果的にとることができる。
3.金型熱管理における動的平衡の課題
- 暴走温度勾配金型の温度差が50℃を超えると、鋳物の各領域の凝固収縮差率が0.8%を超え、熱亀裂を誘発する。ある工場は鋳型の温度を監視するポイントを移植して、スポーク部分の温度変動は±30℃まで、仕切り温度制御システムを設置した後、温度差は±5℃以内に安定していることを発見した。
- 冷却媒体の不適切な選択伝統的な水冷は、金型の表面温度の急激な低下を引き起こしやすいですが、エアロゾル混合冷却技術を使用すると、正確に3〜8℃/秒の冷却速度を制御することができ、急冷による応力の急冷を避けることができます。
ひび割れ防止のためのエンジニアリンググレードのソリューション
1.リフトシステムの力学のための最適化されたシステム
- ランナー形状の再構築リフトパイプの直径をΦ60mmからΦ85mmに拡大し、30°傾斜したランナー設計により、金属液の流速を0.8~1.0m/sに安定させた。あるプロジェクトの実践では、この移動によりリフトパイプの凍結確率が70%減少した。
- 断熱材のアップグレードナノマイクロポーラス保温スリーブ(熱伝導率≤0.1W/m・K)を採用し、従来のセラミックファイバー素材に比べて保温の限界時間を40%延長し、収縮路の平滑性を確保。
2.構造設計のためのバイオニック最適化経路
- ストレス・フロー・マッピング技術トポロジー最適化アルゴリズムに基づくスポーク材の再配分により、主応力方向と補強方向を一致させた。この技術により、軽量ホイールは12%の軽量化を達成し、曲げ剛性は18%向上した。
- 勾配遷移則肉厚変異部に1:4のテーパー移行部を設計し、スポーク根元に深さ1.5mmの応力除去溝を追加することで、局部応力ピークを295MPaから175MPaに低減することに成功した。
3.型の理性的な温度調整システムの革新
- マルチゾーン連成温度制御6ゾーン独立温度制御モジュールを開発し、リムゾーンは320℃(成形収縮を促進)、スポークゾーンは280℃(熱割れを抑制)に設定。高級ブランドホイールの量産では、このシステムにより金型温度の均一性が±3℃に達する。
- ダイナミック冷却戦略空冷は充填段階で金型温度を維持するために使用され、霧状冷却は保持段階で固化を促進するために切り替えられ、生産サイクル全体を8秒短縮する。
寧波禾欣のプロセス革新の実践
ドイツの高級ブランドとの協力関係において、何進のチームは3つの重要な技術的ブレークスルーを通じて業界のベンチマークを達成した:
- 低圧鋳造-スピニング複合成形技術リム部にスピニング加工を施し、砥粒が円周方向に沿うようにすることで、ホイールハブの半径方向の衝撃強度を35%向上。
- 勾配加熱システム(特許技術)金型の表面には0.2mm厚の窒化チタンコーティングが施され、誘導加熱装置とともに、スポーク部の温度差≤5℃の精密な温度制御を実現しています。
- デジタル・プロセス・シミュレーション・プラットフォームMAGMAsoftとANSYSシステムの統合により、金型の試作回数が12回から3回に短縮され、開発サイクルが60%短縮されました。
適切な低圧鋳造ホイールプラントの選択
質の高いサプライヤーが持つべき4つのコア・コンピテンシーがある:
- 材料データベース数万セットのプロセスパラメーターと合金特性のマッピング関係の蓄積、最適な材料ソリューションの迅速なマッチング
- 全工程の品質管理インゴットの純度分析(Fe含有量0.15%以下)からX線欠陥検出(ASTM E505規格)まで、12の品質管理ポイントを設定。
- フレキシブル生産16-24インチホイール対応のクイック・モールド・チェンジ・システム。
- グリーン・マニュファクチャリングアルミチップ回収率≥95%、製品1個当たりのエネルギー消費量は業界平均より28%低い。
よくある質問と回答
1.低圧鋳造ホイールが新エネルギー車に適しているのはなぜですか?
その高密度化はモーターの瞬間トルク(3000N・m以上)に耐え、軽量化(スチールホイールより40%軽量化)は直接的に航続距離を5%-8%向上させる。
2.金属組織分析によるクラックの原因究明方法は?
- 熱クラック:粒界に連続した酸化皮膜が存在し、ジグザグ網目状のクラックが入る。
- コールドフラクチャー:亀裂は直線的で、明確な溶解性のステップが見える。
- 応力腐食: クラック先端でのCl濃縮元素の存在 (EDS検出)
3.金型の寿命はクラック率にどのように影響しますか?
金型を5,000回以上使用すると、表面のマイクロクラックが25%の離型抵抗の増加につながり、定期的なレーザー肉盛補修(表面硬度をHRC 45以上に戻す)が必要になります。
4.今後の技術開発の方向性は?
プロセスの最適化には人工知能が導入され、機械学習アルゴリズムが圧力プロファイルをリアルタイムで調整し、クラッキング率を0.1%以下に制御することを目標に、生産性はさらに20%向上した。