Die Druckgusstechnologie: ein wichtiges Herstellungsverfahren, um Visionen Wirklichkeit werden zu lassen
发布时间:2024-12-24 分类:Nachrichten 浏览量:1684
In der modernen Fertigung gilt das Druckgussverfahren als ein wichtiges Mittel zur Herstellung von Präzisionsmetallteilen. Es ermöglicht die Herstellung komplex geformter Metallteile durch Einspritzen von geschmolzenem Metall in Präzisionsformen unter hohem Druck und ist in der Automobilindustrie, der Elektronik und anderen Bereichen weit verbreitet und unterstützt die technologische Entwicklung mehrerer führender Branchen. In diesem Beitrag werden die Kernprozesse, die Materialauswahl und die Anwendungen des Druckgussverfahrens eingehend analysiert und es wird aufgezeigt, wie dieses Verfahren zu Innovationen und Spitzenleistungen in der Fertigung führt.
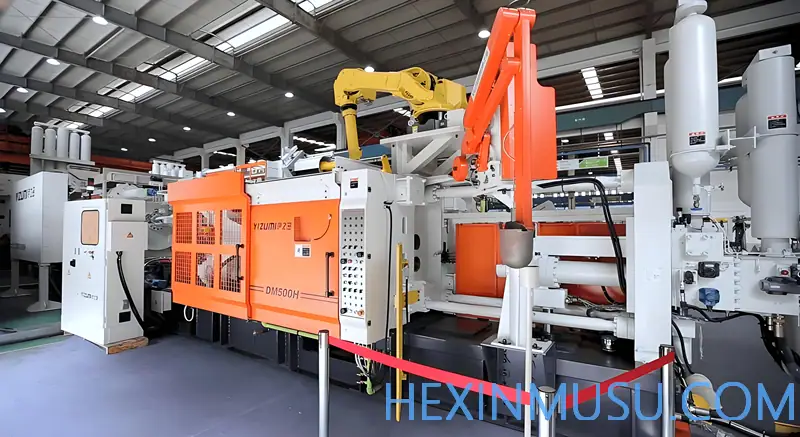
Was ist Druckguss?
Druckguss ist ein effizientes und genaues Verfahren des Metallgusses, bei dem wiederverwendbare Formen zur Herstellung komplex geformter Metallteile verwendet werden. Im Gegensatz zu herkömmlichen Gießverfahren wird beim Druckguss geschmolzenes Metall unter hohem Druck in die Form gespritzt. Das Verfahren eignet sich besonders für die Großserienproduktion und bietet hohe Genauigkeit, Wiederholbarkeit und eine hervorragende Oberflächengüte.
Ursprünglich wurde das Druckgussverfahren in der Druckindustrie eingesetzt, doch schon bald weitete sich sein Anwendungspotenzial auf eine Reihe von Bereichen aus, darunter die Automobil-, Luft- und Raumfahrt- sowie die Elektronikindustrie. Heute werden beim Druckguss hauptsächlich Leichtmetalle wie Aluminium, Zink und Magnesium verwendet, um die Herstellungsanforderungen einer breiten Palette von Produkten zu erfüllen, von kleinen, komplexen Komponenten bis hin zu wichtigen Automobilteilen. Der Hauptvorteil des Druckgießens besteht darin, dass Teile mit extrem engen Toleranzen hergestellt werden können und weniger Nachbearbeitung erforderlich ist, was es zu einer unverzichtbaren Technologie in der modernen Fertigung macht.
Druckgussverfahren
Der Produktionsprozess des Druckgusses lässt sich in mehrere wichtige Schritte unterteilen:
- Vorbereitung der Form
Formen sind die Grundlage des Druckgießverfahrens, und zu den üblichen Formen gehören Formen mit einem Hohlraum, Formen mit mehreren Hohlräumen und Kombinationsformen. Bei der Konstruktion der Form müssen die Komplexität des Teils und der Produktionsumfang berücksichtigt werden, und die Form muss vor der Verwendung gereinigt und vorgeheizt werden, um Risse und thermische Defekte zu vermeiden. - Einspritzvorgang
Beim Einspritzverfahren wird das geschmolzene Metall in verschiedenen Systemen geschmolzen und in die Form eingespritzt. Beim Warmkammersystem findet das Schmelzen innerhalb der Gießmaschine statt, während das Kaltkammersystem das geschmolzene Metall in die kalte Kammer gießt, wo es durch Druck in die Form gespritzt wird. - Abkühlung und Erstarrung
Das geschmolzene Metall wird abgekühlt und erstarrt in einer Form, um das endgültige Teil zu formen. Der Abkühlungsprozess erfordert einen kontrollierten Druck, um Defekte im Teil aufgrund von Schrumpfung zu vermeiden. - Schleudern (aus einem Flugzeug)
Sobald das Metall vollständig erstarrt ist, wird die Form geöffnet und der Auswerfer der Maschine drückt das Teil heraus. - Beschneiden und Nachbearbeiten
Um die Qualität des Teils zu gewährleisten, müssen überschüssiges Material und Grate entfernt werden. Falls erforderlich, kann die Genauigkeit des Teils durch Nachbearbeitungsmethoden wie Schleifen weiter verbessert werden.
Arten des Druckgusses
Je nach Schmelz- und Einspritzverfahren kann das Druckgussverfahren in zwei Haupttypen unterteilt werden: Warmkammerdruckguss und Kaltkammerdruckguss:
- Heißzellen-Druckguss (Metallurgie)
Geeignet für Metalle mit niedrigem Schmelzpunkt wie Zink und bestimmteAluminium. Bei diesem Verfahren wird das Metall mit einem pneumatischen Kolben durch einen Behälter für geschmolzenes Metall, der mit einer Druckgussmaschine verbunden ist, in die Form gespritzt. Es ist effizient, schnell und eignet sich für die Großserienproduktion von Kleinteilen, die häufig bei der Herstellung von Unterhaltungselektronik verwendet werden. - Kaltkammer-Druckguss (Metallurgie)
Wird für Metalle mit hohem Schmelzpunkt wie Aluminium- und Kupferlegierungen verwendet. Beim Kaltkammerdruckguss wird das geschmolzene Metall zunächst in eine kalte Kammer gegossen und dann durch einen Kolben in die Form gespritzt. Dieses Verfahren eignet sich für Teile, die eine hohe Festigkeit und Hitzebeständigkeit erfordern, und wird häufig in der Automobil- und Luftfahrtindustrie eingesetzt.
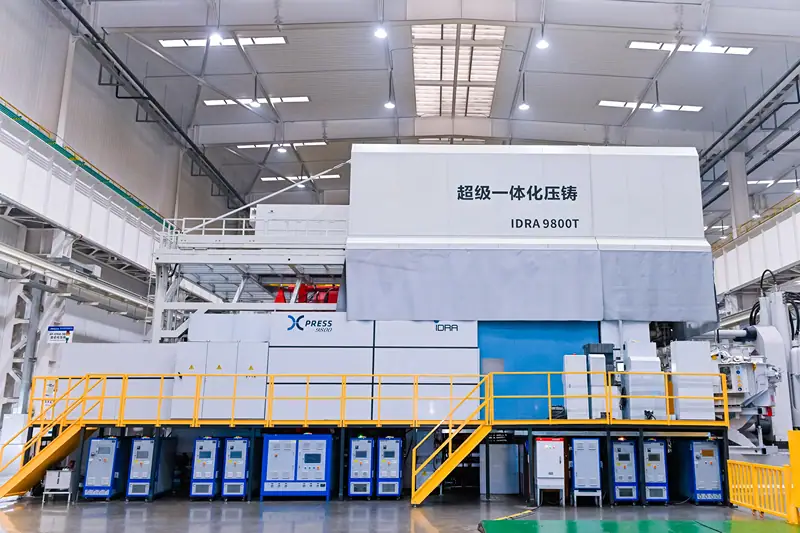
Druckgussvarianten und Innovationen
Da sich die Technologie ständig weiterentwickelt, gab es bei den Druckgussverfahren eine Vielzahl von Varianten und Innovationen, um den unterschiedlichen industriellen Anforderungen gerecht zu werden. Zum Beispiel:
- KokillengussSchmelzmetall wird unter Ausnutzung der Schwerkraft in die Form gespritzt und eignet sich daher für die Herstellung großer Mengen von Präzisionsgussteilen.
- DruckgussFüllen von Metall mit niedrigem oder hohem Druck, geeignet für die Herstellung von Teilen mit hohen Präzisionsanforderungen, wie z. B. Automobil- und Luft- und Raumfahrtteile.
- Vakuum-DruckgussVerbesserung der Oberflächenqualität und der Maßgenauigkeit durch Schaffung einer Vakuumumgebung, die die Lufteinschlüsse reduziert und für hochwertige Produkte geeignet ist.
- ExtrusionsdruckgussEs kann die mechanischen Eigenschaften und die Genauigkeit der Teile verbessern und wird häufig für Automobilteile verwendet.
- Semi-Solid-DruckgussHerstellung von Teilen mit komplexer Geometrie mit höherer Präzision und Festigkeit durch spezifische Gießtemperaturen.
Vergleich der Vor- und Nachteile des Druckgusses
Die Vorteile des Metalldruckgusses, eines in der industriellen Produktion weit verbreiteten Fertigungsverfahrens, haben ihm in der Massenproduktion große Bedeutung verliehen. Es hat jedoch auch einige Einschränkungen, die seinen Einsatz in bestimmten Anwendungsszenarien beeinträchtigen können. Im Folgenden werden die wichtigsten Vor- und Nachteile des Druckgusses und ihre Ursachen analysiert:
Vorteile des Druckgusses
- Ausgezeichnete Maßhaltigkeit
Metalldruckguss kann Teile mit hoher Maßgenauigkeit herstellen und eignet sich besonders für Anwendungen, bei denen enge Toleranzen erforderlich sind. Die Genauigkeit hängt von der Konstruktion der Form und dem Herstellungsverfahren ab. Eine höhere Maßgenauigkeit kann vor allem dann erreicht werden, wenn die Formen mit hochpräzisen CNC-Maschinen, z. B. 5-Achsen-CNC-Maschinen, hergestellt werden. Darüber hinaus trägt der Einsatz von Verfahrensvarianten wie Niederdruck- und Kokillenguss dazu bei, die Formen genau zu füllen und so die Genauigkeit des Teils zu erhöhen. - Komplexe Geometrie
Druckguss ist in der Lage, Teile mit komplexen Geometrien herzustellen, einschließlich Gussteilen, dünnen Wänden und anderen Konstruktionen. Diese Eigenschaft hat es dem Druckguss ermöglicht, Teile mit komplexen Strukturen und einer Vielzahl von Funktionen in Bereichen wie der Luft- und Raumfahrt, der Automobilindustrie und der Unterhaltungselektronik herzustellen. Auf diese Weise können die Konstrukteure mehr Funktionen in ein einziges Teil integrieren, wodurch sich die Notwendigkeit einer späteren Montage verringert. - Großserienproduktion für schnelle Lieferung
Das Druckgießen ist ein Großserienverfahren, das sich für die Herstellung großer Mengen von Teilen eignet. Beim Hochdruckgießen ist die Produktion aufgrund des hohen Drucks schneller, was die Produktionskosten pro Teileinheit senkt. Insbesondere bei Kombinationsformen können mehrere Teile gleichzeitig hergestellt werden, was die Produktivität und die Kosteneffizienz pro Teil erhöht. - Glatte Oberfläche
Aufgrund des hohen Drucks, der während des Druckgussverfahrens in das Metall gepresst wird, haben gegossene Metallteile in der Regel eine glatte Oberfläche, insbesondere im Bereich derNiederdruckguss,Schwerkraftgussund andere Verfahren. Diese hochwertige Oberflächenbehandlung verbessert nicht nur das Aussehen des Teils, sondern reduziert auch den Aufwand für nachfolgende Oberflächenbehandlungen. - Lange Lebensdauer der Form
DruckgussformSie bestehen in der Regel aus hochwertigem Stahl mit hervorragender Beständigkeit gegen hohe Temperaturen und Drücke. Dank dieser zähen Stähle können die Formen einem längeren Einsatz standhalten und haben eine lange Lebensdauer, wodurch die Häufigkeit des Formenwechsels und die Wartungskosten für eine langfristige Produktion reduziert werden.
Nachteile des Druckgusses
- Nur für Nichteisenmetalle
Das Druckgussverfahren wird hauptsächlich für Nichteisenmetalle wie Aluminium, Zink und Magnesium angewendet. Diese Metalle haben einen mittleren Schmelzpunkt und lassen sich leicht unter hohem Druck in Formen spritzen. Für Eisenmetalle mit höherem Schmelzpunkt, wie Stahl und Eisen, ist das Druckgussverfahren jedoch nicht geeignet. Für Metalle wie Stahl und Eisen sind spezielle Ausrüstungen und komplexere Verfahren zum Gießen erforderlich, was die Anwendung des Druckgusses etwas einschränkt. - Hohe Formkosten
Druckgussformen sind in der Herstellung teurer, vor allem wenn man dieBearbeitung mit numerischer SteuerungDie Herstellung von Gussformen ist ein komplexer und kostspieliger Prozess. Insbesondere bei der Herstellung komplexer Teile treibt die Verwendung von Formen aus hochwertigem Stahl die Kosten weiter in die Höhe. Das Druckgussverfahren eignet sich zwar für die Großserienproduktion, aber die Kosten für die Werkzeuge können bei kleinen Chargen oder komplexen Teilen ein limitierender Faktor sein. - Empfindlichkeit gegenüber Mängeln
Druckgussteile können während des Produktionsprozesses Porosität, Schrumpfung, Porosität und andere Defekte aufweisen, insbesondere beim Hochdruckguss sind diese Defekte häufiger. So können beispielsweise durch Lufteinschlüsse während des Gießens Poren auf der Oberfläche des Teils entstehen, die bei der Wärmebehandlung Luftblasen bilden können, was die Qualität des Teils beeinträchtigt. Zur Behebung dieser Mängel sind unter Umständen zusätzliche Schritte der Oberflächenbearbeitung erforderlich, was die Produktionskosten erhöht. - Nicht für die Kleinserienproduktion geeignet
Das Druckgussverfahren eignet sich zwar für die Großserienproduktion, aber die Anfangsinvestitionen sind hoch, insbesondere die Fixkosten für die Herstellung der Formen und die Einrichtung der Anlagen. Daher eignet sich das Druckgussverfahren in der Regel nicht für die Kleinserienfertigung oder die Herstellung von Einzelteilen. Für die Kleinserienproduktion sind andere Verfahren (wie Spritzguss oder CNC-Bearbeitung) möglicherweise besser geeignet und können die Kosten und Produktionsvorlaufzeiten verringern.
Hershey's Metallwerkstoffe im Druckguss
Die im Druckgussverfahren verwendeten Metallwerkstoffe sind in der Regel Nichteisenlegierungen wie Aluminium, Magnesium und Zink. Diese Legierungen haben unterschiedliche Leistungsmerkmale und eignen sich für verschiedene Anwendungsanforderungen. Die folgende Tabelle enthält einen detaillierten Vergleich der gängigen Druckgusslegierungen mit ihren wichtigsten Zusammensetzungen, Schmelzpunkten, Eigenschaften und typischen Anwendungen.
Legierungen | Gemeinsame Subtypen | Basis | Schmelzpunkt (°C) | Wichtigste Merkmale | typische Anwendung |
---|---|---|---|---|---|
Aluminium | a380, a360, a390, a413, adc12 | Aluminium (Al), Kupfer (Cu), Silizium (Si), Magnesium (Mg) | 577 - 660 | Geringes Gewicht, korrosionsbeständig, hohe Festigkeit, gute Verarbeitbarkeit und kostengünstig. | Automobilindustrie (Motorkomponenten, Räder, Fahrwerk), Luft- und Raumfahrt (Strukturkomponenten, Gehäuse), Elektronik (Gehäuse, Karosserien) |
Magnesiumlegierung | az91d, am60b, as41b | Magnesium (Mg), Aluminium (Al), Zink (Zn) | 632 - 650 | Extrem leicht, gute Gießbarkeit für gewichtssensible Anwendungen, ausgezeichnete Gießbarkeit. | Luft- und Raumfahrt (Karosseriestruktur, Innenraumkomponenten), Automobilbau (Leichtbaukomponenten), Elektronik (Handheld-Geräte, Mobiltelefongehäuse) |
Zinklegierung | Zinklegierung #2, #3, #5, #7, ZA8, ZA27 | Zink (Zn), Aluminium (Al), Kupfer (Cu), Magnesium (Mg) | 381 - 419 | Ausgezeichnete Gießbarkeit, niedriger Schmelzpunkt, geeignet für komplexe Konstruktionen und kostengünstig. | Elektronik (Stecker, Gehäuse), Eisenwaren (Schlösser, Knöpfe), Spielzeug und Automobilteile (dekorative Teile, Zahnräder) |
Kupferlegierung | Messing (z. B. C85700), Bronze (z. B. C93200) | Kupfer (Cu), Zink (Zn) (Messing); Kupfer (Cu), Zinn (Sn) (Bronze) | 900 - 1083 | Hohe Festigkeit, ausgezeichnete Leitfähigkeit und Korrosionsbeständigkeit, langlebig. | Rohre (korrosionsbeständige Wasserrohre, Gasrohre), elektrische Anschlüsse (Klemmen, elektrische Kontakte), Schiffskomponenten (korrosionsbeständige Komponenten), Lager |
Zinnlegierung | - | Zinn (Sn) (90%), Kupfer (Cu) (2,5%), Blei (Pb) (7,5%), Antimon (Sb) | 170 - 230 | Niedriger Schmelzpunkt, gute Fließfähigkeit, Korrosionsbeständigkeit, einfaches Gießen. | Dekorationsartikel (Schmuck, Kunsthandwerk), Figurinen, Souvenirs |
Bleilegierung | - | Blei (Pb), Zinn (Sn) | 183 - 327 | Niedriger Schmelzpunkt, weich, gute Korrosionsbeständigkeit, geeignet zur Strahlenabschirmung. | Strahlungsabschirmung (medizinische Geräte, kerntechnische Anlagen), Batterien (werden nach und nach ersetzt) |
Zinnbasislegierung | - | Zinn (Sn), Kupfer (Cu), Antimon (Sb) | 232 | Niedriger Schmelzpunkt, gute Gießeigenschaften, gute Korrosionsbeständigkeit. | Elektronische Komponenten (Lötmaterialien, elektronische Teile), Schmuck, Spezialanwendungen (Kleinteile, feiner Schmuck) |
Vergleich des Druckgusses mit anderen Herstellungsverfahren
Das Druckgießen wird häufig mit anderen Fertigungsverfahren (z. B. Spritzgießen, Schmieden, Stanzen usw.) verwechselt, vor allem für diejenigen, die neu in der Fertigung sind. Trotz ihrer Ähnlichkeiten hat jedes Verfahren seine eigenen Vorteile und Anwendungsbereiche. Im Folgenden wird das Druckgießen mit gängigen Verfahren wie dem Spritzgießen und Schmieden verglichen, um die Unterschiede und Anwendungsszenarien zu verdeutlichen:
Unterschied zwischen Druckguss und Spritzguss
Druckguss und Spritzguss sind zwei gängige Formverfahren, die beide nach dem Spritzgussprinzip funktionieren und sich für die Herstellung von Teilen mit komplizierten Details und hervorragender Oberflächengüte eignen. Sie unterscheiden sich jedoch in den verwendeten Materialien und Verfahren. Im Folgenden werden die Hauptunterschiede zwischen den beiden Verfahren erläutert:
Unstimmigkeit | Druckguss | Spritzgießen |
---|---|---|
Arbeitsabläufe | Einspritzen von geschmolzenem Metall unter Druck in vorgefertigte Stahlformen | Einspritzen von geschmolzenem Kunststoff unter Druck in vorgefertigte Stahl- oder Aluminiumformen |
Anfertigungen | Nichteisenmetall-Legierungen (z. B. Aluminium, Zink, Magnesium) | Thermoplaste oder Duroplaste |
Materialien für Formen | Stahl (Chemie) | Stahl oder Aluminium |
Abklingzeit | Längere Abklingzeit | Kürzere Abklingzeit |
Produktionsgeschwindigkeit | relativ langsam | relativ bald |
Bearbeitungskosten | Höhere Werkzeugkosten (bei Verwendung von Stahlwerkzeugen) | Geringere Werkzeugkosten (Verwendung von Aluminiumwerkzeugen) |
Komponentenkosten | Höher (aufgrund der längeren Produktionszeit) | Niedriger (schnellere Produktionszeit) |
Unterschied zwischen Druckguss und Schmieden
Der Hauptunterschied zwischen Schmieden und Druckguss ist die Art der Formgebung. Beim Schmieden wird das Metall durch Anwendung von Druckkräften in einem festen Zustand geformt, während beim Druckguss geschmolzenes Metall in eine vorher entworfene Form gespritzt wird. Die beiden Verfahren unterscheiden sich auch in Bezug auf die verwendbaren Materialien, die Produktionsgeschwindigkeit und die Leistungsfähigkeit der Teile:
Unstimmigkeit | Schmiede (Metall) | Druckguss |
---|---|---|
Arbeitsabläufe | Umformung von erhitztem Metall durch Aufbringen einer Druckkraft | Einspritzen von geschmolzenem Metall in eine Form unter Druck |
Anfertigungen | Für Eisen- und Nichteisenmetalle wie Stahl und Aluminium | Für Nichteisenmetalle wie Aluminium, Zink und Magnesium |
Formgebende Materialien | Kein Bedarf an Formen, aber Verwendung von Formen zur Optimierung der Form | Es müssen Formen verwendet werden |
Produktionsgeschwindigkeit | Langsamer | relativ bald |
Toleranzkontrolle | Mittlere Toleranz | Hochpräzise Toleranzkontrolle |
Eigenschaften des endgültigen Teils | Verbesserung der mechanischen Eigenschaften | Mechanische Eigenschaften hängen vom Gussmaterial ab |
Unterschied zwischen Druckguss und Stanzen
Das Stanzen ist ein Verfahren zur Umformung von Blechen mit Hilfe einer Presse und eignet sich für die Massenproduktion von dünnwandigen Teilen. Im Vergleich zum Druckguss weist das Stanzen andere Formmaterialien und -verfahren auf, insbesondere im Hinblick auf die Komplexität der anwendbaren Teile und die Produktivität:
Unstimmigkeit | Druckguss | Stanze |
---|---|---|
Arbeitsabläufe | Einspritzen von geschmolzenem Metall in eine Form zum Umformen | Formung von Teilen aus Blech durch Stanzen mit Hilfe einer Matrize. |
Anfertigungen | Hauptsächlich Nichteisenmetall-Legierungen (z. B. Aluminium, Zink) | Geeignet für alle Arten von Blechen (z.B. Stahl, Aluminium) |
Materialien für Formen | Stahl (Chemie) | Stahl (Chemie) |
Form des Teils | Für komplexe Formteile | Für dünnwandige Teile und einfache Formen |
Produktionsgeschwindigkeit | Langsamer | relativ bald |
genau | äußerst präzise | Geringere Präzision |
Der Unterschied zwischen Druckguss und 3D-Druck
Der 3D-Druck ist ein auf additiver Fertigung basierendes Verfahren, bei dem Teile durch schichtweises Auftragen von Materialien hergestellt werden. Der 3D-Druck bietet eine größere Flexibilität und schnellere Prototyping-Möglichkeiten als der Druckguss, unterscheidet sich aber in der Produktionsgeschwindigkeit und der Leistungsfähigkeit der Teile:
Unstimmigkeit | Druckguss | 3D-Druck |
---|---|---|
Arbeitsabläufe | Einspritzen von geschmolzenem Metall in eine Form zum Umformen | Schichtweises Drucken von Materialien auf der Grundlage digitaler Modelle |
Anfertigungen | Nichteisenmetall-Legierungen (z. B. Aluminium, Zink) | Thermoplastische Kunststoffe, Metallpulver, usw. |
Materialien für Formen | Stahl (Chemie) | Keine Gussformen erforderlich |
Produktionsgeschwindigkeit | Langsamer | relativ bald |
genau | äußerst präzise | Mäßige Präzision |
Gerät | Massenproduktion von komplexen Teilen | Schnelles Prototyping, Kleinserienfertigung |
Gängige Druckgusswerkstoffe und deren Auswahl
Aluminium, Zink, Magnesium und andere Legierungen sind gängige Druckgusswerkstoffe, die jeweils einzigartige Eigenschaften aufweisen und sich für unterschiedliche Anwendungsszenarien eignen. Im Folgenden werden die Eigenschaften einiger gängiger Legierungen beschrieben:
- AluminiumLeicht, korrosionsbeständig, einfach zu verarbeiten und weit verbreitet in der Automobilindustrie, der Luft- und Raumfahrt und der Elektronik.
- MagnesiumlegierungSehr leicht für gewichtskritische Anwendungen wie Luft- und Raumfahrt und Unterhaltungselektronik.
- ZinklegierungNiedriger Schmelzpunkt, ausgezeichnete Gießbarkeit, wird häufig für elektronische Produkte, Hardware und Spielzeugteile verwendet.
- KupferlegierungHohe Festigkeit und gute elektrische Leitfähigkeit für elektrische Anschlüsse und Schiffskomponenten.
Optimierung von Konstruktion und Fertigung
Die Konstruktion von Druckgussteilen hängt nicht nur von der Materialauswahl ab, sondern muss auch Faktoren wie Teilegeometrie, Entnahmewinkel, Verrundungsradius usw. berücksichtigen, um die Leistung, Herstellbarkeit und Kosteneffizienz der Teile zu verbessern. So kann beispielsweise ein geeigneter Entformungswinkel wirksam verhindern, dass Teile an der Form haften bleiben, und das Risiko von Beschädigungen verringern; ein angemessener Verrundungsradius kann dazu beitragen, Spannungen gleichmäßig zu verteilen und Spannungskonzentrationen zu vermeiden.
zu einem Urteil gelangen
Der Druckguss ist dank seiner hohen Präzision und der Möglichkeit, große Stückzahlen zu produzieren, zu einer unverzichtbaren Technologie in der modernen Fertigung geworden. Ob Automobilteile, Elektronikgehäuse oder Komponenten für die Luft- und Raumfahrt, die Druckgusstechnologie bietet eine solide Grundlage für Innovation und herausragendes Design. Mit der Weiterentwicklung von Werkstoffen und Verfahren wird der Druckguss auch in Zukunft effizientere und hochwertigere Lösungen für eine Vielzahl von Branchen bieten.
Gemeinsame Probleme beim Druckguss und Strategien zur Bewältigung
Warum sind Druckgussteile anfällig für Porosität?
Taschen werden in der Regel dadurch verursacht, dass das Metall während des Einspritzvorgangs nicht vollständig entlüftet wird, oder durch eine mangelhafte Werkzeugkonstruktion (z. B. ein schlechtes Entlüftungssystem). Zu den Strategien gehören die Optimierung des Entlüftungsdesigns der Form, die Anpassung der Einspritzgeschwindigkeit und des Drucks sowie die Verwendung eines effizienteren Entlüftungssystems.
Warum können Fehler auf der Oberfläche von Druckgussteilen auftreten?
Oberflächenfehler wie Blasen, Falten und Kratzer werden meist durch unebene Formoberflächen oder ungleichmäßigen Metallfluss verursacht. Um solche Probleme zu vermeiden, sollte die Oberflächenbeschaffenheit der Form regelmäßig überprüft werden, um sicherzustellen, dass die Einspritztemperatur und die Fließgeschwindigkeit stabil sind.
Was ist das Problem mit Lunkern in Druckgussteilen?
Schrumpfung Loch ist aufgrund der Gießerei Kühlung Metall Schrumpfung nicht auf den Füllstoff wieder aufzufüllen, erscheinen oft in der großen oder komplexe Form des Druckgusses. Schrumpfung kann durch die Optimierung des Formdesigns, die Verbesserung der Effizienz des Gießsystems und die Anpassung der Kühlrate wirksam vermieden werden.
Sind Druckgussteile anfällig für Risse?
Risse entstehen in der Regel, wenn das Metall ungleichmäßig fließt oder zu schnell abkühlt, und können durch einen zu hohen Einspritzdruck oder eine schlechte Werkzeugkonstruktion verursacht werden. Die Rissbildung kann durch die Kontrolle der Einspritzgeschwindigkeit, der Temperatur und des Drucks sowie durch die Verwendung hochfester Materialien reduziert werden.
Wie sieht es mit der Dimensionsstabilität von Druckgussteilen aus?
Die Instabilität der Abmessungen kann auf Verschleiß der Form, instabilen Einspritzdruck oder unsachgemäße Temperaturregelung zurückzuführen sein. Eine regelmäßige Überholung und Wartung des Werkzeugs zur Aufrechterhaltung stabiler Einspritzbedingungen sowie eine Feineinstellung des Temperaturregelungssystems können das Problem der Dimensionsinstabilität wirksam lösen.
Wie wirkt sich der Formenverschleiß auf die Qualität des Druckgusses aus?
Der Verschleiß von Formen kann zu einem Verlust der Produktgenauigkeit führen und sogar das Aussehen und die Leistung von Gussstücken beeinträchtigen. Um dem Formenverschleiß entgegenzuwirken, sollten die Formen regelmäßig inspiziert und ausgetauscht werden, verschleißfeste Materialien verwendet und die Konstruktion und der Prozess der Formen optimiert werden.
Warum sind Druckgussteile anfällig für Verformungen?
Verformungen sind in der Regel auf eine ungleichmäßige Abkühlung oder eine schlechte Formgestaltung zurückzuführen, insbesondere bei großen oder komplexen Gussteilen. Das Risiko von Verformungen kann durch die Anpassung des Kühlsystems und die Optimierung der Formkonstruktion verringert werden.
Wie kann die kalte Segregation verringert werden?
Kaltentmischung ist ein Delaminationsfehler, der dadurch entsteht, dass das Metall beim Einspritzen in die Form nicht vollständig verschmilzt. Um Kaltentmischung zu vermeiden, müssen die Einspritzgeschwindigkeit und die Temperatur optimiert werden, um einen reibungslosen Metallfluss zu gewährleisten, und das Gießsystem und die Angüsse müssen entsprechend ausgelegt sein.
Ist eine Nachbearbeitung von Druckgussteilen erforderlich?
Die Nachbearbeitungsanforderungen für Druckgussteile hängen von den Konstruktionsanforderungen und den Kriterien für die Oberflächenqualität des Teils ab. Einige Teile erfordern zusätzliche Bearbeitungen wie Schleifen, Bohren oder Entgraten, um enge Toleranzen und Oberflächengüten einzuhalten.