Progettazione di stampi per la pressofusione di alluminio: una guida pratica dal processo all'ottimizzazione
发布时间:IL SUO NOME È UN'ALTRA COSA.2025-02-15 分类: 分类informazioni al pubblico 6D4F↩览量:IL MIO NOME È2743
In qualità di ingegnere senior di Ningbo Hexin, impegnato da più di 20 anni nell'industria della colata, sono ben consapevole dell'alluminio e del fatto che il suo peso è molto elevato. stampo per pressofusione La posizione centrale nell'industria manifatturiera. Che si tratti di componenti automobilistici, di prodotti elettronici 3C o di componenti aerospaziali, il processo di pressofusione di alluminio ad alta efficienza e precisione è inseparabile dalla progettazione dello stampo di supporto sottile. Questo articolo sarà combinato con l'esperienza pratica, l'analisi sistematica dei punti di progettazione degli stampi per la pressofusione di alluminio, le tendenze tecnologiche e la strategia di ottimizzazione, per fornire una guida pratica ai colleghi del settore.
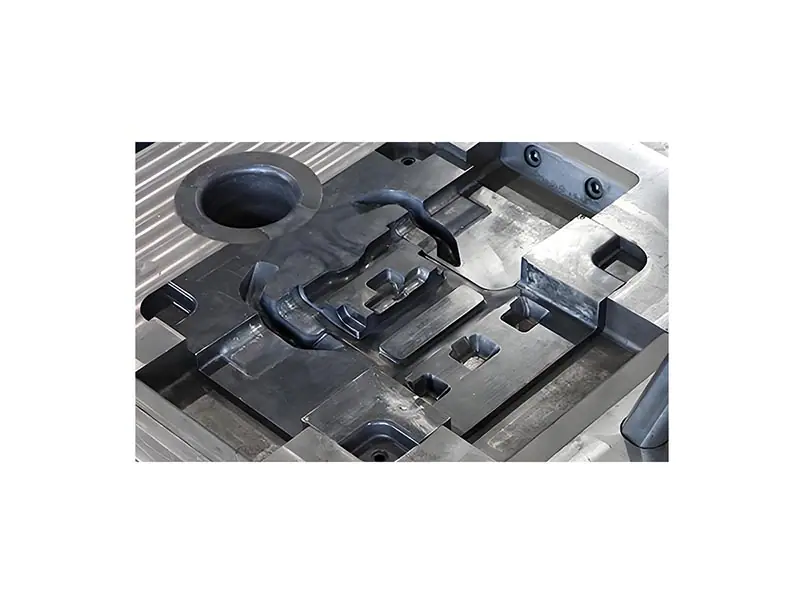
Il valore fondamentale di uno stampo per la pressofusione di alluminio: perché è la chiave del successo o del fallimento del processo
Lo stampo di pressofusione non è solo la "sagoma" di formatura del metallo, ma anche l'efficienza produttiva e la qualità del prodotto.fattore determinanteL'importanza del programma è triplice. La sua importanza si riflette in tre aree:
- Precisione accurata
La progettazione della cavità dello stampo determina direttamente la tolleranza dimensionale (di solito ±0,1 mm) e la finitura superficiale (Ra 1,6~3,2μm) della colata. Ad esempio, nella pressofusione del blocco motore automobilistico, la progettazione del sistema di raffreddamento dello stampo, se irragionevole, porterà a un ritiro locale non uniforme, innescando porosità o deformazioni. - Alta efficienza produttiva
Un set di stampi a più cavità ottimizzati può aumentare l'efficienza produttiva di oltre 300%. Prendendo come esempio il progetto di una scocca del motore di un veicolo a nuova energia, dopo l'adozione di uno stampo a 4 cavità, la produzione oraria è passata da 15 a 60 pezzi, mentre il tasso di rendimento è rimasto stabile a oltre 98%. - Vantaggio di costo
La durata dello stampo ha un impatto diretto sul costo per pezzo. Utilizzando l'acciaio per lavorazioni a caldo H13 per gli stampi, la durata dello stampo può essere aumentata da 100.000 a 500.000 stampi grazie al trattamento superficiale TD (metodo di diffusione termica), che riduce significativamente il costo di condivisione.
Cinque principali tipi di stampi per la pressofusione di alluminio e strategia di selezione
Tipo di stampo | Scenari applicabili | ciclo dei costi | Caratteristiche tecniche |
---|---|---|---|
Stampo per prototipi | Convalida di piccoli lotti (<500 pezzi) | Costo ridotto/2-3 settimane | Stampa 3D +lavorazioneprocesso composito |
Utensili rapidi | Produzione pilota (500-5000 pezzi) | Costo medio/4-6 settimane | Produzione additiva con rivestimento laser |
Stampo unitario | Multi-specie e piccoli lotti | Design modulare | Cambio rapido degli inserti della cavità |
Stampo di produzione | Alto volume (>100.000 pezzi) | Costo elevato/8-12 settimane | Struttura a più cursori + sistema di raffreddamento a punti |
Stampo per rifilatura | Sbavatura e separazione dei canali | necessario per | Servocomando idraulico + guida di precisione |
Suggerimenti per la selezione::
- Pressofusione ad alta pressione(HPDC)La priorità è data agli stampi di produzione con sistemi a vuoto per ridurre i fori d'aria;
- Parti complesse a parete sottile(ad esempio, i telai centrali dei telefoni cellulari) Si raccomanda l'uso di utensili rapidi, combinati con tecniche di fusione a pressione locali;
- Produzione flessibile multivariataGli stampi unitari possono essere utilizzati per ridurre i tempi di cambio formato a meno di 30 minuti.
Le sei regole d'oro della progettazione di stampi per la pressofusione di alluminio
- Ottimizzazione della linea frattale
La linea di troncatura deve evitare le superfici funzionali critiche. Ad esempio, il radiatore di una stazione base 5G utilizza la troncatura di superfici curve in modo da produrre bave su superfici non a contatto, riducendo i costi di post-lavorazione. - Progettazione idrodinamica di sistemi di canali di flusso
adozioneCoclea trasversale conica(Ingresso 8 mm → Uscita 4 mm), insieme all'angolo di apertura interno di 30°, può ottenere un riempimento regolare del liquido di alluminio ed evitare lo slagging da ossidazione causato dal flusso turbolento. - Controllo del bilancio termico dei sistemi di raffreddamento
La parte centrale è dotata di inserti in rame berillio (conduttività termica 210 W/mK), che possono essere utilizzati con il termostato dello stampo per ottenere un controllo della temperatura a gradiente (250℃ nell'area del gate → 180℃ alla fine) e ridurre il tempo di raffreddamento di 20%. - Calcolo scientifico dell'inclinazione di sformatura
A seconda del ritiro della lega (circa 0,6% per l'ADC12) e dei requisiti di superficie, l'inclinazione della parete esterna è di 1°~1,5°, che aumenta a 2°~3° per le parti a cavità profonda. Ad esempio, la struttura a cavità profonda di un guscio di un UAV utilizza una pendenza di 3° e la resistenza all'espulsione è ridotta di 40%. - Disposizione precisa dei serbatoi di scarico e di troppopieno
Nell'area di riempimento finale è presente un serbatoio di troppopieno a gradini (profondità 0,3 mm→0,8 mm) e con la valvola del vuoto (vuoto ≤ 50mbar) è possibile controllare la porosità al di sotto di 0,5%. - Selezione avanzata dei materiali per stampi
- Parti normali: acciaio H13 (durezza 48-52 HRC)
- Requisiti di alta resistenza all'usura: acciaio DIEVAR (con aggiunte di cobalto e molibdeno)
- Scene resistenti alla corrosione: STAVAX ESR (lucidato a specchio a Ra 0,05μm)
Tecnologia all'avanguardia nel settore: la digitalizzazione e l'intelligenza favoriscono l'aggiornamento degli stampi
- Iterazioni di progettazione basate sulla simulazione AI
Con il software AnyCasting/MAGMA, l'intero processo di simulazione di riempimento-solidificazione-sollecitazione può essere completato in 48 ore e il rischio di ritiro può essere previsto in anticipo. Il progetto di una scatola di ingranaggi ha ottimizzato la posizione del gate attraverso la simulazione, riducendo di 3 volte il numero di prove stampo. - Corsi d'acqua di raffreddamento conformi stampati in 3D
L'uso della tecnologia SLM (Selected Zone Laser Melting) per la produzione di corsi d'acqua sagomati ha permesso di controllare la differenza di temperatura dello stampo entro ±5°C, riducendo in modo significativo i nodi termici. Dopo l'applicazione di uno stampo per paralumi a LED, il tempo di ciclo è stato ridotto di 18%. - Sistema di monitoraggio degli stampi Internet of Things (IoT)
I sensori di temperatura/pressione sono impiantati in punti critici dello stampo per monitorare in tempo reale le condizioni della superficie della cavità. Quando viene rilevata una fluttuazione anomala della forza di serraggio (>5%), viene automaticamente emesso un avviso per evitare difetti del lotto.
Caso di studio: ottimizzazione dello stampo del vassoio della batteria per un veicolo a nuova energia
sfida::
- Dimensioni del prodotto 1200×800 mm, spessore medio delle pareti 2,5 mm, tenuta all'aria ≤ 0,5Pa-m³/s richiesta
- La resa iniziale è di soli 65%, i difetti principali sono la segregazione a freddo e la deformazione.
prescrizione::
- Percorso di riempimento bilanciato con alimentazione tangenziale a doppia paratoia
- Nucleo dello stampo impiantato con 12 serie di tubi di raffreddamento a impulsi per il controllo dinamico della temperatura
- Sistema di espulsione con molle a gas di azoto per una forza di rilascio equilibrata
basato sui risultati::
- Resa migliorata a 92%
- Battito di produzione ridotto da 180 a 140
- La durata dello stampo supera i 300.000 cicli di stampaggio
Domande frequenti (FAQ)
Q1: Come valutare la forza tecnica dei fornitori di stampi?
- Metriche chiave: valori di Cpk per i casi passati (≥1,33), capacità di analisi CAE, completezza dei rapporti sugli stampi di prova.
D2: Come scegliere il rivestimento superficiale per lo stampo?
- Convenzionale: rivestimento in CrN (durezza 2200 HV)
- Altamente resistente all'usura: AlCrN (resistenza alla temperatura di 900°C)
- Miglioramento del rilascio: rivestimento diamantato DLC
D3: Migliori pratiche per la manutenzione delle muffe?
- Quotidianamente: controllare la lubrificazione del ditale (utilizzare grasso per alte temperature NLGI grado 2)
- Ogni 5000 stampi: l'elettroerosione ripara le piccole crepe
- Ogni 50.000 stampi: trattamento di tempra integrale (550°C x 2h)
osservazioni conclusive
La progettazione di uno stampo per la pressofusione di alluminio è una combinazione di scienza e arte, che richiede calcoli ingegneristici rigorosi e si basa su una ricca esperienza pratica. Con la profonda penetrazione della tecnologia digitale, l'industria degli stampi sta inaugurando il nuovo paradigma "progettazione intelligente - produzione di precisione - manutenzione predittiva". In qualità di operatori del settore, l'unico modo per assumere un ruolo di primo piano nel triangolo dei costi, dell'efficienza e della qualità è continuare ad abbracciare l'innovazione.
Per soluzioni di stampi personalizzate o per una consulenza tecnica. Benvenuti al contatto Team di Ningbo Hersin Casting - Con 20 anni di esperienza, diamo ai vostri prodotti la massima precisione e prestazioni.