Rissbildung in Niederdruckguss-Aluminiumradnaben - Ursachen und Verbesserungsmaßnahmen
发布时间:2025-01-27 分类:Nachrichten 浏览量:1982
Niederdruckguss Kann ein hohes Maß an Mechanisierung und Automatisierung zu erreichen, die Produktivität zu erhöhen (10 ~ 15 Typ / h), kann es auch viele negative menschliche Faktoren in den Produktionsprozess zu reduzieren, verbessern die Rate der fertigen Produkte, eine deutliche Verringerung der Arbeitsintensität der Arbeitnehmer. Allerdings ist die Qualität der Niederdruck-Gussteile durch den Prozess-Plan, Prozess-Parameter, Schimmel-Struktur und den manuellen Betrieb und andere Faktoren, eine unangemessene Design oder unsachgemäße Bedienung der Verbindung kann dazu führen, dass Niederdruck-Gießen Mängel. Die Entstehung von Rissen im Aluminiumrad ist ein wichtiger Faktor, der die Produktionskosten und die Produktivität der Unternehmen beeinflusst. Daher ist es besonders wichtig, die Ursachen für Risse in Aluminiumrädern aus Niederdruckguss zu erörtern. Als nächstes werde ich mit Ihnen in China Niederdruckgießerei Gießen diskutieren Aluminium Entstehung von Rissen in Fahrzeugrädern und Maßnahmen zu ihrer Beseitigung.
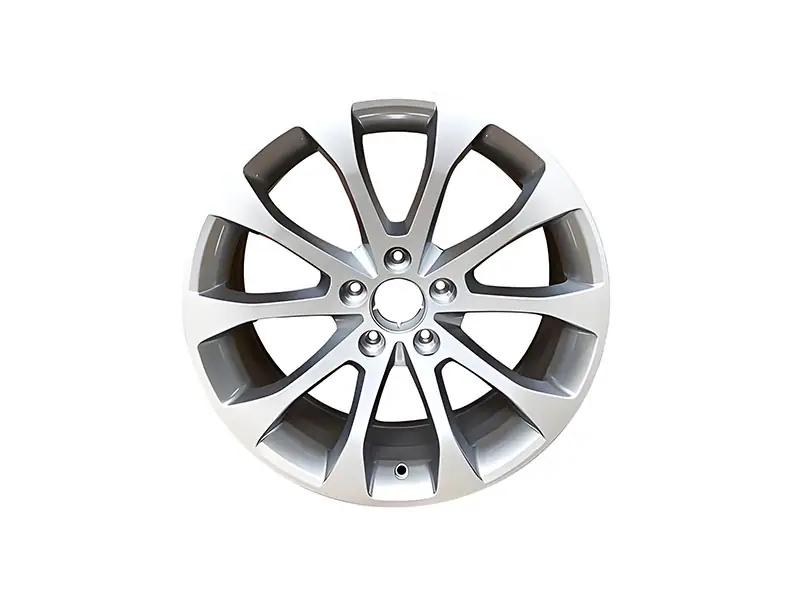
Was ist ein Niederdruckgießrad?
Niederdruckgussräder werden im Niederdruckgussverfahren hergestellt, das eine hohe Dichte, hohe Festigkeit und eine gute Qualitätskontrolle gewährleistet. Bei diesem Verfahren wird eine flüssige Legierung bei niedrigem Druck in eine Form gespritzt, wo die Legierung abkühlt und erstarrt. Im Niederdruckgussverfahren werden Räder mit hoher Dichte, homogener Struktur, guter Festigkeit und Zähigkeit hergestellt, die für die Massenproduktion geeignet sind.
Der Produktionsprozess ist in mehrere Schritte unterteilt: Zunächst wird die flüssige Legierung in die Form gespritzt, dann wird die Legierung abgekühlt und verfestigt, und schließlich wird das Rad durch Wärmebehandlung, Endbearbeitung und Lackierung fertiggestellt. Durch dieses Verfahren werden Luftblasen und Verunreinigungen reduziert, die Festigkeit und Präzision verbessert und die Sicherheit des Rades erhöht.
zusammen mitSchwerkraftgussDas Niederdruckgießen ist effizienter und erzeugt qualitativ bessere Produkte als das Niederdruckgießen. Beim Schwerkraftgießen fließt das Metall durch die Schwerkraft, was zu einer ungleichmäßigen Verteilung führen kann, was die Qualität und Sicherheit beeinträchtigt. Beim Niederdruckguss wird der Fluss der Aluminiumlegierung durch Druck gesteuert, was die Genauigkeit und Festigkeit der Räder gewährleistet.
Infolgedessen gewinnen Niederdruckgussräder in der Automobilherstellung zunehmend an Bedeutung und bieten hohe Effizienz, Qualität und Sicherheit.
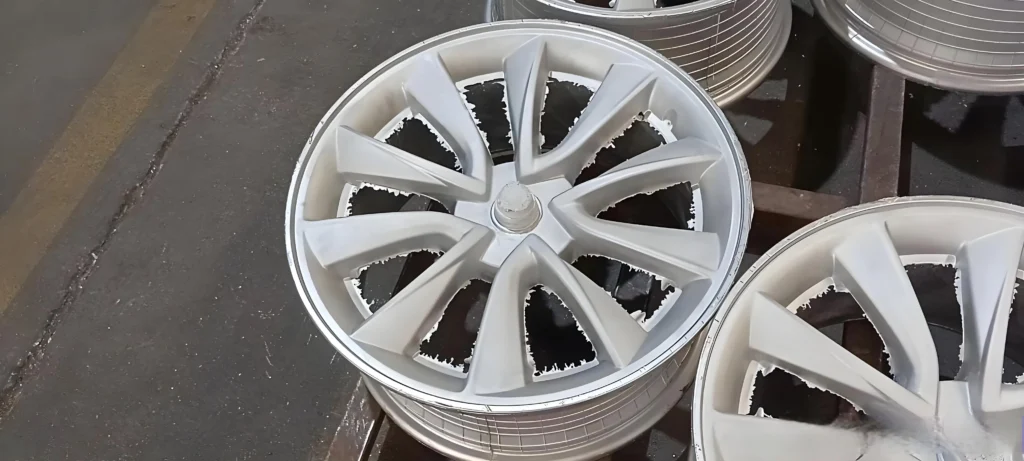
Niederdruckgießrad Technologievorteil und industrieller Wertumbau
Revolution in der Präzisionsfertigung durch mechanische Automatisierung
Die Niederdruckgusstechnologie hat durch ein hohes Maß an Mechanisierung und Automatisierung eine stabile Produktionskapazität von 10 bis 15 Stück pro Stunde erreicht, was etwa 30% über der Effizienz des traditionellen Schwerkraftgießens liegt. Ihr Kernprinzip ist die Verwendung von Niederdruckgas (0,02-0,08MPa), um flüssige Aluminiumlegierungen gleichmäßig in die Formhohlräume zu pressen, wodurch die Probleme des aufgewirbelten Gases und der oxidierten Schlacke vermieden werden, die durch das freie Fließen der Metallflüssigkeit beim Schwerkraftgießen entstehen. Durch die Einführung der vollautomatischen Niederdruckgießanlage konnte die Ausbeute von 82% auf 96% gesteigert werden, während die Personalkosten um 45% gesenkt wurden. Durch die Kombination aus geschlossenem Regelkreis für die Formtemperatur und intelligenten Drucksensoren konnte die innere Körnung des Gussteils bis auf Mikron-Ebene verfeinert werden, und die dynamische Biegewechselfestigkeit der Radnabe überstieg 1.000.000 Zyklen, was den Anforderungen an Leichtgewicht und Sicherheit von High-End-Fahrzeugen voll entspricht. Damit werden die doppelten Anforderungen an Leichtgewicht und Sicherheit von High-End-Modellen voll erfüllt.
Interdisziplinäre Diagnose von Rissursachen in Niederdruckgießrädern
Tiefgreifende Korrelation zwischen Rissmorphologie und Versagensmechanismen
Bei der Herstellung von Rädern aus Aluminiumlegierungen ist die Bildung von Rissen häufig das Ergebnis des Zusammenwirkens mehrerer Faktoren, wie z. B. der Materialeigenschaften, des strukturellen Designs und der Prozessparameter. Nach der bruchmechanischen Analyse können Radrisse in drei Haupttypen unterteilt werden:
- Thermische Rissbildung (Erstarrungsfehler)Er tritt meist an der Speichen-Felgen-Verbindung auf und äußert sich als netzartiger Riss, der sich entlang der Korngrenzen verteilt. Der Grund dafür ist, dass das verbleibende flüssige Metall zwischen dem dendritischen Skelett am Ende der Erstarrung der Schrumpfspannung nicht standhalten kann. Typische Fälle zeigen, dass die Wahrscheinlichkeit der thermischen Rissbildung um 60% steigt, wenn die lokale Abkühlungsgeschwindigkeit 4°C/s übersteigt.
- Kaltrissbildung (mechanische Belastung)Der Bruch tritt in der Regel an der Wurzel des Nabenflansches auf und weist typische Sprödbrucheigenschaften auf. Die Versagensanalyse einer Nutzfahrzeugnabe ergab, dass das erstarrte Metall, das während der Entformung im Hubrohr verblieb, das Gussteil einer Zugspannung von mehr als 200 MPa aussetzte, was direkt einen durchdringenden Riss auslöste.
- Spannungsrisskorrosion (Wechselwirkung mit der Umwelt)In küstennahen Umgebungen mit hoher Luftfeuchtigkeit wirken Eigenspannungen in der Nabe synergetisch mit Chloridionen, so dass sich Risse langsam entlang der Korngrenzen ausbreiten. Solche Risse zeigen bei mikroskopischer Betrachtung eine ausgeprägte dendritische Bifurkationsmorphologie.
Systematische Analyse der wichtigsten Fracking-Faktoren
1. mechanische Verstärkung von Konstruktionsfehlern
- Spannungskonzentration an scharfen EckenWenn der Radius der inneren Verrundung im Speichenübergangsbereich weniger als 3 mm beträgt, kann der Spannungskonzentrationsfaktor (Kt) 3,5 bis 4,2 erreichen und damit die Streckgrenze der Aluminiumlegierung A356-T6 (220 MPa) weit übersteigen. Die Simulationsdaten eines Sportrads zeigen, dass nach der Optimierung des R-Winkels von 2mm auf 5mm die maximale Vergleichsspannung von 315MPa auf 185MPa reduziert wird.
- WanddickenmutationseffektWenn der Unterschied in der Wanddicke zwischen benachbarten Bereichen 3:1 übersteigt, kann der während des Abkühlungsprozesses erzeugte thermische Spannungsgradient die Grenze der Materialzugfestigkeit durchbrechen. Der Bruchfall einer leichten Radnabe zeigt, dass die Dicke der Felgen-Speichen-Verbindung von 8 mm auf 3 mm reduziert wurde, was zu einer lokalen Spannungsspitze von 280 MPa führte.
2) Systemisches Risiko einer Fehlanpassung der Prozessparameter
- Enges Zeitfenster zum Halten des DrucksHaltezeit: Eine Haltezeit von weniger als 15 Sekunden führt zu einer Unterbrechung der Schrumpfung und zur Bildung von Schrumpfungslockerungen, während eine Haltezeit von mehr als 40 Sekunden einen mechanischen Widerstand gegen die Erstarrung des Metalls im Steigrohr erzeugt. Ein Projekt-DOE-Test bestätigte, dass die Rissrate von 7,2% auf 0,8% sinkt, wenn die Haltezeit im Bereich von 25-30 Sekunden gesteuert wird.
- Unsachgemäße Kontrolle der FüllmengeWenn die Füllgeschwindigkeit 120 mm/s übersteigt, erhöht sich die Wahrscheinlichkeit von turbulenten Gaswalzen im flüssigen Metall um 40%, und die mikroskopischen Defekte, die durch Gasretention gebildet werden, werden zum Ausgangspunkt der Rissbildung. Der Step-up-Prozess (anfänglich 0,03MPa, abschließend 0,06MPa) kann die Füllgeschwindigkeit und das Risiko von Gasblasen wirksam ausgleichen.
3. die Herausforderungen des dynamischen Gleichgewichts beim Wärmemanagement von Formen
- unkontrollierbares TemperaturgefälleWenn die Temperaturdifferenz der Form 50℃ übersteigt, überschreitet die Erstarrungsschrumpfungsdifferenzrate jeder Region des Gussteils 0,8%, was zu thermischen Rissen führt. Eine Fabrik durch die Implantation der Form Temperaturüberwachungspunkt festgestellt, dass die Temperaturschwankung in der Speiche Bereich bis zu ± 30 ℃, nach der Installation der Partition Temperaturkontrollsystem Temperaturdifferenz ist stabil innerhalb ± 5 ℃.
- Falsche Auswahl des KühlmediumsTraditionelle Wasserkühlung ist leicht zu einem plötzlichen Rückgang der Oberflächentemperatur der Form, die Verwendung von Aerosol gemischte Kühlung Technologie kann genau steuern, die Abkühlgeschwindigkeit von 3-8 ℃ / s, um die Abschreckung Stress durch die schnelle Abkühlung zu vermeiden.
Ingenieurtechnische Lösungen zur Rissvermeidung
1. optimiertes System für die Dynamik von Aufzugssystemen
- Rekonstruktion der KufengeometrieDer Durchmesser des Heberohrs wurde von Φ60mm auf Φ85mm vergrößert, und mit dem 30° geneigten Kanal wurde die Durchflussgeschwindigkeit der Metallflüssigkeit auf 0,8-1,0m/s stabilisiert. Die Praxis eines Projekts zeigte, dass diese Maßnahme die Wahrscheinlichkeit des Einfrierens des Heberohrs um 70% reduzierte.
- Verbesserungen der IsolierungDie Verwendung einer nanoporösen Wärmekonservierungshülse (Wärmeleitfähigkeit ≤ 0,1 W/m-K) verlängert die Wärmekonservierungsdauer um 40% im Vergleich zum herkömmlichen Keramikfasermaterial, um die Glattheit des Schrumpfkanals zu gewährleisten.
2. bionischer Optimierungspfad für den Strukturentwurf
- Stress Flow Mapping TechnologieUmverteilung der Speichenmaterialien auf der Grundlage von Algorithmen zur Topologieoptimierung, um die Hauptbelastungsrichtung mit der Ausrichtung der Verstärkung in Einklang zu bringen. Ein leichtes Rad hat durch diese Technik 12% an Gewicht verloren, während die Biegesteifigkeit um 18% erhöht wurde.
- GradientenwechselregelDie Entwicklung einer 1:4 konischen Übergangszone im Bereich der Wanddickenänderung und das Hinzufügen von Spannungsentlastungsrillen mit einer Tiefe von 1,5 mm an der Speichenwurzel führten zu einer Reduzierung der lokalen Spannungsspitze von 295 MPa auf 175 MPa.
3. intelligentes Temperaturkontrollsystem für die Form
- Gekoppelte Mehrzonen-TemperaturregelungEntwicklung eines unabhängigen Sechs-Zonen-Temperaturregelungsmoduls, bei dem die Felgenzone auf 320 °C (zur Förderung der Make-up-Schrumpfung) und die Speichenzone auf 280 °C (zur Verhinderung thermischer Rissbildung) eingestellt ist. Bei der Massenproduktion eines hochwertigen Markenrads kann mit diesem System eine gleichmäßige Formtemperatur von ±3℃ erreicht werden.
- Dynamische KühlungsstrategieDie Luftkühlung wird zur Aufrechterhaltung der Formtemperatur während der Füllphase verwendet, und die Nebelkühlung wird zur Beschleunigung der Erstarrung während der Haltephase eingeschaltet, wodurch der gesamte Produktionszyklus um 8 Sekunden verkürzt wird.
Praktiken der Prozessinnovation bei Ningbo Hexin
In der Zusammenarbeit mit einer deutschen Luxusmarke hat das Team von He Xin durch drei wichtige technologische Durchbrüche den Maßstab für die Branche gesetzt:
- Niederdruck-Gieß-Spinn-VerbundumformungstechnologieÜberlagertes Drückverfahren im Felgenbereich, so dass die Maserung entlang des Umfangs ausgerichtet ist, erhöht die radiale Schlagzähigkeit der Radnabe um 35%.
- Gradientenheizsystem (patentierte Technologie)Die Oberfläche der Form ist mit einer 0,2 mm dicken Titannitridbeschichtung versehen, die zusammen mit der Induktionsheizvorrichtung eine präzise Temperaturregelung mit einem Temperaturunterschied von ≤5℃ im Speichenbereich ermöglicht.
- Plattform für digitale ProzesssimulationIntegration von MAGMAsoft und ANSYS: Durch die Integration von MAGMAsoft und ANSYS wird die Anzahl der Formversuche von 12 auf 3 reduziert, wodurch sich der Entwicklungszyklus um 60% verkürzt.
Die Wahl der richtigen Niederdruck-Gießradanlage
Es gibt vier Kernkompetenzen, über die ein Qualitätsanbieter verfügen muss:
- Material-DatenbankAkkumulation von Zehntausenden von Sätzen von Prozessparametern und Legierungseigenschaften, die die Beziehung abbilden, schnelle Anpassung der besten Materiallösungen
- Qualitätskontrolle des gesamten ProzessesFestlegung von 12 Qualitätskontrollpunkten von der Analyse der Barrenreinheit (Fe-Gehalt ≤ 0,15%) bis zur Röntgenfehlererkennung (ASTM E505-Norm).
- flexible ProduktionSchnelles Werkzeugwechselsystem, kompatibel mit 16-24-Zoll-Rädern, Umrüstzeit <45 Minuten
- grüne ProduktionDie Verwertungsquote von Aluminiumspänen liegt bei ≥95%, der Energieverbrauch pro Produkteinheit ist um 28% niedriger als der Branchendurchschnitt.
Häufig gestellte Fragen und Antworten
1) Warum sind Niederdruck-Gussräder besser für neue Energiefahrzeuge geeignet?
Seine hohe Verdichtung kann dem momentanen Drehmoment des Motors (≥3000N-m) standhalten, während das geringe Gewicht (40% Gewichtsreduktion gegenüber Stahlrädern) die Reichweite direkt um 5%-8% verbessert.
2) Wie kann die Ursache von Rissen durch metallographische Analyse bestimmt werden?
- Thermische Rissbildung: Vorhandensein einer durchgehenden Oxidschicht an den Korngrenzen, Risse in Form eines Zickzack-Netzwerks
- Kaltbruch: der Bruch ist gerade, es sind deutliche Auflösungsstufen sichtbar
- Spannungskorrosion: Vorhandensein von elementarer Cl-Anreicherung an der Rissspitze (EDS-Nachweis)
3. wie wirkt sich die Lebensdauer der Form auf die Rissrate aus?
Wenn die Form für mehr als 5.000 Formzyklen verwendet wird, können Mikrorisse in der Oberfläche zu einem Anstieg der Gussablösungsbeständigkeit von 25% führen, was eine regelmäßige Reparatur des Laserplattierens erfordert (Wiederherstellung der Oberflächenhärte auf HRC 45 oder höher).
4) In welche Richtung geht die technologische Entwicklung in Zukunft?
Künstliche Intelligenz wurde in die Prozessoptimierung eingeführt, wobei Algorithmen des maschinellen Lernens die Druckkurve in Echtzeit regulieren, mit dem Ziel, die Crackrate auf unter 0,11 TP3T zu senken und gleichzeitig die Produktivität um weitere 201 TP3T zu erhöhen.