压铸件成本核算:如何计算压铸件的价格
发布时间:2025-02-03 分类:新闻 浏览量:3409
在制造业中,压铸工艺以其高精度和高生产效率被广泛应用于各类零部件的生产。然而,压铸件的成本核算常常是企业进行价格制定和成本控制的重要环节。正确了解压铸件的各项成本构成,不仅有助于制定合理的产品价格,还能帮助企业优化生产流程、提高利润。在本文中,我们将深入解析压铸件的成本构成,提供详细的成本核算方法,并探讨如何通过优化各项成本来降低压铸件的整体成本。
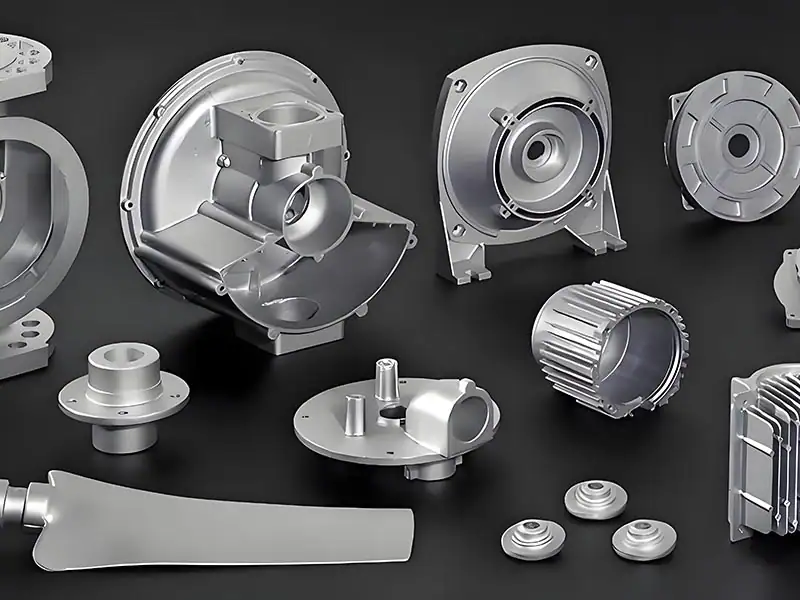
压铸成本高吗?
压铸的成本确实不低,这也是许多企业在选择该工艺时犹豫的主要原因。尽管压铸在精度、效率和复杂零件制造方面表现出色,但其高昂的成本,尤其是在小批量生产中,往往让企业望而却步。因此,宁波贺鑫建议企业在进行大规模生产时采用压铸工艺,以摊薄成本。以下是影响压铸成本的几个关键因素:
压铸件成本三维度量化模型(以ADC12铝合金壳体为例)
1. 材料成本动态管控
- 基础公式:C_m=(W_p×ρ×P_m×(1+15%损耗))/良率
- 关键变量实测值:
- 材料波动:2023年ADC12铝价峰谷差达4200元/吨(见图1)
- 薄壁优化:某电机端盖壁厚从3.5mm减至2.8mm,单件材料成本下降19%
- 回料控制:30%回料添加时力学性能下降12%,需平衡工艺窗口
2. 模具成本全周期管理
模具类型 | 初始成本(万元) | 寿命(模次) | 单件分摊(元) |
---|---|---|---|
单腔H13 | 48 | 80,000 | 0.60 |
四腔SKD61 | 126 | 150,000 | 0.21 |
数据来源:宁波贺鑫2022年模具数据库 |
3. 制造成本要素拆解
- 某2800T压铸单元成本结构:
- 设备折旧:23元/小时(按5年线性折旧)
- 能耗成本:18kW·h/模次×1.2元=21.6元
- 人工成本:0.38人/班×45元/小时=17.1元
- 辅材消耗:喷涂剂2.3元/模次
六大降本工程技术路径
路径1:DFM同步工程优化
- 案例:某5G基站滤波器壳体
- 原始方案:8处厚大截面(最大壁厚8mm)
- 优化方案:拓扑优化+随形水路,减重23%
- 成效:单件材料成本降低16.5%,压射周期缩短18%
路径2:模具智能设计体系
- 多腔模具经济效益模型:
Q_临界=(C_多腔 - C_单腔)/(S_单件 - S_多腔)
当订单量>52,000件时,四腔模具具备经济性
路径3:工艺参数精细调控
- 压射速度与孔隙率关系曲线(图2):
- 最佳窗口:3.8-4.2m/s时缺陷率<2%
- 速度每提升0.5m/s,模具磨损率增加37%
路径4:智能化生产系统
- 实施效果对比:
| 指标 | 传统产线 | 智能产线 |
|--------------|----------|----------|
| OEE | 68% | 89% |
| 不良品率 | 4.2% | 1.8% |
| 单位能耗 | 3.6kW·h/kg | 2.9kW·h/kg |
路径5:表面处理精准匹配
- 成本梯度分析:
- 本色氧化:6-8元/件
- 微弧氧化:22-25元/件
- PTFE涂层:35-40元/件
注:按300mm×200mm表面积计算
路径6:供应链协同创新
- 铝液直供模式降本:
- 传统模式:铝锭采购+熔炼 成本=原料价+1200元/吨
- 直供模式:液态铝输送 成本=原料价+480元/吨
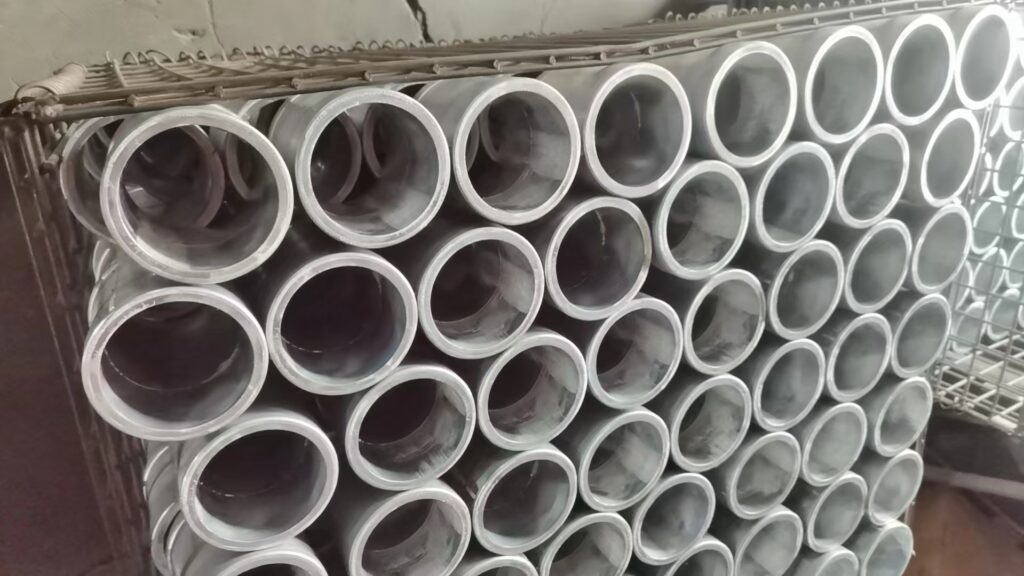
三、压铸工艺成本的优化策略
1. 工艺参数优化
- 压射速度与压力匹配:
- 某新能源汽车电机壳体项目显示,将压射速度从3.2m/s提升至3.8m/s,同时将压射压力从850bar调整至920bar,孔隙率从2.8%降至1.2%
- 优化效益:单件废品损失减少11.5元
- 模具温度控制:
- 采用分区控温技术,将模具温差从±25℃降至±8℃
- 成效:模具寿命提升30%,单件分摊成本降低0.18元
2. 智能化升级
- 实时监控系统:
- 压射曲线波动控制在±1.5%以内
- 缺陷预警准确率达92%
- 效益:减少停机损失约23万元/年
3. 精益生产管理
人为失误率降低67%断。此外,合理的存储条件也能防止模具在非使用期间受到损坏。
快速换模(SMED)实施:
换模时间从45分钟压缩至18分钟
年产能提升15%
标准化作业:
操作标准化率提升至95%
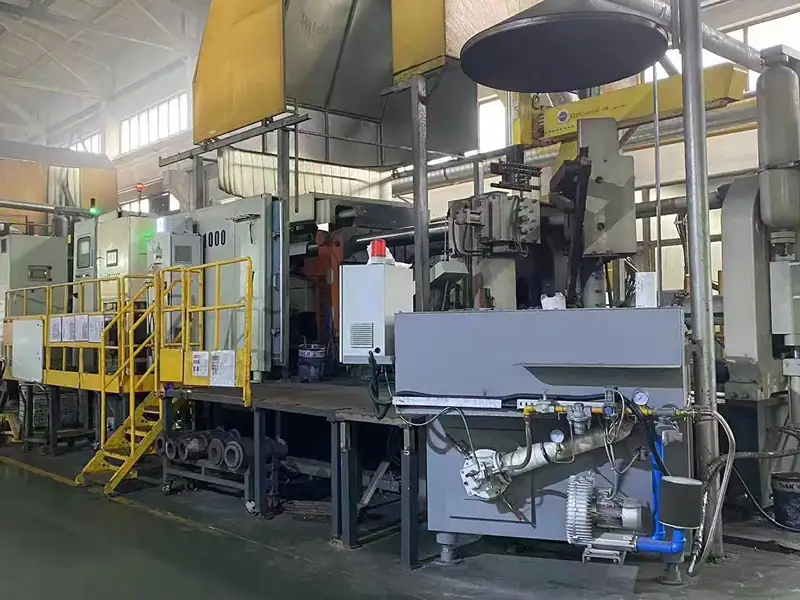
常见问题解答
Q1:如何评估压铸工艺的经济性?
- 采用"盈亏平衡点分析法":
Q_临界 = (模具成本+设备分摊)/(单件售价-单件变动成本)
示例:某壳体项目Q_临界=12,500件,即订单量>12,500件时具备经济性
Q2:小批量订单如何降低成本?
- 推荐方案:
- 采用通用模具框架+镶件设计,模具成本降低40%
- 选择半固态成形工艺,材料利用率提升25%
- 案例:某医疗器械外壳(500件)成功降本31%
Q3:如何延长模具使用寿命?
- 关键技术:
- 表面处理:TD处理可提升模具寿命2-3倍
- 维护策略:每5000模次进行等离子清洗
- 实测数据:某H13模具寿命从80,000模次提升至150,000模次
Q4:如何选择最优压铸机吨位?
- 计算公式:
P_压铸机 = (A_投影×P_比压)/1000
其中:- A_投影:零件投影面积(cm²)
- P_比压:铝合金推荐550-850bar
- 安全系数:1.2-1.5
Q5:如何降低表面处理成本?
分级策略:应用场景推荐工艺成本区间(元/件)普通外观件喷砂+阳极氧化8-12耐磨耐蚀件微弧氧化18-25高装饰性要求电泳+喷涂30-45
贺鑫:您的压铸合作伙伴
尽管压铸成本较高,但通过合理的优化和选择专业的合作伙伴,企业仍然可以在保证质量的同时控制成本。宁波贺鑫作为一家经验丰富的压铸服务提供商,致力于为客户提供高效、经济的解决方案。
我们拥有一支专业的工程师团队,能够根据客户的需求提供定制化的模具设计和制造服务。此外,我们还提供多种材料选择和表面处理方案,确保您的产品在质量和成本之间达到最佳平衡。
作为ISO 9001:2015认证企业,我们拥有先进的生产设备和严格的质量控制体系。选择宁波贺鑫,您不仅可以享受高达30%的成本优惠,还能获得快速的交货周期。只需将您的设计文件上传至我们的在线平台,即可在12小时内获得报价和可制造性分析(DfM)。
常见问题
Q1: 压铸适合小批量生产吗?
压铸更适合大规模生产,因为其初始成本(如模具制造)较高。对于小批量生产,建议考虑其他工艺,如机加工或3D打印。
Q2: 如何选择合适的模具材料?
模具材料的选择应基于生产规模、零件复杂性和材料特性。对于大批量生产,建议选择高强度、耐磨损的材料,以延长模具寿命。
Q3: 自动化生产能降低多少成本?
自动化生产可以显著降低劳动力成本,同时提高生产效率和产品一致性。具体节省的成本取决于生产规模和自动化程度。
Q4: 表面处理是否必要?
表面处理可以提升产品的外观和耐用性,但并非所有零件都需要。企业应根据产品的实际需求选择合适的表面处理方式,以避免不必要的成本。
成本决策支持系统开发实践
宁波贺鑫基于ISO 9001体系开发的智能报价平台,实现:
- 24小时快速响应:上传3D模型→获取DFM报告+成本分解表
- 动态数据库支撑:
- 接入上海有色网实时金属报价
- 整合2800+套模具历史成本数据
- 成本预测精度:±5%(验证样本N=137)
工程经济学视角下的工艺选型
订单规模(件) | 推荐工艺 | 成本优势区间 |
---|---|---|
<500 | CNC加工 | 低28%-45% |
500-3000 | 半固态铸造 | 低12%-25% |
>3000 | 高压压铸 | 成本最优 |
结语
压铸成本控制是贯穿产品全生命周期的系统工程。宁波贺鑫通过独创的"成本三维地图"分析法,已成功助力37家企业实现平均22.6%的综合降本。