How many types of aluminum corrosion are there?
Date: 2025-05-12 Categories: Blog Views: 1398
Types of Aluminum Corrosion
1. Atmospheric corrosion
The most common form of aluminum corrosion. Atmospheric corrosion of aluminum occurs as a result of exposure to natural elements. Because of its likelihood of occurring in most places, atmospheric corrosion accounts for the largest share of the total damage to aluminum caused by all types of corrosion combined in the world.
Atmospheric corrosion can be divided into three subcategories. They are dry, wet and humid, depending on the humidity level of the service environment.
- dry corrosion(Humidity <30%): Only slow chemical oxidation occurs;
- wetting corrosion(Humidity 30%-60%): Localized galvanic corrosion initiated by a thin liquid film;
- galvanic corrosion(Humidity > 60%): thick liquid film accelerates ion migration and corrosion rate increases significantly.
Since moisture levels can vary greatly depending on your geographic location, certain areas will experience greater corrosion than others.
Other environmental factors affecting the extent of atmospheric corrosion are changes in wind direction, temperature and precipitation. The concentration and type of pollutants in the air and proximity to large bodies of water also play an important role.
2. Galvanic corrosion
Galvanic coupling corrosion, also known as dissimilar metal corrosion, affects aluminum when it is attached to a noble metal, either physically or through an electrolyte. The precious metal can be any metal that has a lower reactivity compared to aluminum.
The reactivity of a metal depends on its position in the electrochemical series. If another metal in the electrochemical series is further away from the aluminum, the severity of the corrosion will be more severe.
Corrosion strength is highest at the intersection where the two metals meet and decreases as you move away from that interface.
For example, if aluminum and brass are in contact or even close to each other and placed in seawater, a primary cell is formed. The aluminum part will then corrode because it acts as the anode (positive terminal).
This can be a problem in boats where brass fittings may be close to aluminum fittings while they are both immersed in seawater. Electrons flow from aluminum to brass through seawater.
This type of primary cell may inadvertently form and cause galvanic coupling corrosion in other service environments. Galvanic coupling corrosion is much faster than normal atmospheric corrosion.
- Potential difference > 0.2Voccurred significantly at the time and the corrosion rate was positively correlated with the cathode/anode area ratio;
- Typical scenario: Aluminum components and brass fittings in ships conduct through seawater, with aluminum as the anode corroding up to 0.5mm per year, a 20-fold improvement over the isolated state;
- Protection strategy: isolate dissimilar metals with insulating spacers, or anodize the aluminum surface.
3. Pitting
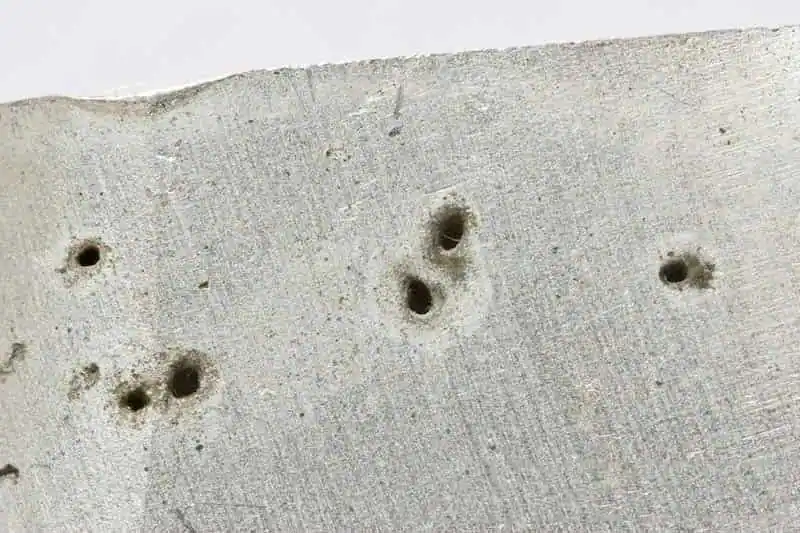
Pitting is a surface corrosion phenomenon characterized by the appearance of small holes (pits) on the surface of aluminum metal. Usually, these pits do not affect the strength of the product. Instead, it is an aesthetic issue, but can lead to failure if surface appearance is critical.
Pitting corrosion usually occurs in areas where salts are present in the atmosphere, as the presence of chloride anions is responsible for it. Sulfates also cause pitting corrosion to some extent. The worst case of pitting corrosion is observed in the presence of alkaline and acidic salts.
trigger condition:
- Chloride ion (Cl-) concentration > 0.5 mol/L;
- The presence of inclusions or grain boundary defects on the surface;
- The alloy potential is higher than the local breakdown potential (>0.4V vs SCE).
Extension Mechanisms: - Hydrolysis of Al³⁺ in the etching holes produces acid (pH down to 2-3) and Cl- enrichment forms an autocatalytic cycle;
- The growth rate of hole depth can be up to 0.1mm/month, and the depth-to-width ratio is often >10:1.
For pitting to occur, the potential of the alloy must be higher than the potential of the electrolyte (salt solution). The presence of surface defects at grain boundaries and second phase particles is a precursor to pitting.
4. crevice corrosion
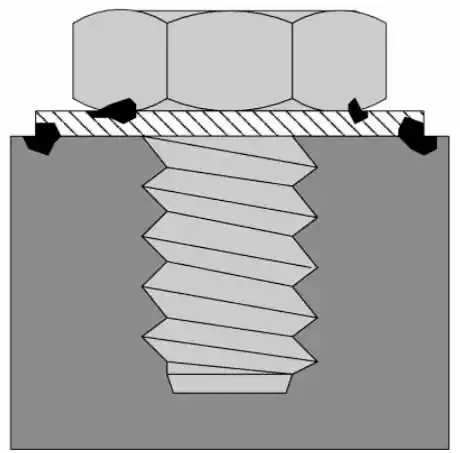
Crevice corrosion is a form of localized corrosion process in materials. Overlapping materials or unintentional design errors can lead to the formation of crevices. As a result, the collection of seawater into these pockets can lead to crevice corrosion.
Even a small gap between the bolt and the structure is enough to start this type of corrosion. Over time, the aluminum in the material dissolves and precipitates into the seawater. This ionized aluminum absorbs oxygen from the surrounding air and hydroxide ions from the electrolyte, forming aluminum hydroxide.
Geometrically restricted areas (e.g., flange seams, rivet gaps) form occlusion cells due to differences in oxygen diffusion:
- beginning period: The difference in oxygen concentration inside and outside the gap drives aluminum dissolution (Al→Al³⁺+3e-);
- development period: Hydrolysis of Al³⁺ leads to a decrease in pH and Cl- migration to concentration;
- plateau: maintains a strongly corrosive microenvironment at pH ≈ 2, with the greatest hazard at a gap width of 0.1-0.5 mm.
In the presence of chlorides, this oxygen reduction makes the crevices acidic, which accelerates the rate of corrosion.
5. Intergranular corrosion
For aluminum, the grain boundaries are electrochemically different compared to the alloy microstructure. This leads to the establishment of an electrochemical potential and electron exchange between the two.
There are several variations of intergranular corrosion based on thermochemical treatment and metal structure. In different series ofaluminumIt is also found in varying degrees in For example, alloys of the 6xxx series are relatively insensitive to this type of aluminum corrosion.
The anode path will vary with different alloy systems. In the 2xxx series it appears as a narrow band on either side of the grain boundary, while in the 5xxx series it appears as a continuous path along the grain boundary.
The phenomenon of preferential dissolution along grain boundaries stems from tissue heterogeneity:
- Department of 2xxx: CuAl₂ precipitation at grain boundaries leads to a copper-poor zone (anode);
- Department of 5xxx: Selective dealloying triggered by a continuous β-phase (Mg₂Al₃);
- defend: T6 aging treatment reduces the depth of grain boundary corrosion by 80%.
Like pitting, intergranular corrosion begins with pitting. However, it propagates faster along susceptible grain boundaries.
6. Spalling corrosion
Spallation corrosion is a specific type of intergranular corrosion found in aluminum alloys with a distinctly oriented structure. This is particularly evident in aluminum products that have undergone the hot or cold rolling process.
It occurs along elongated grain boundaries in the microstructure. The term spalling comes from the fact that the corrosion products are much larger and give the impression of lifting from the surface of the material.
This type of aluminum corrosion extends above the surface and builds stress laterally in the product. In turn, this results in an initial wedging action at the surface before migrating into the body of the product. Severe delamination occurs and the material weakens. Surface degradation such as pitting, spalling and blistering may occur.
The 2xxx, 5xxx and 7xxx series are more susceptible to exfoliation corrosion due to their highly oriented grain structure. This makes the grain boundaries more sensitive to intergranular corrosion. Laminar corrosion in rolled sheet due to anisotropic organization:
EXCO solution accelerated test for 48h can simulate the degree of natural corrosion for 10 years.
Volume expansion of corrosion products (Al→Al(OH)₃ volume increase by a factor of 6.3) triggers interlayer stresses (>100 MPa) in the parallel rolling direction;
Susceptibility to exfoliation corrosion can be altered by redistributing the precipitates using heat treatments.
7. General corrosion
When corrosion occurs almost uniformly on the surface of an aluminum product, it is uniform or total corrosion.
This corrosion occurs when products are frequently exposed to strongly acidic or alkaline media. It may also occur in the presence of high electrochemical potentials when the product is in an electrolyte. A typical example is the rusting of aluminum plates in acidic solutions.
Uniform corrosion is the result of continuous movement of the anode and cathode regions in contact with the electrolyte and manifests itself as uniform corrosive attack on the surface.
The oxide layer is also unstable in high and low pH solutions and does not protect the metal underneath. The thickness of the material decreases and eventually dissolves completely.
Attacks are not entirely consistent and there will be peaks and valleys. There are no small areas of deep corrosion sufficient to call this a general example of corrosion.
The passivation film is completely dissolved in strong acid (pH 9) environments:
- corrosion rate: >1.2 mm/year at pH 9;
- Concentrated nitric acid (65%) reduces the rate to 0.001 mm/year due to strong passivation.
8. Depositional corrosion
Deposition corrosion occurs when dissimilar metals are deposited on an aluminum surface resulting in severe localized corrosion.
Imagine water flowing through a copper pipe. As the water flows through, it absorbs copper ions. These copper ions are now in solution. When that solution comes into contact with an aluminum surface or container, it deposits these copper ions on it.
These ions now form a subtle protocell, and if the ion is low in the electrochemical or protocell series, it will corrode the aluminum by pitting. The greater the difference between the aluminum and the electrically coupled deposited ions, the more severe the corrosion.
Even solutions of copper ions at a concentration of 1 ppm have been known to cause severe corrosion of aluminum surfaces.
Metals that can cause corrosion of aluminum deposits are called "heavy metals". Some important heavy metals are copper, mercury, tin, nickel and lead.
The passivation film is completely dissolved in strong acid (pH 9) environments:
- corrosion rate: >1.2 mm/year at pH 9;
- Concentrated nitric acid (65%) reduces the rate to 0.001 mm/year due to strong passivation.
The corrosion caused by this method is more pronounced in acidic solutions compared to alkaline solutions. This is due to the low solubility of these ions in alkaline solutions.
9. Stress Corrosion Cracking (SCC)
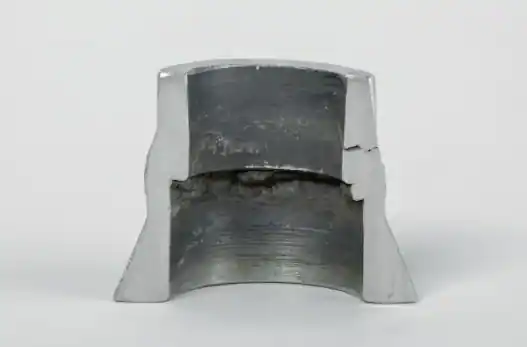
Stress Corrosion Cracking (referred to here as SCC) is a form of intergranular corrosion that can lead to complete failure of aluminum parts.
Three conditions need to be met for this corrosion to occur. Sensitive alloys are the first of these. Not all aluminum alloys are equally susceptible to SCC. high yield strength alloys are more susceptible to stress corrosion cracking.
The second condition is that the environment in which it is to be used must be wet or humid. The third condition is the presence of tensile stress in the material. This tensile stress is the cause of crack propagation and its propagation through the metal.
triptych: Sensitive alloys (e.g. 7075-T6), tensile stress (> yield strength 30%), corrosive media (Cl-solution):
- Crack type: along the grain (IGSCC) or through the grain (TGSCC);
- The critical stress intensity factor (KISCC) can be reduced to 30% of conventional strength.
There are two types of SCC processes. The first is intergranular stress corrosion cracking (IGSCC), in which cracks propagate along grain boundaries. The second is through-grain stress corrosion cracking (TGSCC), in which the cracks propagate through the grains rather than along the grain boundaries.
10. Erosion corrosion
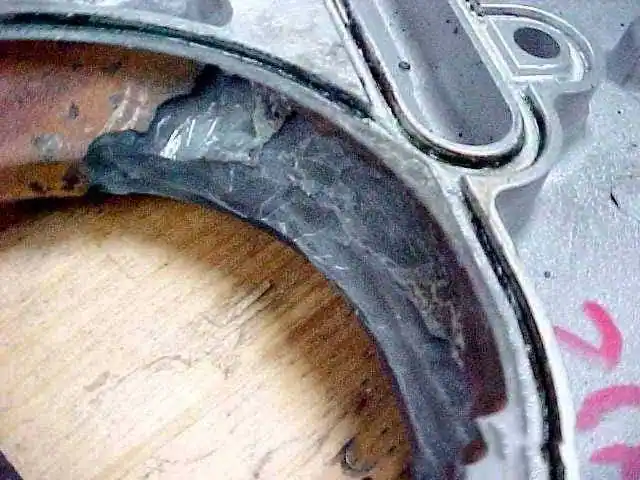
Erosion corrosion of aluminum is caused by the impact of high velocity water jets on the aluminum body.
Two factors that exacerbate erosion-corrosion are the flow rate of the water and its pH. The presence of carbonate and silica content in the water further increases the rate of corrosion.
In pure water, aluminum corrosion proceeds at a slow rate. However, this rate increases when the pH exceeds 9. In acidic water, corrosion is even faster.
Fluid dynamics and chemical corrosion synergize:
- High velocity water flow(>5m/s) destroys the passivation film;
- a sandy fluidInduced abrasion-corrosion interaction damage;
- collapse of vacuoleGenerates >1GPa impact pressure resulting in surface flaking.
Erosion-corrosion can be prevented by controlling the above factors. Erosion-corrosion can be significantly reduced by either reducing water velocity, maintaining water quality, or both. Improving water quality means keeping the pH as close to neutral (<9) as possible and reducing silica and carbonate levels.
11. Corrosion fatigue
It is well known that fatigue can lead to complete product failure if left unchecked. In the case of aluminum, fatigue cracking can act as an initiation point for pitting corrosion.
Corrosion fatigue occurs when aluminum is repeatedly subjected to low stresses over long periods of time. In corrosive environments such as seawater and salt solutions, crack initiation and expansion are more likely to occur.
Synergistic reduction of fatigue limit by alternating loads and corrosive media:
- 3.5% NaCl solution, the fatigue life of the 2024-T3 aluminum alloy drops to 10% in a dry environment;
- The crack extension rate is regulated by ΔK (stress intensity factor amplitude) in conjunction with frequency (critical threshold of 10 Hz).
Corrosion fatigue cannot proceed if water is not present in the atmosphere. It is also largely independent of the direction of stress, since crack propagation is primarily through the crystal. Thus, unlike in the case of SCC, stress does not affect its propagation.
12. Filamentary corrosion
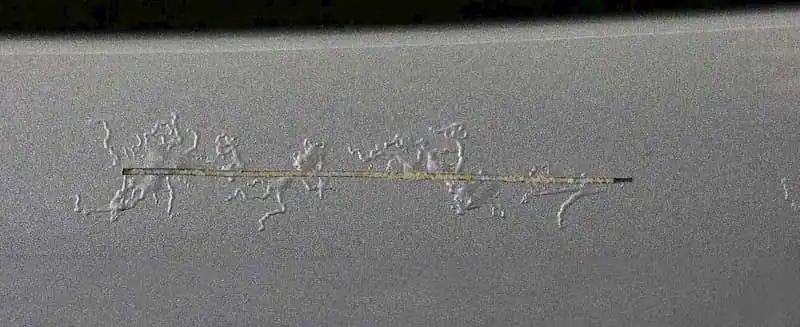
Filamentary or worm corrosion begins as pitting. It begins at the point where the paint peels off the aluminum surface. The cause may be a scratch or abrasion on the surface that exposes the metal surface underneath.
In the presence of chloride anions and high humidity, filiform corrosion can easily occur and spread. Although it begins as salt water pitting, it spreads as crevice corrosion.
The head of the earthworm is acidic and has a high chloride content. It absorbs oxygen and acts as an anode. The second half of the worm track acts as a cathode and a reaction ensues.
Self-propelled corrosion formed at coating defects:
- The acidic zone in the head (pH ≈ 1-2) and the alkaline zone in the tail (pH ≈ 10-12) form an electrochemical gradient;
- Extension rate 0.1-0.5 mm/day, path controlled by matrix weave.
Filamentary corrosion can be prevented by keeping the surface undamaged and sealing all small gaps with paint or wax. If feasible, the relative humidity of the environment must be reduced.
13. Microbial corrosion(MIC)
Microbial Induced Corrosion or MIC is corrosion caused by microorganisms/fungi. This type of corrosion is common in fuel and lube oil tanks.
Microorganisms and fungi can thrive in the presence of water in oil. Some of these organisms are able to consume the oil and excrete acids that can cause corrosion of aluminum containers used for storage.
This acid can cause pitting in aluminum containers and eventually lead to leaks.
triggered by microbial metabolism such as sulfate-reducing bacteria (SRB):
- The anaerobic environment produces H₂S to destroy the passivation film;
- Biofilms form oxygen concentration cells;
- The water phase separation area of the fuel system is a high incidence area that requires regular draining and addition of biocide.
To prevent this, the oil must be purified to remove as much water as possible. Regular draining from the tank after purification is also necessary. If it is not possible to improve the quality of the fuel, germination can be prevented by the use of biocides.