A380 aluminum alloy composition and physical properties analysis
Date: 2025-05-08 Categories: Blog Views: 1566
As an efficient solution in the die casting sector, the A380 model aluminum It is the most common type of die cast aluminum because it combines the properties of easy molding, easy machining, and good heat transfer. Shiftability, load-bearing capacity, and resistance to high-temperature splitting are all very high, and although type A380 has long been considered easy to machine, its high silicon content makes it slightly rough. It is utilized in a wide variety of products including motor equipment chassis, engine mounts, gearboxes, furniture, generators, and hand tools. The following comparison of specialized data visualizes its core technical parameters:
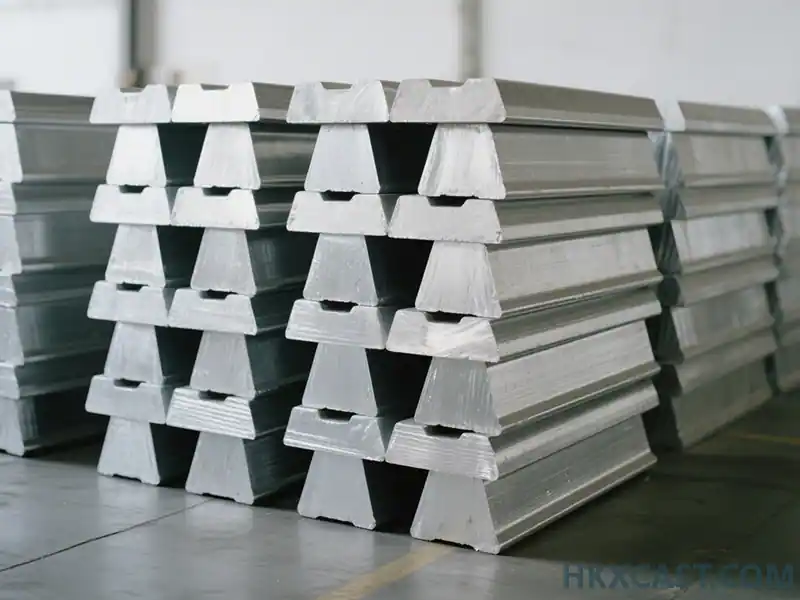
A380 Aluminum Alloy Composition Table
elemental | Content range (wt%) | functional role |
---|---|---|
Aluminum (Al) | 85.0-89.5 | Substrate materials to ensure a lightweight base |
Silicon (Si) | 7.5-9.5 | Improved flow and abrasion resistance |
Copper (Cu) | 3.0-4.0 | Enhanced high temperature strength and hardness |
Iron (Fe) | ≤1.2 | Control of intermetallic compound formation |
Zinc (Zn) | ≤3.0 | Improved corrosion resistance |
A380 Physical Property Parameter Table
Performance indicators | Numerical range | Cross reference (mild steel) |
---|---|---|
intensity | 2.71 g/cm³ | 7.85 g/cm³ |
Tensile strength (T6 state) | 310-330 MPa | 400-500 MPa |
elongation | 2.5-3.5% | 15-25% |
heat conductivity | 96 W/(m-K) | 50 W/(m-K) |
Coefficient of linear expansion | 21.8 μm/(m-°C) | 11.7 μm/(m-°C) |
A380 Aluminum Alloy Application Scenario Analysis
1. Automotive Manufacturing
- mechanical system: Engine mounts, gearbox housings (weight reduction 30%-50%, temperature resistance up to 200°C)
- New Energy Vehicle Core: Integrated Battery Tray (Reduces soldering points 40%, improves assembly efficiency)
- security structure: Crash energy absorption box (energy absorption rate higher than steel 25%-30%)
2. electronic equipment
- thermal module: 5G base station heat sink (thermal conductivity of 96W/(m-K), 2 times higher efficiency)
- Precision construction: Drone frame (wall thickness can be die-cast up to 1.2mm, accuracy ±0.1mm)
3. Industrial equipment
- hydraulic system: Pump valve casing (pressure strength >300MPa, life extension 20%)
- automation: Robotic arm joint (lightweight design reduces motor load by 15%)
A380 Aluminum FAQ
Q1: What should I do if the surface of A380 aluminum alloy is rough when machining?
- prescription:
① Control silicon content in the optimized range of 8.5%-9.2%
② AdoptionVacuum Die Casting Process(Porosity <0.3%)
③ Follow-up sandblast or CNC finishing (roughness Ra≤1.6μm)
Q2: Why is the A380 more heat resistant than ordinary aluminum alloys?
- Technical Principles:
- Copper elements (3%-4%) form Al₂Cu reinforced phases to enhance high-temperature strength.
- Elemental silicon reduces the coefficient of thermal expansion to 21.8 μm/(m-°C)
- Measured data: tensile strength retention rate at 150℃>85%
Q3:How to improve the thin-walled parts die-casting easy to break?
- process optimization:
- Mold temperature control at 200 ± 10 ℃ (to avoid rapid cooling embrittlement)
- Add 0.05%-0.15% titanium to refine the grain size
- Heat treatment using the T5 process (20% strength gain, 3.5% elongation)
Q4: Does A380 corrosion resistance meet outdoor use?
- protection strategy:
- Anodized (film thickness 15-25μm, salt spray test >500h)
- Zinc (≤3%) to enhance the corrosion resistance of the substrate
- Recommended for coastal areas with epoxy coating