A356 Aluminum Alloy Comprehensive Guide: Properties, Applications and FAQs
Date: 2025-04-30 Categories: Blog Views: 1689
Hyundai CastingaluminumThe most widely used material is the American Society for Testing and Materials (ASTM) grade A356 alloy, which is equivalent to China's ZL101A, Japan's AC4CH and Germany's AlSi.7Mg, France A-S7G03, Russia AлIn addition to the A356 alloy, Germany also uses AlSi9Mg, AlSi10Mg, AlSi11Mg, France also uses A-S11G, A-S12.5 . These high Si alloys are not heat-treated, they have good liquid fluidity, strong make-up shrinkage, good casting performance and few casting defects. However, the mechanical properties andmachiningArtistic performance is not as good as A356 alloy.
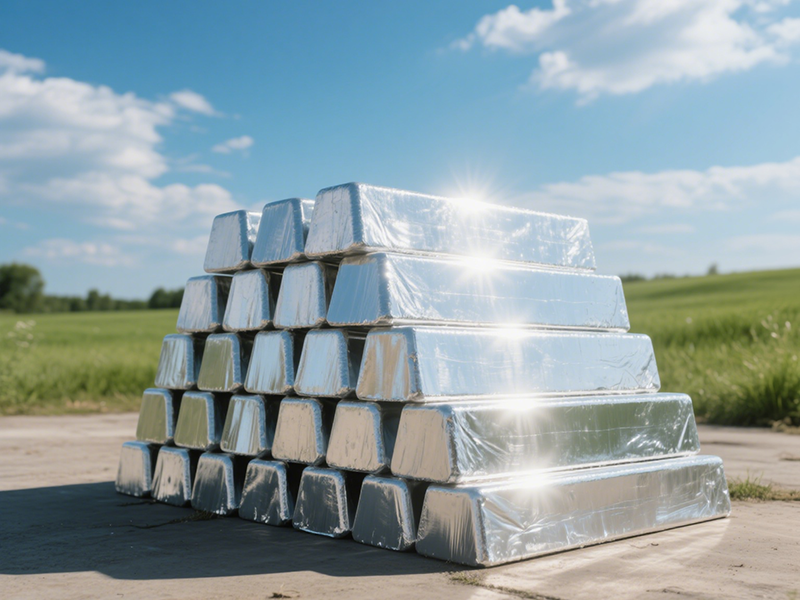
chemical composition
element symbol | Composition range (% mass, %) | Remarks (maximum allowable or other requirements) |
---|---|---|
Si | 6.5 - 7.5 | Main alloying elements for improved fluidity |
Mg | 0.25 - 0.45 | Enhanced strength and heat treatment response |
Fe | ≤ 0.20 | Impurity elements, which need to be strictly controlled |
Cu | ≤ 0.20 | Impurity elements, excess reduces corrosion resistance |
Zn | ≤ 0.10 | impurity element |
Mn | ≤ 0.10 | Impurity elements, which may affect mechanical properties |
Ti | ≤ 0.20 | Commonly used as grain refiner (can be added) |
Al | tolerance (i.e. allowed error) | base metal |
mechanical property
Performance Parameters | Typical values (sand casting) | Typical values after T6 heat treatment | note |
---|---|---|---|
Tensile strength (Rm) | 160 - 190 MPa | 230 - 260 MPa | Heat treatment significantly improves strength |
Yield strength (Rp0.2) | 80 - 110 MPa | 170 - 200 MPa | Yield strength nearly doubled after T6 treatment |
Elongation (A50mm, %) | 2 - 5% | 3 - 8% | Plasticity improves with heat treatment optimization |
Brinell hardness (HB) | 60 - 80 HB | 80 - 100 HB | Hardness is related to the heat treatment process |
modulus of elasticity | 70 - 75 GPa | 70 - 75 GPa | Less related to casting process |
Impact toughness (Charpy) | 4 - 8 J/cm² | 6 - 10 J/cm² | Affected by impurity content and grain refinement |
physical property
physical property | Typical Value/Range | note |
---|---|---|
intensity | 2.68 g/cm³ | Lightweight properties for lightweight designs |
Melting point range | 557 - 613°C | Temperature range from solid phase line to liquid phase line |
Coefficient of thermal expansion (20-100°C) | 23.0 - 24.0 µm/m-K | Correlates with temperature change |
heat conductivity | 130 - 160 W/(m-K) | Good thermal performance |
conductivity | 30 - 40% IACS | Moderately conductive, non-highly conductive alloy |
Specific heat capacity (25°C) | 0.88 - 0.96 J/(g-K) | Dependent on alloy composition and temperature |
resistivity | 4.3 - 5.5 µΩ-cm | Calculated value of the reciprocal of the corresponding conductivity |
modulus of elasticity | 70 - 75 GPa | Consistent with the modulus of elasticity in mechanical properties |
A356 Grade name and element content standard for different stages
The A356 alloy is subdivided into A356.2, A356.1, and A356.0, and their chemical compositions, respectively, are shown in the table below:
A356 at different times | A356 | Si | Mg | Ti | Fe | Cu | Zn | Mn | detergent | Other impurities | |
each | aggregate | ||||||||||
procure (for an enterprise etc) | A356.2 | 6.5/7.5 | 0.30/0.45 | 0.08/0.20 | ≤0.12 | ≤0.05 | ≤0.05 | ≤0.05 | ≤0.05 | ≤0.15 | |
melt | A356.1 | 6.5/7.5 | 0.30/0.45 | 0.08/0.20 | ≤0.15 | ≤0.10 | ≤0.10 | ≤0.10 | Sb=0.1~0.20 Sr=0.012~0.020 | ≤0.05 | ≤0.15 |
a finished product | A356.0 | 6.5/7.5 | 0.25/0.45 | 0.08/0.20 | ≤0.20 | ≤0.10 | ≤0.10 | ≤0.10 | Sb=0.08~0.18 Sr=0.008~0.018 | ≤0.05 | ≤0.15 |
A356 Aluminum Alloy Applications
A356 aluminum alloy is a "star material" in the field of automobile manufacturing, especially suitable for the production of complex shaped parts through the die-casting process. Combining light weight, high strength and corrosion resistance, it is a key material for improving vehicle performance and energy efficiency.
Why choose A356 aluminum alloy?
- lightweighting: With a density of only 1/3 that of steel, it can significantly reduce body weight and help reduce fuel consumption or extend the range of electric vehicles.
- sturdy and durable: Through heat treatment (such as the T6 process), the strength can be increased to 1.5 times that of conventional aluminum, making it easy to cope with high-load scenarios such as engine mounts and wheel hubs.
- precision castingExcellent fluidity for die casting complex structures (e.g. thin-walled parts, curved shapes), reducing subsequent processing costs.
- safe and reliable: Strictly controlled impurity content (e.g., iron, copper) ensures resistance to corrosion and fatigue in long-term use, prolonging part life.
typical application
- fuel-efficient vehicle: Engine block, transmission case, chassis mounts.
- electric powered vehicle: Battery pack housing, motor mounts, lightweight body structure.
- General area: Highly demanding components such as aerospace mounts, industrial pumps and valves.
As engineers, we optimize the casting process and heat treatment parameters to ensure that each A356 part meets the optimal balance of safety, durability and cost while being lightweight.
1. What is the difference between A356 aluminum alloy and other high-silicon aluminum alloys such as AlSi9Mg?
A356 aluminum alloy significantly improves strength through heat treatment (e.g., T6 process) and is suitable for high-load components (e.g., wheel hubs, engine mounts). While AlSi9Mg, AlSi10Mg and other alloys, although excellent casting performance (good fluidity, less defects), but without heat treatment when the mechanical properties and machinability is weaker, suitable for complex shapes but lower strength requirements of the parts.
2. Why does A356 aluminum alloy require heat treatment?
Heat treatment (e.g., the T6 process) strengthens the tensile strength by solid solution and aging from190 MPa upgraded to 260 MPaThe yield strength doubles to200 MPaThis is why it is the material of choice for key automotive components. This is an important reason why it is the material of choice for key automotive components.
3. For what areas is A356 aluminum alloy suitable?
- motor vehicles: Engine block, electric car battery shell (lightweight weight reduction of 30% or more).
- aerospace: High-strength brackets, fatigue-resistant structural components.
- industries: pump and valve housings, high heat dissipation components (thermal conductivity of160 W/m-K).
4. What is the difference between A356.0, A356.1 and A356.2?
The criteria for the three components differ slightly:
- A356.2: Impurity control is the strictest (e.g. Fe≤0.12%), suitable for precision parts.
- A356.1: Add strontium (Sr) or antimony (Sb) to refine the grain and improve casting performance.
- A356.0: General purpose grade with slightly higher impurity tolerance and lower cost.
5. How to balance the lightness and strength of A356?
By optimizing the die casting process (e.g., vacuum casting to reduce porosity) and precise heat treatment parameters (e.g., aging temperature of 155°C x 4 hours), it is possible to guarantee a density of just2.68 g/cm³(1/3 of steel) while realizing tensile strength250 MPa or more.
6. Will A356 aluminum alloy fail at high temperatures?
Its long-term use temperature is recommended not to exceed150°C. Strength decreases at high temperatures, but short-term heat resistance can be improved by grain refinement with the addition of titanium (Ti) or surface coating treatments.
7. Why are impurities (e.g., Fe, Cu) in A356 strictly controlled?
Excess iron (Fe > 0.2%) forms brittle compounds that reduce toughness and corrosion resistance; copper (Cu > 0.1%) may initiate galvanic corrosion. Strict control of impurities is the key to extending part life.