ADC12 Die-Cast Aluminum Alloy Comprehensive Guide: Compositional Properties, Mechanical Properties and Industry Applications
Date: 2025-04-14 Categories: Blog Views: 3075
ADC12(Japan JIS standard 12 aluminum) is a high-performance Al-Si-Cu system die casting. aluminum JIS H 5302-2000 standard. The alloy is known for its excellent casting fluidity, good machinability and high dimensional stability, making it particularly suitable for the production of complex thin-walled components. Its typical composition (Si 9.6-12.0%, Cu 1.5-3.5%) ensures that the material combines good strength, heat and corrosion resistance while keeping production costs low. In the automotive industry, ADC12 is widely used in the manufacture of key components, including cylinder head covers, various types of sensor housings, engine mounts, transmission components and motor housings and other structural parts. It is one of the most common materials used in the die casting industry.
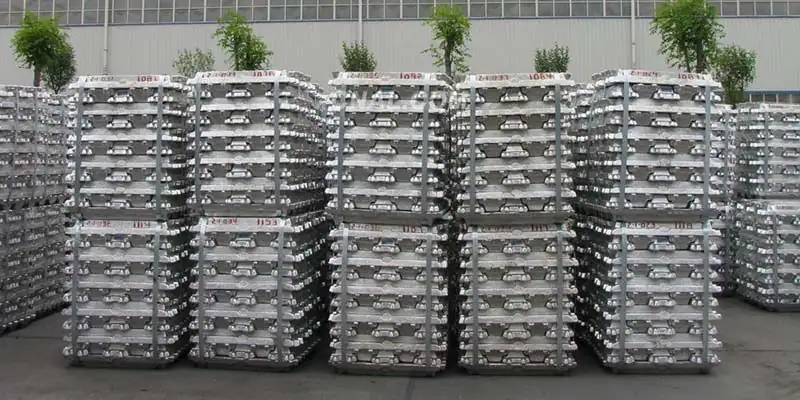
Material composition
JIS Standard | copper (chemistry) | silicon (chemistry) | milligram | zinc (chemistry) | unshakeable | manganese (chemistry) | Ni | Sn | aluminum (chemistry) |
ADC12 | 1.5-3.5 | 9.6-12.0 | <0.3 | <1.0 | <1.3 | <0.5 | <0.5 | ≤ 0.2 | Residual (85.5 is optimal) |
2. Mechanical properties
alloys | tensile strength | Hardness test | ||||||||||||
Tensile strength MPa | Endurance MPa | Elongation % | HB | HEB | ||||||||||
average value | σ | ASTM | average value | σ | ASTM | average value | σ | ASTM | average value | σ | ASTM | average value | σ | |
ADC12 | 228 | 41 | 310 | 154 | 14 | 150 | 1.4 | 0.8 | 3.5 | 74.1 | 1.5 | 86 | 40 | 1.8 |
3. Physical properties
Performance indicators | typical value | Test Standards | instructions |
---|---|---|---|
intensity | 2.68-2.71 g/cm³ | JIS H 5302 | Slightly higher than pure aluminum, due to the content of Si, Cu |
melting point | 520-580°C (solid phase line - liquid phase line) | ASTM E794 | Eutectic properties, wide casting temperature range |
heat conductivity | 96-120 W/(m-K) | JIS H 0505 | Better thermal performance than A380 |
Coefficient of linear expansion | 21.5×10-⁶/°C (20-100°C) | JIS H 5401 | Close proximity to cast iron reduces thermal stress |
resistivity | 50-55 nΩ-m | JIS H 0505 | Not suitable for high conductivity requirements |
specific heat capacity | 880-920 J/(kg-K) | ASTM E1269 | Comparable to most aluminum alloys |
4. Applications
Automotive
New Energy Battery Casing: Balancing Heat Dissipation Needs with Lightweight Targets
Sensor holders: low shrinkage for assembly accuracy
3C electronics
Thermal Substrates for 5G Devices: Taking Advantage of Thermal Conductivity and Circumventing Anodizing Process Limitations
appliance component
Power tool housings: Reducing unit costs by optimizing the casting system
5. Advantages
- High strength and light weightExcellent mechanical properties combine tensile strength with lightweight characteristics to meet safety standards for automotive load-bearing components;
- Precision molding capabilityHigh silicon content gives excellent fluidity and filler properties, stable molding of 0.5mm grade thin-walled parts, the pull-out angle is reduced by 15%-20% compared with conventional alloys, significantly enhancing the freedom of mold design;
- Process Friendliness: Low cutting resistance and not easy to stick the knife, machining efficiency is improved by about 30% compared with similar materials;
- dimensional stability: Solidification shrinkage is only 0.5%-0.7%, and the tolerance accuracy of complex structural parts can reach CT6 level;
- Surface treatment suitability: Excellent adhesion of spraying and plating, with the rate of blisters lower than the industry average, especially suitable for automotive exterior parts;
- Balanced corrosion resistance: Corrosion resistance is superior to ordinary aluminum in conventional environments, but needs to be coated for protection in salt spray environments.
Faqs
Q: Is welding repair of ADC12 die castings feasible?
A: MIG welding can be used to repair, but need to control the heat input to avoid grain coarsening
Q: How to reduce die casting porosity?
A:Ningbo Hexin can control the porosity below 2% by vacuum-assisted die-casting technology.